Field calibration, 6field calibration – PNI CompassPoint Prime User Manual
Page 29
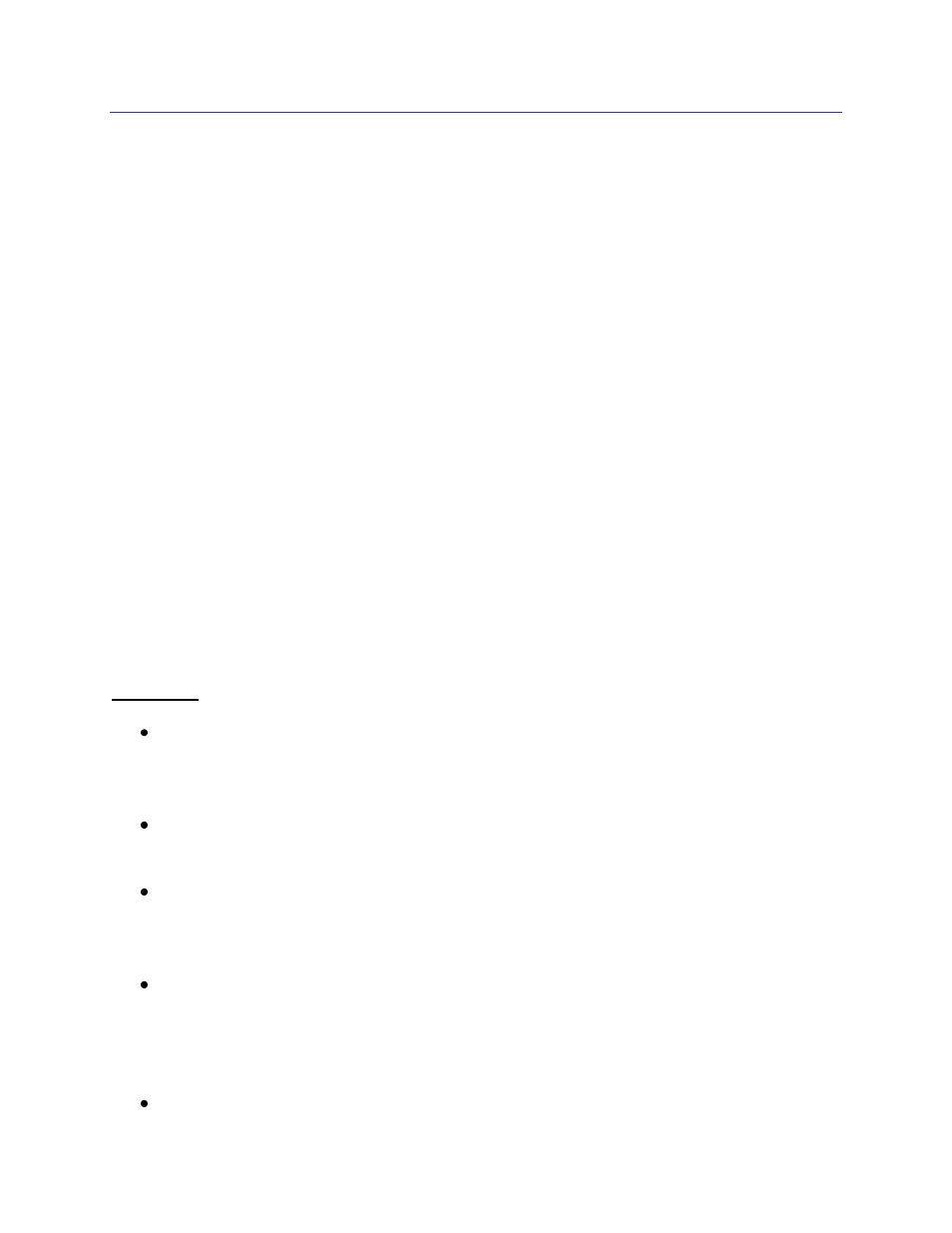
Prime User Manual r08
Page 23
6
Field Calibration
Sources of magnetic distortion that are positioned near the Prime in the user’s system will distort
Earth’s local magnetic field and need to be compensated for before implementing the Prime in
the host system. Examples of such sources include ferrous metals and alloys (ex. iron, nickel,
magnetized or non-stainless steel, etc.), batteries, permanent magnets, wires, and electric motors.
Compensation is accomplished by calibrating the Prime’s magnetic sensors while mounted in the
user’s system. In the user’s system it is expected the sources of magnetic distortion will remain
fixed relative to the Prime’s position. When performing a field calibration, the Prime identifies
the local sources of magnetic distortion and subtracts these effects from the overall reading to
provide an accurate compass heading.
Additionally, the Prime’s MEMS accelerometers gradually may change over time and it may be
desirable to recalibrate the accelerometers from time-to-time. The accelerometer calibration
procedure corrects for changes in accelerometer gain and offset. Unlike the magnetic sensors,
the accelerometers may be calibrated outside the host system. Accelerometer calibration is more
sensitive to noise or hand jitter than magnetic sensor calibration, especially for subsequent use at
high tilt angles. Because of this, a stabilized fixture is recommended for accelerometer
calibration, although resting the unit against a stable surface often is sufficient. Alternatively,
the Prime can be returned to PNI for recalibration. Since change in the accelerometers is gradual
and relatively small, accelerometer calibration is optional.
Key Points
Magnetic calibration requires incorporating the module in the user’s system such that the
magnetic components of the user’s system can be compensated for. Full sphere coverage
during calibration is ideal, but not necessary to obtain a good calibration.
Even though heading is only specified to a tilt angle of ≤45°, calibrating at >45° of tilt
generally will improve accuracy when operating near the specification limit of 45°.
Accelerometer calibration requires that the module essentially be rotated through a full
sphere of coverage. However, it does not require that the module be incorporated into the
user’s system to perform the calibration.
Magnetic and accelerometer calibration can be performed simultaneously. However, it
generally is easier to perform them separately since the requirements of each calibration
are significantly different. (Magnetic calibration requires the module be incorporated in
the user’s system, while accelerometer calibration requires full sphere coverage.)
Pay attention to the calibration scores. See Section 7.3.18 for the score meanings.