Aerovent IM-201 User Manual
Page 4
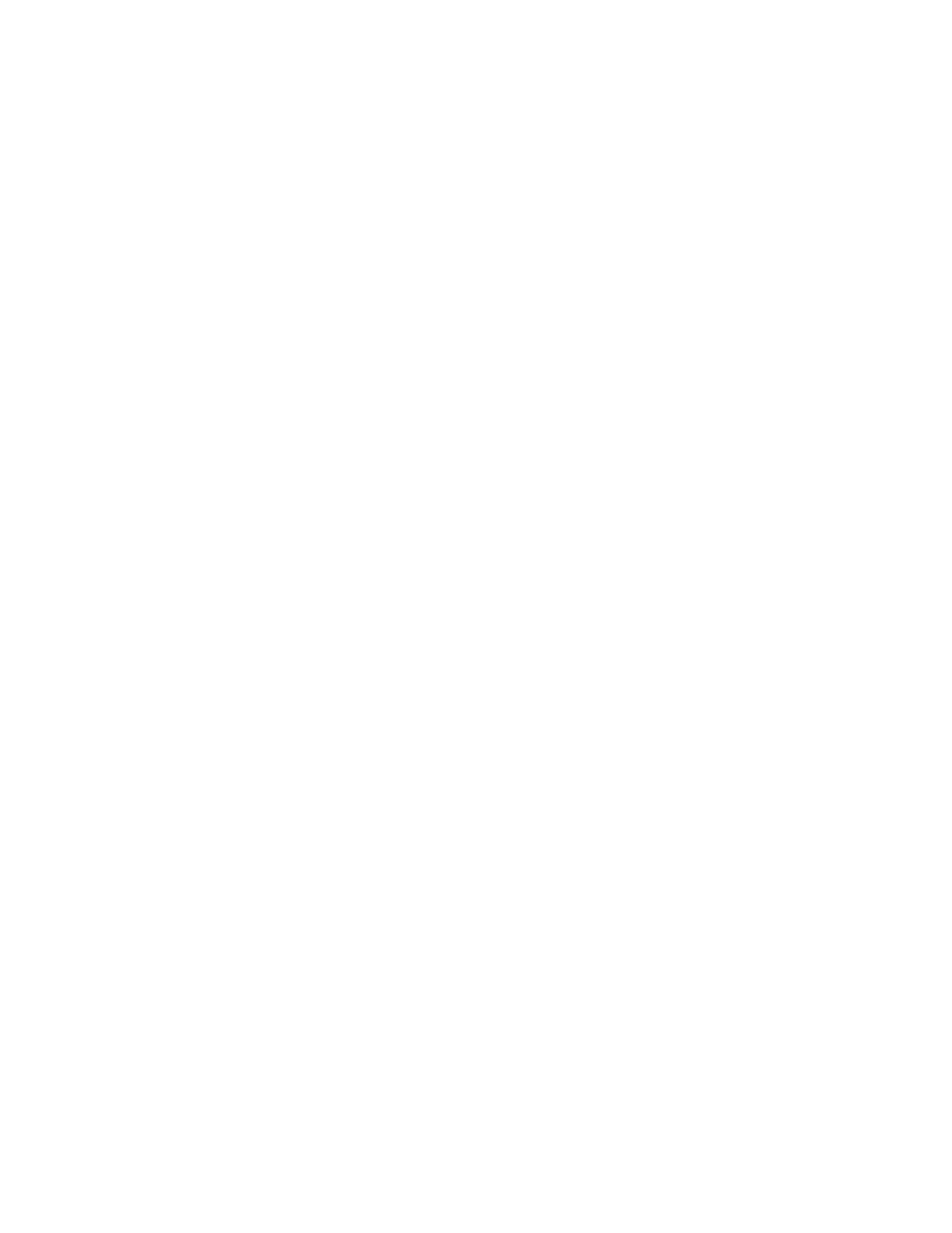
4
Aerovent IM-201
5. Reconnect air line from the diaphragm to the positioner.
6. Proceed with the positioner calibration, as described
below:
a. Connect a
1
∕
4
-NPT pressure regulator to the instrument
port to simulate a control pressure.
b. Turn on the supply air. Adjust the regulator to 9 psig
control pressure.
c. The mark on the cam should point to the center of the
cam follower. If not, turn spring adjusting nut to align
the mark.
d. Replace the cover plate and reconnect the control pres-
sure line to the middle port.
e. The positioner is now adjusted and calibrated to provide
linear blade pitch control from a 3 to 15 psig control
pressure.
NOTE: It is advised that a 0-30 psi pressure gauge of
known accuracy be used during the calibration proce-
dure.
NOTE: In the event that a positioner has to be replaced
with a new part, the pin in the slotted arm on the new
part should be placed in the identical position as on the
old one. Specifically, the slot marking should match the
distance between the marks made on the cable in item 3
of the adjustment instructions above.
3.1.5 Air Consumption
The bleed rate of the positioner is zero. Under oper-
ating conditions, an FPAC fan will use a maximum of 0.25
SCFM of supply air.
3.2 FPMC FAN
The FPMC fan is a mechanical version of the AXICO
fan. Pitch control is achieved by a mechanical linkage con-
nected to a thrust bearing in the hub cover. This arrangement
is available in three versions:
1. FPMC with electric operator mounted on the outside of
the vane section.
2. FPMC with a manual gear/jack mounted inside the core
of the vane section, and a handwheel mounted on the side
of the vane section to adjust pitch. This version can be
adjusted while the fan is running.
3. FPMC with the same linkage as on the motor-operated
version, but the input end of the linkage is clamped in one
position on a quadrant. This version cannot be adjusted
while the fan is running.
3.2.1 FPMC, Electric Motor Operator
The 120 VAC operator is used with FPMC fans. This
operator provides position proportion control of the AXICO
mechanical blade linkage. The operators are furnished with
end limit switches which have been factory set to match mini-
mum and maximum pitch conditions required for each fan.
The motor will rotate the output shaft through an arc of 150°,
but the switches have been set to give the necessary linkage
stroke within this 150° arc. Operating time is 60 seconds for
the full 150°, so on an AXICO fan the time will be somewhat
shorter. The motor has a 135 ohm balancing slide wire which
must also be connected to the control relay. The motor is also
equipped with a 135 ohm feedback slide wire to permit an
output signal which can be used as the input signal to a second
relay which would control a parallel fan.
3.2.1.1 Control
Since fan pitch is being used to control duct system
static pressure in the majority of cases, a pressure sensing
transducer or slide wire bridge must be used in conjunction
with a balancing relay. This relay will operate a single pole
double throw switch to feed power of the correct polarity
to the operator motor to achieve CW or CCW rotation of
the output shaft. If the balancing slide wire is not connected,
the motor would run until the limit switch cuts power to the
motor in that circuit direction. Not until polarity is reversed
would the motor operate, and then it would go through full
stroke in the opposite direction until the second limit switch is
opened.
By connecting the balancing slide wire circuit back
to the balancing relay, the relay is now able to compare the
requirements of the duct sensor with the actual rotation of the
operator, and the comparison will make or break the SPDT
switch, changing operator rotational direction in a stepping
manner. Thus, the system becomes proportional.
3.2.1.2 Actuator Electrical Connection
All electric connections should be in strict accor-
dance with the job specification and local electric codes. Refer
to the current manufacturer's owner's manual for a schematic
wiring diagram.
3.2.1.3 Actuator Replacement
The actuator is factory adjusted to provide the
full range of blade pitch movement. Should the actuator be
replaced, the limit switches must be adjusted to prevent the
motor from stalling at the maximum and minimum pitch posi-
tions.
To replace the actuator proceed as follows:
1. Remove the crankarm from the motor shaft without dis-
turbing the ball joint and pushrod location.
2. Remove wiring and mark terminal locations.
3. Remove four mounting bolts and replace actuator with
new unit.
4. Remove four screws from the end cover and remove the
cover.
5. Connect 120 VAC power to the proper terminals, accord-
ing to the owner's manual, to drive motor to mid-position
of shaft rotation as indicated by wiper arm location.
6. Move pitch control lever to mid-position and install cran-
karm on motor shaft.
7. Drive motor counterclockwise, according to the owner's
manual, to the maximum pitch position.
8. Adjust limit switch (LS1), according to the owner's man-
ual, to open at this position.
9. Drive motor clockwise, according to the owner's manual,
to the minimum pitch position.
10. Adjust limit switch (LS2), according to the owner's man-
ual, to open at this position.
CAUTION: Check that the limit switches are properly
adjusted and that the actuator motor does not stall at
either of the two extreme positions.
11. Reconnect wiring, according to the owner's manual, and
replace covers.
3.2.1.4 Actuator Linkage Adjustment
Should the linkage be removed during fan disassem-
bly, it may be adjusted as follows:
1. Position the pitch control lever and actuator motor at
mid-position per Section 3.2.1.3.
2. Install crankarm in an upward vertical position on motor
shaft.
3. Install ball joint on crank arm at the minimum radius
from shaft, which will permit the wiper arm to operate
within the length of the slide wire. It must not run off at
either end.