Brooks, Model 5850i – Brooks Instrument 5850i User Manual
Page 22
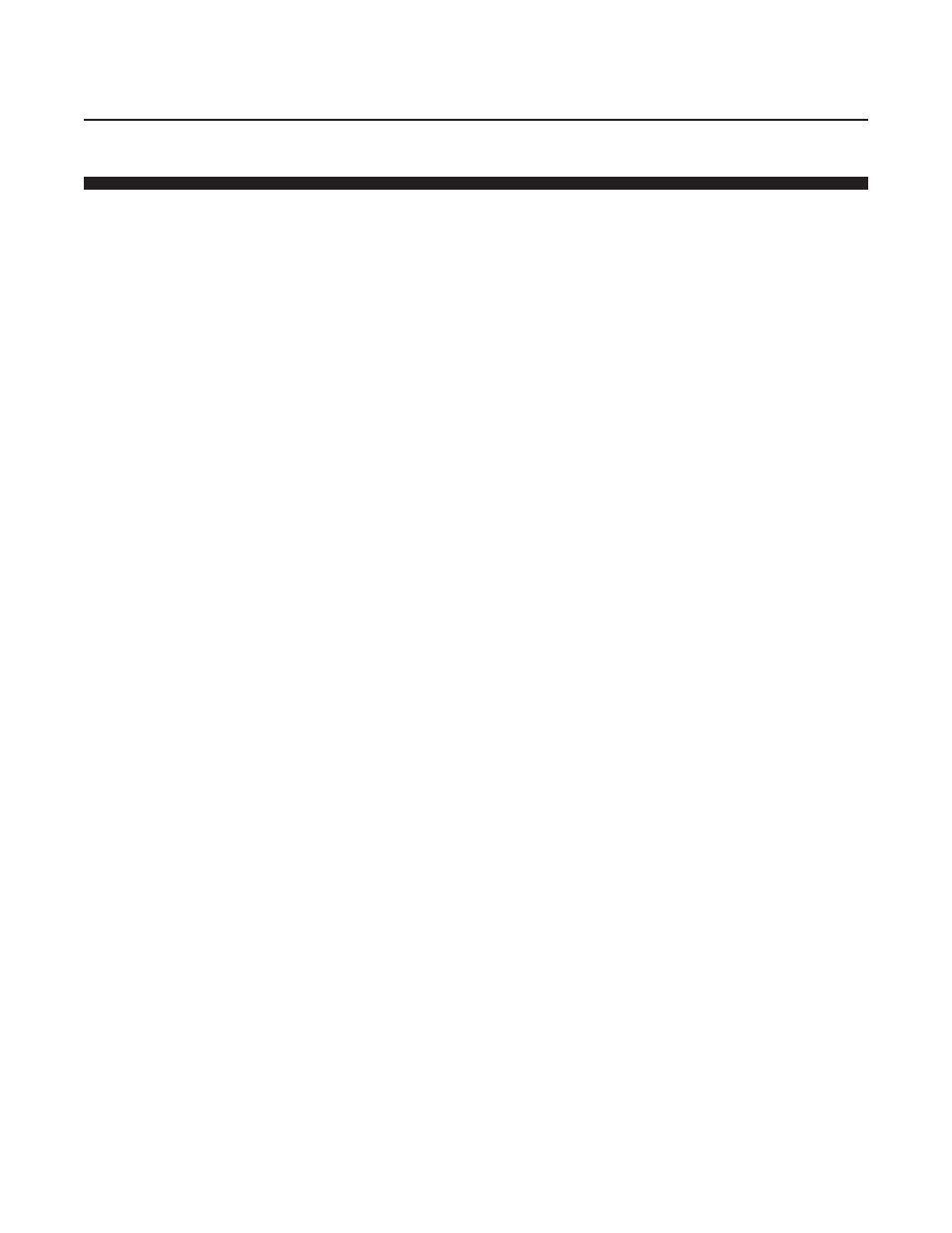
Brooks
®
Model 5850i
3-4
Section 3 Operation
Installation and Operation Manual
X-TMF-5850i-MFC-eng
Part Number: 541B108AAG
December, 2008
3-4 Calibration Procedure
NOTE 1: If the valve has been disassembled and any of the following parts
have been replaced, the control valve adjusting procedure in Section 4-4c
must be performed before the Model 5850i is calibrated.
orifice
valve stem
plunger
lower guide spring
valve seat
NOTE 2: Calibration of the 5850i mass flow controller requires the use of a
digital voltmeter (DVM) and a precision flow standard calibrator such as the
Brooks Vol-U-Meter. It is recommended that the calibration be performed
only by trained and qualified service personnel.
NOTE 3: If the mass flow controller is to be used on a gas other than the
calibration gas, apply the appropriate sensor conversion factor. Size the
orifice for actual operating conditions (refer to Section 4-5).
a. With the controller installed in an unpressurized gas line, apply power
and allow approximately 45 minutes for warm-up. During the warm-
up, adjustment and calibration check procedures, do not allow the
control valve to open when gas flow is not present. This situation is
not a normal operating mode; it will cause the control valve to
abnormally heat up. A meter with an abnormally warm valve will be
difficult to calibrate. This situation can be prevented by the valve
override “closed” when there is no gas flow, or setting the setpoint to
less than 1%. Also avoid unnecessary periods with the valve over-
ride “open.”
b. Adjust the anticipate potentiometer fully clockwise (twenty turns).
Then adjust the anticipate potentiometer ten turns counterclockwise
to center the potentiometer. This will provide a rough adjustment of
this circuit and make the flow more stable for calibration.
c. Connect the DVM positive lead to the 0-5V signal output (pin 2) and
the negative lead to signal common (TP4). Adjust the zero potenti-
ometer for an output of 0mV ±2 mV.
d. Apply pressure to the system and insure that the zero signal repeats
within 2 mV of the voltage set in step “c” above. If the zero does not
repeat, check for leakage.
NOTE: Controllers supplied with all-metal valve seats do not provide tight
shut-off. A 0-8% leak-through is typical. For metal seat controllers, close a
downstream shut-off valve and observe the zero signal.
e. Adjust the setpoint for 100% flow (5.000V or 20 mAdc). Connect the
DVM positive lead to TP2 (linearity voltage) and the negative lead to
TP4 (signal common). Adjust the linearity potentiometer for an
output of 0.0V (zero volts).