Chiller operation and maintenance – ClimaCool IOM AR2 SERIES User Manual
Page 60
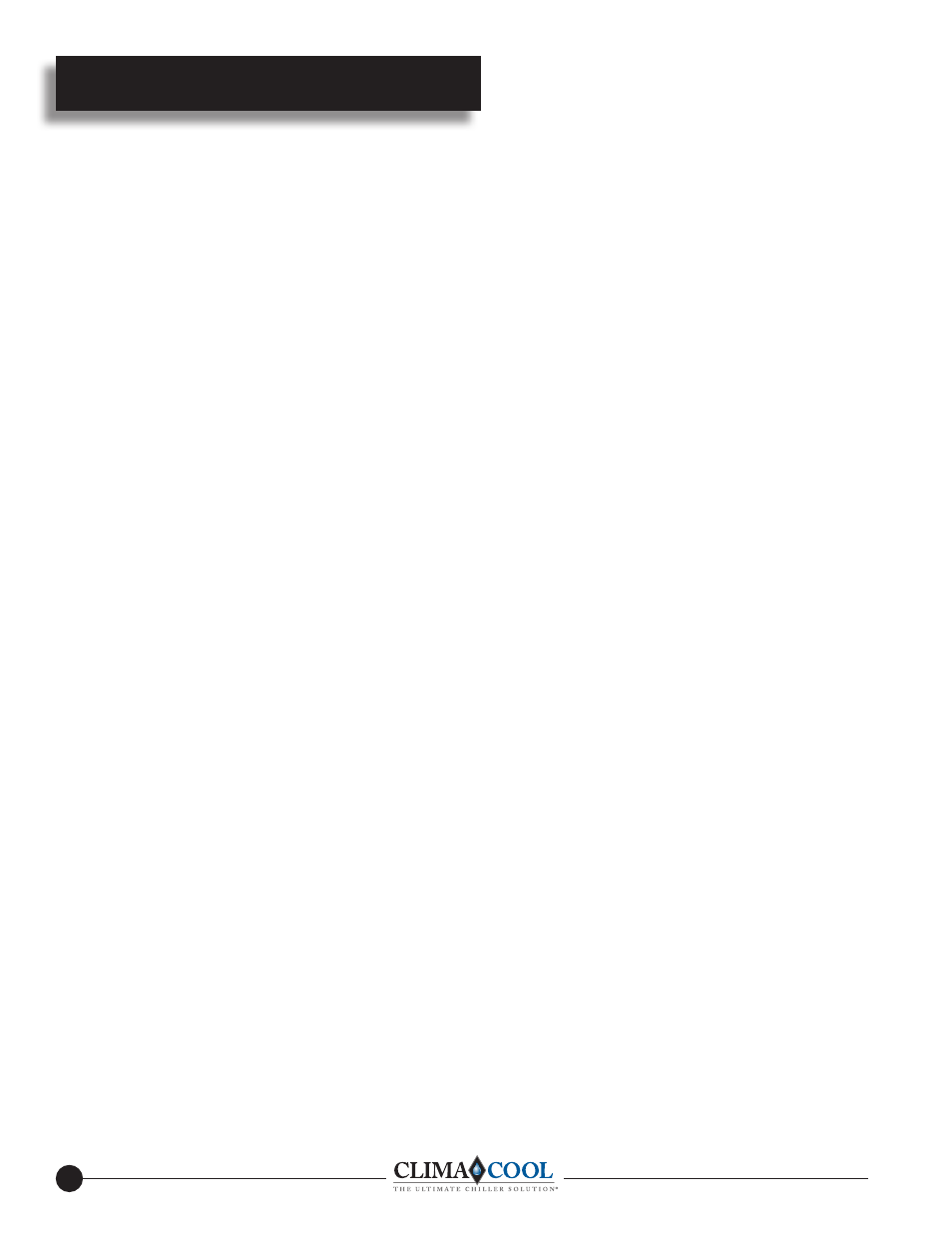
58
www.climacoolcorp.com
®
CHILLER OPERATION AND MAINTENANCE
Pressure and Temperature Log
A log of temperatures and pressures should be taken regularly .
Periodically conduct a visual inspection of the chiller to identify
problems before they reach the point of failure . As with any
mechanical system, it is necessary to conduct a series of checks to the
ClimaCool chiller to confirm correct operation .
HEAT EXCHANGERS
Back Washing
It may become evident from the recorded daily log data that the
performance of the chiller is gradually degrading . This could be
due to a buildup of debris or sludge obstructing the free passage of
flow through the heat exchangers . This debris can be removed by a
“back washing” process, which involves the introduction of a forced,
violent, backwards flow through the heat exchanger, using a carefully
formulated flushing solution . To be effective, this back flow should
be slightly higher than the normal flow, and, in the opposite direction .
The difficulties and practicality of this method depends on the back
wash pumping system itself . Another method would be to back flush
each heat exchanger using city water as opposed to system water
(see Fig . 1 page 59, City Water Cleaning Arrangement) . Note: Check
city water pressure meets requirements for back washing . The back
washing procedure is accomplished by isolating each individual heat
exchanger, and introducing the city water using a connection hose
to the 3/4” service port to flow in an opposite direction from the
“normal” heat exchanger flow direction . On the opposite 3/4” service
port, connect a drain hose to run to a suitable floor drain . Continue
back flow until all debris is removed .
Chemical in Place Washing
“Chemical Clean In-Place Washing” will typically provide the best
debris removal, even from severely clogged heat exchangers . It is
only necessary to mechanically and electrically isolate one chiller
module at a time which undergoes the “Clean In-Place Washing” .
The rest of the chiller modules can continue to operate to satisfy the
cooling load required . The cleaning tank, pump and pump strainer
should be arranged in the manner shown in Fig . 2 page 59, In Place
Cleaning Arrangement . The flow of the cleaning is arranged in the
opposite flow to the normal operational direction . Connection points
are provided using the 3/4” service ports at each heat exchanger .
The cleaning solution used can be either a detergent or hot water to
remove particles and simple cleaning . If correct water treatment has
been implemented this should provide adequate cleaning for most
situations . The solution can be pumped through the heat exchangers
and allowed to “soak” for a time and then pumped again .
If it is required to remove carbonates, then an acidic wash should be
used . A 2% solution of phosphoric or sulfamic acids in pure water are
generally acceptable . These acid solutions should only be allowed
to circulate within the heat exchanger for 10 to 15 minutes, followed
by a thorough pure water flush for 10 to 15 minutes . Hydrochloric or
sulfuric acids must not be used . In any case, you should consult the
chemical supplier to establish the correct formulation and handling
process . The materials, which will be exposed to the wash, are stated
on page 16 - Water Treatment .
Once the washing is complete, the solution should be flushed out
completely by pumping clean, fresh water through the chiller . To
achieve a reasonable level of dilution, it may be required to change
the water several times . After cleaning, the water quality and water
treatment should be confirmed .
If you have questions related to the suitability of a solution, please
contact ClimaCool for more information .
Chiller Operation and Maintenance