3 lubrication and information, Hydraulic system, Hydraulic oil – JLG 450A_AJ Series II Service Manual User Manual
Page 36: Changing hydraulic oil, Lubrication specifications, 4 cylinder drift test, Platform drift, Cylinder drift, Lubrication and information -4, Cylinder drift test -4
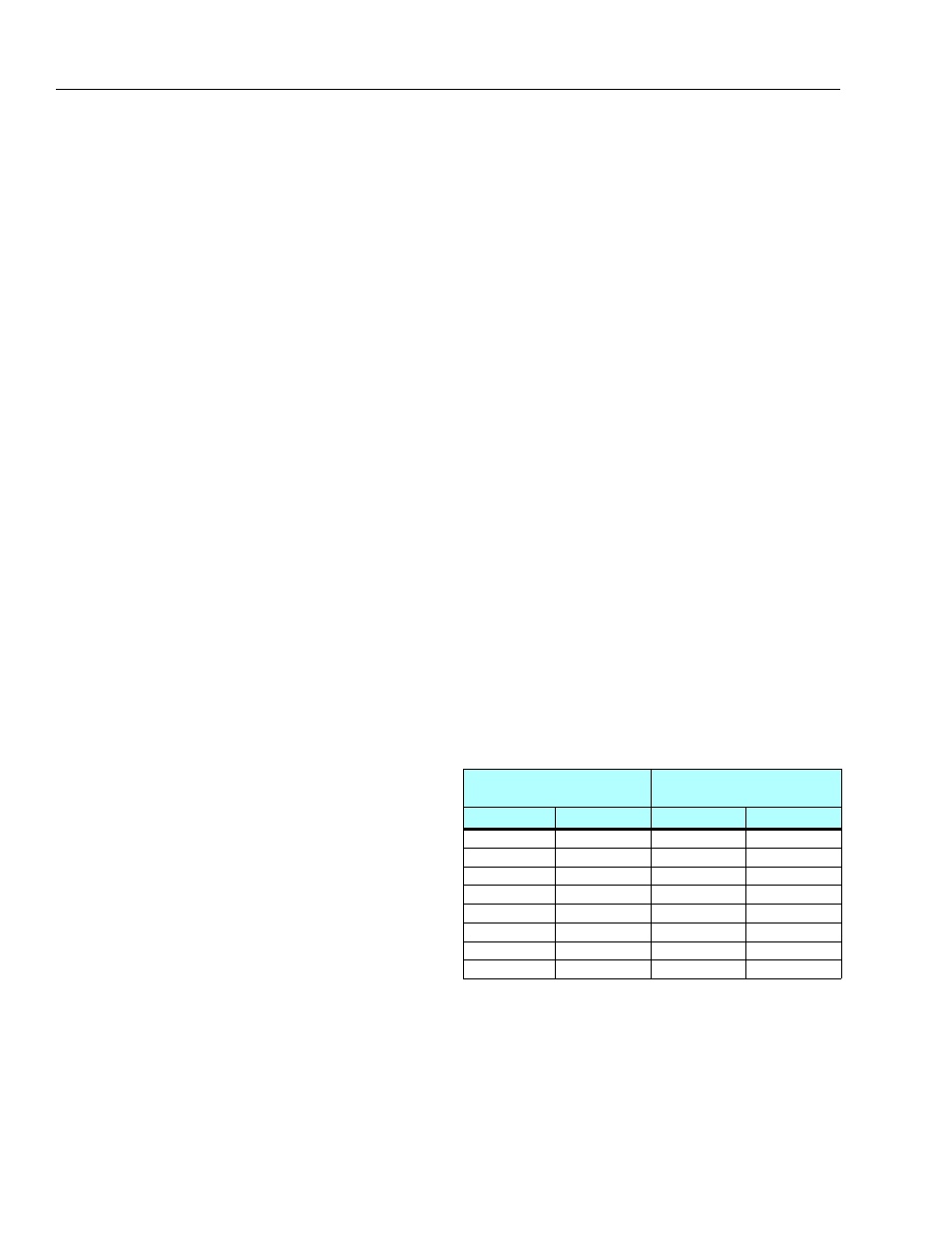
SECTION 2 - GENERAL
2-4
– JLG Lift –
3121290
2.3
LUBRICATION AND INFORMATION
Hydraulic System
1.
The primary enemy of a hydraulic system is contamina-
tion. Contaminants can enter the system by using inade-
quate hydraulic oil allowing moisture, grease, filings,
sealing components, sand, etc., to enter when perform-
ing maintenance, or by permitting pump to cavitate due
to insufficient system warm-up or leaks in pump supply
(suction) lines.
2.
Design and manufacturing tolerances of component
working parts are very close, even the smallest amount
of dirt or foreign matter entering a system can cause
wear or damage to components and generally results in
faulty operation. Every precaution must be taken to
keep hydraulic oil clean, including reserve oil in storage.
Hydraulic system filters should be checked, cleaned,
and/or replaced as necessary, at specified intervals
required in the Lubrication Chart in Section 1. Examine
filters for metal particles.
3.
Cloudy oils indicate a high moisture content which per-
mits organic growth, resulting in oxidation or corrosion.
If this condition occurs, the system must be drained,
flushed, and refilled with clean oil.
4.
It is not advisable to mix oils of different brands or types,
as they may not contain the same required additives or
be of comparable viscosities. Good grade mineral oils,
with viscosities suited to ambient temperatures in which
the machine is operating, are recommended for use.
NOTE: Metal particles may appear in oil or filters of new machines
due to wear-in of meshing components.
Hydraulic Oil
1.
Refer to Section 1 for viscosity ranges.
Changing Hydraulic Oil
1.
Filter elements must be changed after the first 50 hours
of operation and every 300 hours (unless specified oth-
erwise) thereafter. If it is necessary to change the oil, use
only those oils meeting or exceeding specifications
appearing in this manual. If unable to obtain the same
type of oil supplied with machine, consult local supplier
for assistance in selecting the proper equivalent. Avoid
mixing petroleum and synthetic base oils. JLG Industries
recommends changing hydraulic oil annually.
2.
Always keep hydraulic oil clean. If oil must be poured
from original container into another, clean all possible
contaminants from the service container. Always clean
the filter mesh element and replace cartridge any time
system oil is changed.
3.
While unit is shut down, make a thorough inspection of
all hydraulic components, lines, fittings, etc., as well as a
functional check of each system, before placing
machine back in service.
Lubrication Specifications
Lubricants specified by component manufacturers are always
the best choice. However, multi-purpose greases usually have
qualities which meet a variety of single purpose grease
requirements. Should any question arise regarding use of
greases in maintenance stock, consult your local supplier for
evaluation. Refer to Section 1 for an explanation of lubricant
key designations appearing in the Lubrication Chart.
2.4
CYLINDER DRIFT TEST
Maximum acceptable cylinder drift is measured using the fol-
lowing methods.
Platform Drift
Measure drift of platform to the ground. Lower booms (if
equipped) slightly elevated, main boom fully extended, with
rated load in platform and power off. Maximum allowable drift
is 2 inches (5 cm) in 10 minutes. If machine does not pass this
test, proceed with the following.
Cylinder Drift
Measure drift at cylinder rod with a calibrated dial indicator.
Cylinder oil must be stabilized at ambient temperature.
Cylinder must have normal platform load applied.
If cylinder passes this test, it is acceptable.
NOTE: This information is based on 6 drops per minute cylinder
leakage.
Table 2-2. Cylinder Drift
Cylinder Bore Diameter
Max. Acceptable Drift
in 10 Minutes
inches
mm
inches
mm
3
76.2
0.026
0.66
3.5
89
0.019
0.48
4
101.6
0.015
0.38
5
127
0.009
0.22
6
152.4
0.006
0.15
7
177.8
0.005
0.13
8
203.2
0.0038
0.10
9
228.6
0.0030
0.08