Aerovent IM-201 User Manual
Page 8
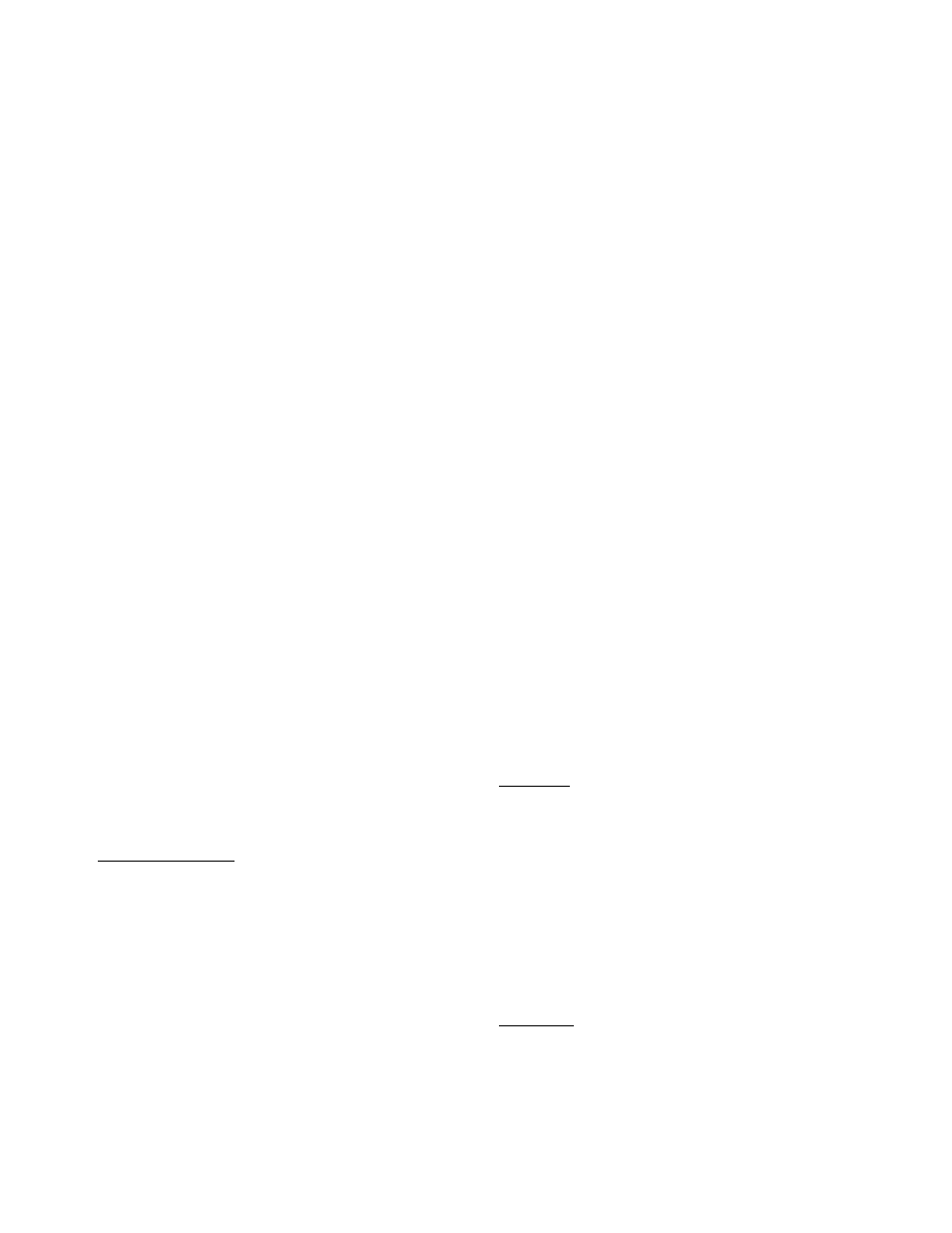
8
Aerovent IM-201
4. The motor shaft bolt (62) is now visible. After
removing it, the rotor can be pulled off the motor
shaft. Two threaded holes are provided in the face
of the hub to anchor a puller bar.
6.3 ROTOR DISASSEMBLY & INSPECTION
(Not Required For Maintenance)
If the rotor is to be serviced on site, proceed as fol-
lows.
1. Remove the diaphragm cover and diaphragm (FPAC) or
hub cover (FPMC) as per Section 6.2.
2. Remove the bolts retaining the links to the spider arms.
Mark the spider arms and blade bearing housings to
insure proper reassembly.
3. Slide the spider off the hub, using a continuous twisting
motion.
4. Remove the four socket head screws from each blade,
using an 8 mm hex key. Remove the blades from the bear-
ing housings. Remove the spring, plunger, air seal, and
grease gasket from each blade position.
CAUTION: Mark all parts to insure they will be rein-
stalled in the exact location from which they were
removed. Also, all parts must be thoroughly cleaned, and
kept clean until everything is reassembled.
5. Remove the blade shafts, blade bearing, and bearing hous-
ing from the hub. The blade shafts have been assembled,
using Loctite 242 thread sealant, so it may be necessary
to apply heat to break loose the thread; do not exceed
250°F.
6. Clean the blade bearings with solvent or kerosene.
CAUTION: Do not mix races and rollers as the bearings
should be maintained as a set.
After the bearings are clean, inspect the contact surfaces
for signs of spalling, pitting, cracks, brinelling, or smear-
ing. Replace all bearings from spare parts if there is evi-
dence of wear. If the bearings are not to be immediately
used, coat with oil and wrap in grease paper.
7. Clean the threads on the shafts with a wire brush to
remove the sealant.
8. Clean all remaining parts with solvent to remove dirt and
grease.
9. Inspect the spider bore and hub bearing surfaces for gall-
ing. Lightly dress out any surface defects with fine emery
paper and clean with solvent.
DO NOT remove the hub fairing (6) from the hub
as it will affect the rotor balance.
10. FPMC Thrust Bearing
a. Remove the three bolts holding the grease re-tainer
plate inside the hub cover. Remove the bearing nut and
lock washer from the shaft. Then withdraw the shaft
and attached clevis from the bearing.
b. Check the thrust bearing for wear. If loose or noisy,
press out the bearing and replace with a new part from
spares. Apply Loctite 271 between bearing O.D. and
cover.
6.4 ROTOR ASSEMBLY
To assemble the rotor proceed as follows:
NOTE: An 8 mm hex key with a square drive adaptor
fitted to a torque wrench is required.
1. Grease the blade bearings with Chevron SRI-2 or equal and
assemble on shaft with bearing retainer.
NOTE: It is important to maintain clean conditions when
lubricating bearings.
All parts requiring Loctite must be clean and free of oil
and dirt or Loctite will not cure completely. To clean, use a
non-lubricating cleaner such as trichlorothane.
2. Apply Loctite grade T. Primer to blade shaft threads and
hub threads. Allow to air dry 5 minutes. Apply Loctite 242
to the threads of the shaft. Screw into the hub until the bolt
bottoms firmly on the shoulder. Torque to 60 ft-lbs.
3. Assemble blade, spring, plunger, plastic washer (24) and
new grease gasket (30) to bearing retainer. The proper ori-
entation is as follows when looking at the open end of the
rotor.
a. Position blade into fairing with the concave surface
facing the mechanic and the longer trailing edge of the
blade to the right.
b. Position bearing retainer with counterbalance lug facing
the mechanic and link lug to the right at about a 45-
degree angle to the blade.
c. The washer fits between blade and bearing retainer
inside the fairing.
d. The spring, plunger, and gasket fit between the blade
and shaft. Tighten the three 12M x 70 bolts to 70 ft-lbs
with the 8 mm hex key and torque wrench and the 12M
x 35 bolts to 60 ft-lbs.
4. Clean the spider, teflon insert, and hub with a solvent
to remove any dirt and grease. Carefully inspect the hub
and spider bearing surfaces for signs of galling. Lightly
dress out any surface defects with fine emery cloth and
thoroughly clean with solvent. Inspect the teflon insert for
excessive wear. Replace insert if needed. Apply a thin layer
of lithium base grease such as Chevron SRI-2, or equal, to
the sliding cylindrical surfaces.
NOTE: If your spider does not have the teflon insert, fill
the annular cavity in the spider bore with grease.
5. Replace the spider on the hub using the same twisting
motion to prevent jamming. Check that the spider slides
freely on the hub. If not, repeat Step 4. Position the spider
as marked in Step 2 of Section 6.3.
6. If the link bearings show any perceptible play or are fro-
zen, replace all the links with new parts from spares. Use a
torque wrench to tighten the bolts to 25 ft-lbs. Check that
the mechanism operates freely as the spider is moved in
and out. See note on page 11.
7. FPAC Only (Refer to Section 6.5)
a. Replace the diaphragm with a new part from spares.
Using a torque wrench, progressively tighten opposite
bolts to 25 ft-lbs.
NOTE: The crown in the diaphragm fits inside the dia-
phragm cover.
b. Replace the rotary union (33) with a new part from
spares. Clean and prime the threads with Loctite grade
T primer, allow to air dry five minutes, and apply Loctite
stainless steel PST. Tighten until firmly seated on shoul-
der.
c. Replace the springs, stud bar, and nuts on the studs
maintaining the position recorded in Step 1 of Section
6.2. Tighten the jamb nuts to 24 ft-lbs.
8. FPMC Only (Refer to Section 6.5)
a. Replace the thrust bearing if it has been removed after
packing it with Chevron SRI-2. Replace the bearing
shaft, lock washer, and bearing nut, and pack the cavity
with grease. Replace the spacer, grease retainer plate,
and the three bolts.
b. Replace the hub cover in the position marked in Step 3
of Section 6.3. Tighten the bolts to 25 ft-lbs.