System dismantling and disposal, Important safety precautions – FlexLink X45 (43 мм) Тех. обслуживание User Manual
Page 19
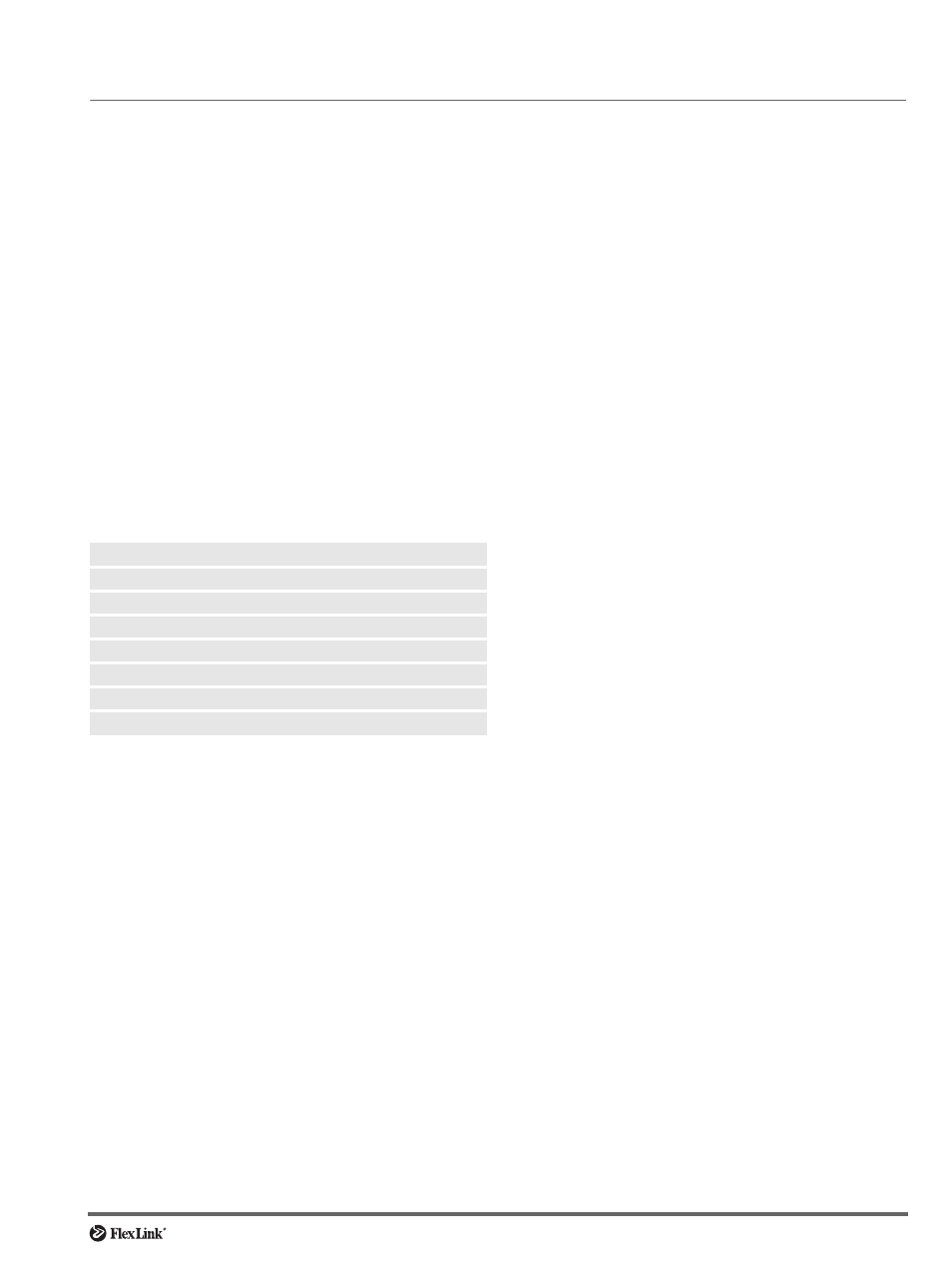
System dismantling and disposal
19
System dismantling and disposal
Important safety precautions
Dismantling
Dismantling of the FlexLink conveyor system should be
carried out by competent persons, who are familiar with
the equipment being decommissioned.
In the absence of detailed information, every care
should be taken to ensure that all items are securely
retained during the decommissioning process. This is to
ensure that the equipment remains stable and will not fall
if left unattended.
If pneumatics or hydraulics are to be decommis-
sioned, special attention should be given for the safe
release of any accumulated pressure from within the cir-
cuitry. All reservoirs/accumulators must be depressu-
rised prior to removal.
If there are any doubts as to the most suitable proce-
dure for decommissioning, then consult the equipment
supplier.
Conveyor system XS, XL, XM, XH, XK, and XB
To dismantle a FlexLink conveyor the following tools are
required.
1 Remove any remaining product from the conveyor
system.
2 Switch off all electrical power and disconnect all pneu-
matic and hydraulic feeds, including accumulators.
Ensure that system is safe by shutting down all feed
supplies or removing electrical fuses.
3 Remove the black transmission cover from drive unit
to expose slip clutch and transmission drive chain.
4 The locking effect of the slip clutch can be removed by
removing the transmission chain or by releasing the
slip clutch (section in maintenance and service refers
to slip clutch adjustment).
5 Remove the motor gear unit from the conveyor drive
assembly. The motor gear unit may be fitted with an oil
breather. Ensure that the oil from the gearbox cannot
leak into the surrounding area when decommis-
sioned. Oil should be drained from the gearbox and
disposed of in accordance with local environmental
regulations.
6 Remove guide rails and guide rail brackets etc.
7 Split the conveyor chain using the pin insertion tool
and remove the conveyor chain. If removing conveyor
chain from over head conveyor special attention
should be given when removing the last few metres.
The weight of the removed chain accelerates the
removal from the conveyor beams and can cause
injury when the last links exit the extrusion. The chain
should always be removed in the conveyor working
direction.
8 Unscrew the inner grub screws from the drive unit
connector strips and remove drive end from the con-
veyor. Repeat for idler end unit.
9 Remove the slide rail on all sides of the conveyor
extrusion. Remove the slide rail retaining fixings by
drilling away the rivets or plastic screws and pulling
away the slide rail from the aluminium extrusion pro-
file.
10 Dismantle the conveyor extrusions from the support
brackets. This should be done in a systematic man-
ner, removing conveyor section by section. Where
extrusions are joined by connecting strips, first
untighten the retaining grub screws from the connec-
tion strips. It may be necessary to release the clamp
effect of the connector piece by giving a sharp tap
with a hammer.
11 Dismantle the conveyor support system into separate
components.
12 Sort different materials ready for disposal. Include a
list of the materials.
If other equipment is to be dismantled simultaneously
with the FlexLink conveyor, attention should also be
given to the interaction of the other equipment to the
FlexLink conveyor. Pneumatic equipment should be
removed from the conveyor before dismantling. Hydraulic
equipment should also first be removed to assist disman-
tling and handling of the conveyor components during
dismantling and disposal.
Ring spanners /10 mm and 13 mm size
Allen keys
Pin insertion tool XS/XL = XLMJ 4
Pin insertion tool XM = XMMJ 6
Pin insertion tool XH = XHMJ 6
Pin punch XK = XKMJ 8
Hammer
Drill to remove slide rail rivets
- X45H (43 мм) Тех. обслуживание XS (45 мм) Тех. обслуживание XL (65 мм) Тех. обслуживание X85 (85 мм) Тех. обслуживание XH (105 мм) Тех. обслуживание XK (105 мм) Тех. обслуживание X180 (182 мм) Тех. обслуживание X300 (300 мм) Тех. обслуживание XW (300–1200 мм) Тех. обслуживание X45E (макс. 250 г) Тех. обслуживание XL (макс. 3 кг) Тех. обслуживание X85 (макс. 10 кг) Тех. обслуживание XK (макс. 30 кг) Тех. обслуживание