Preassembly inspections, Replacement guidelines – Goulds Pumps 3700 - IOM User Manual
Page 71
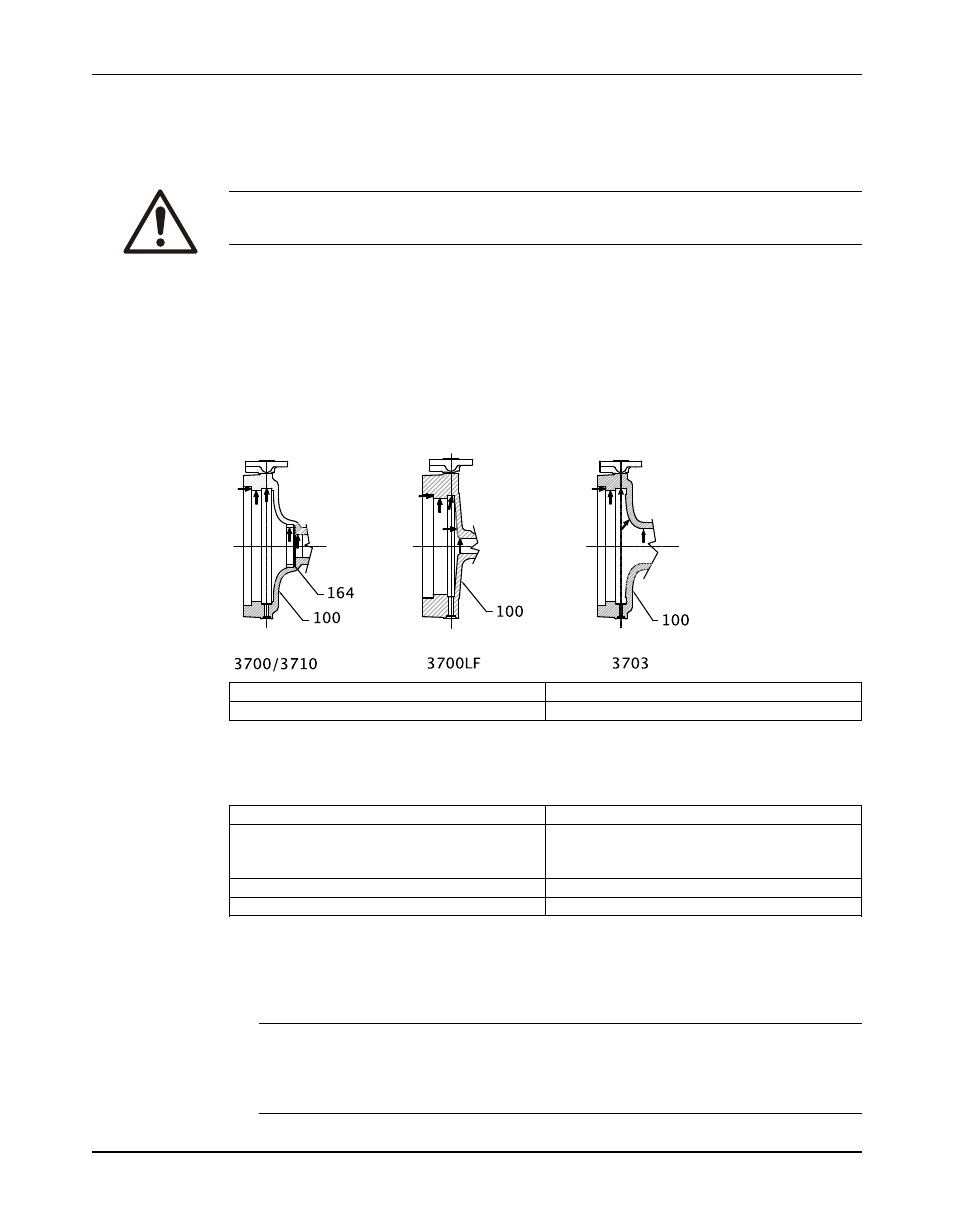
Maintenance
Preassembly inspections
Replacement guidelines
Casing check and replacement
WARNING:
Avoid death or serious injury. Leaking fluid can cause fire and/or burns. Inspect and assure gasket sealing
surfaces are not damaged and repair or replace as necessary.
Inspect the casing for cracks and excessive wear or pitting. Thoroughly clean gasket surfaces
and alignment fits in order to remove rust and debris.
Repair or replace the casing if you notice any of these conditions:
• Localized wear or grooving that is greater than 1/8 in. (3.2 mm) deep
• Pitting that is greater than 1/8 in. (3.2 mm) deep
• Irregularities in the casing-gasket seat surface
Casing areas to inspect
The arrows point to the areas to inspect for wear on the casing:
100
Casing
164
Casing wear ring
Figure 10: Areas to inspect for wear on casing
Impeller replacement
This table shows the criteria for replacing the impeller:
Impeller parts
When to replace
Impeller vanes
• When grooved deeper than 1/16 in. (1.6 mm),
or
• When worn evenly more than 1/32 in. (0.8 mm)
Pumpout vanes
When worn or bent more than 1/32 in. (0.8 mm)
Vane edges
When you see cracks, pitting, or corrosion damage
Impeller checks
• Check and clean the impeller bore diameter.
• Check the impeller balance. Rebalance the impeller if it exceeds the ISO 1940 G1.0
criteria.
NOTICE:
You must have extremely accurate tooling equipment to balance impellers to the ISO 1940
G1.0 criteria. Do not attempt to balance impellers to this criteria unless this type of tooling
and equipment is available.
Model 3700, API Type OH2 / ISO 13709 1st and 2nd Ed. / API 610 8/9/10/11th Ed. Installation, Operation, and Maintenance
69
Manual