Burnham V9A User Manual
Page 28
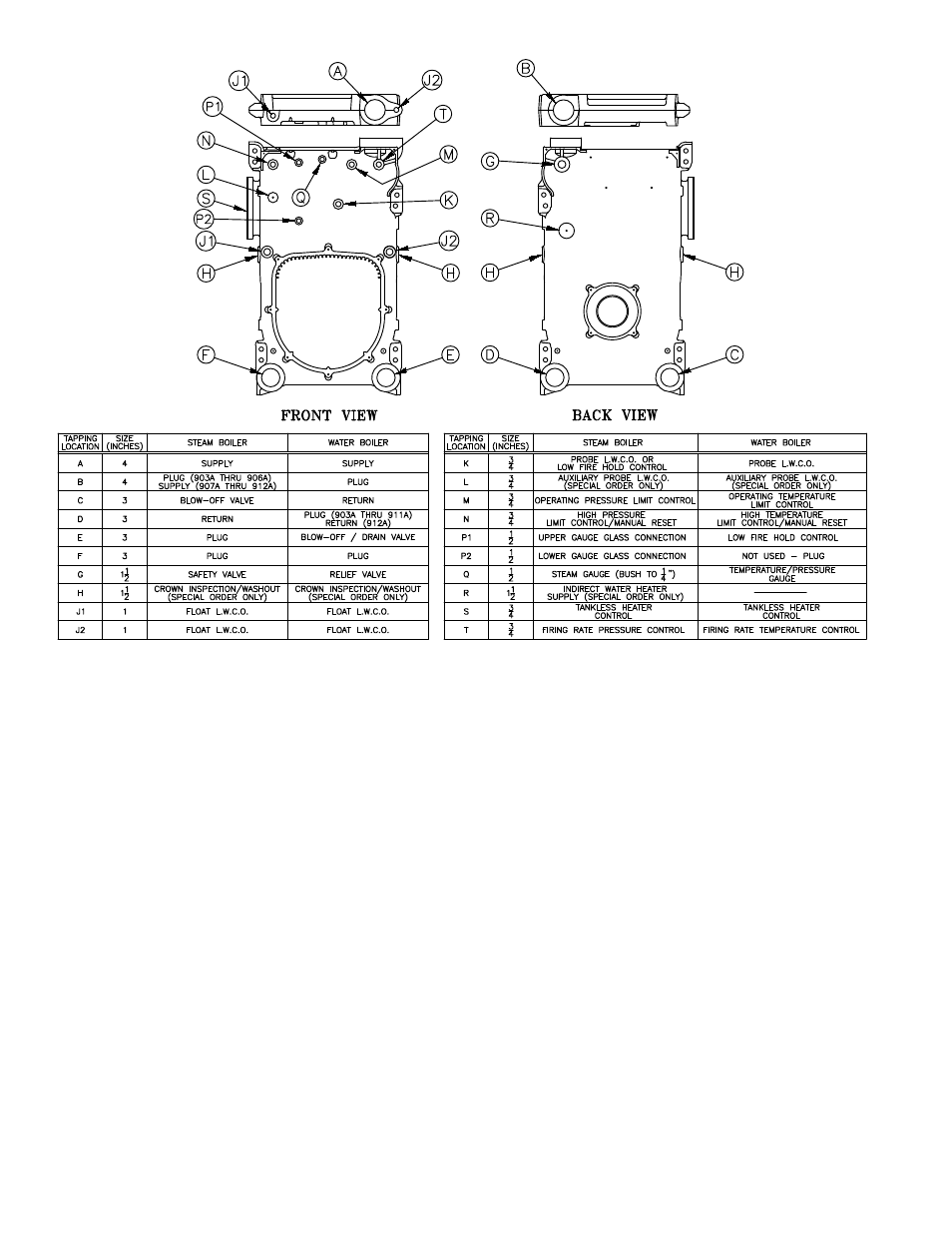
28
Figure 24: Purpose of Tappings
J.
BURNER INSTALLATION
Refer to burner manufacturer’s installation manual
for proper installation, fuel piping, wiring, burner
adjustment, burner start-up and service instructions.
Consult Section VI of this manual for burner
specifications and burner settings.
K.
PACKAGED BOILER
1. The packaged boiler comes on it’s own shipping
skid (see Figure 25) and the assembled block is
hydrostatically tested at the factory. Once the boiler
is in it’s final position, perform another hydrostatic
test at 1½ times the working pressure of the boiler.
Before boiler is put into service, all draw up rod nuts
should be loosened and then retighten to finger tight
plus 1/2 turn. The shipping skid can be used as a
housekeeping pad unless local codes say otherwise.
All controls are pre-wired down to the burner. If
burner is equipped with a lead lag panel, lead lag
controls will be shipped loose for header mounting.
The power can be supplied to the burner if equipped
with a control panel. If burner has no panel, the
power is supplied to the J-box on the front jacket.
2. SUPPLY CONNECTIONS - Removal of top
jacket is not required to connect the supply riser(s),
however one may find it easier. Refer to Figure
26 or 27 for water boilers and Figure 32 for steam
boilers.
3. RETURN CONNECTIONS - The boiler is secured
to the shipping skid with U bolts and 3” shipping
nipples. Remove the bolts and nipples. Using
3” plugs and an appropriate pipe sealant, plug
the unused return connections according to the
minimum piping recommendations. Refer to Figure
26 or 27 for water boilers and Figure 32 for steam
boilers.
4. If the boiler burner unit was factory fire tested, the
burner was adjusted to approximately 10% CO2
(gas) or 12% CO2 (oil) with an over fire pressure as
listed in the Burner Specifications, Section VI of this
manual. Final adjustments should be made once the
unit is installed and adjusted.