Specifications, Set-up – Climax PL4000 LATHE User Manual
Page 2
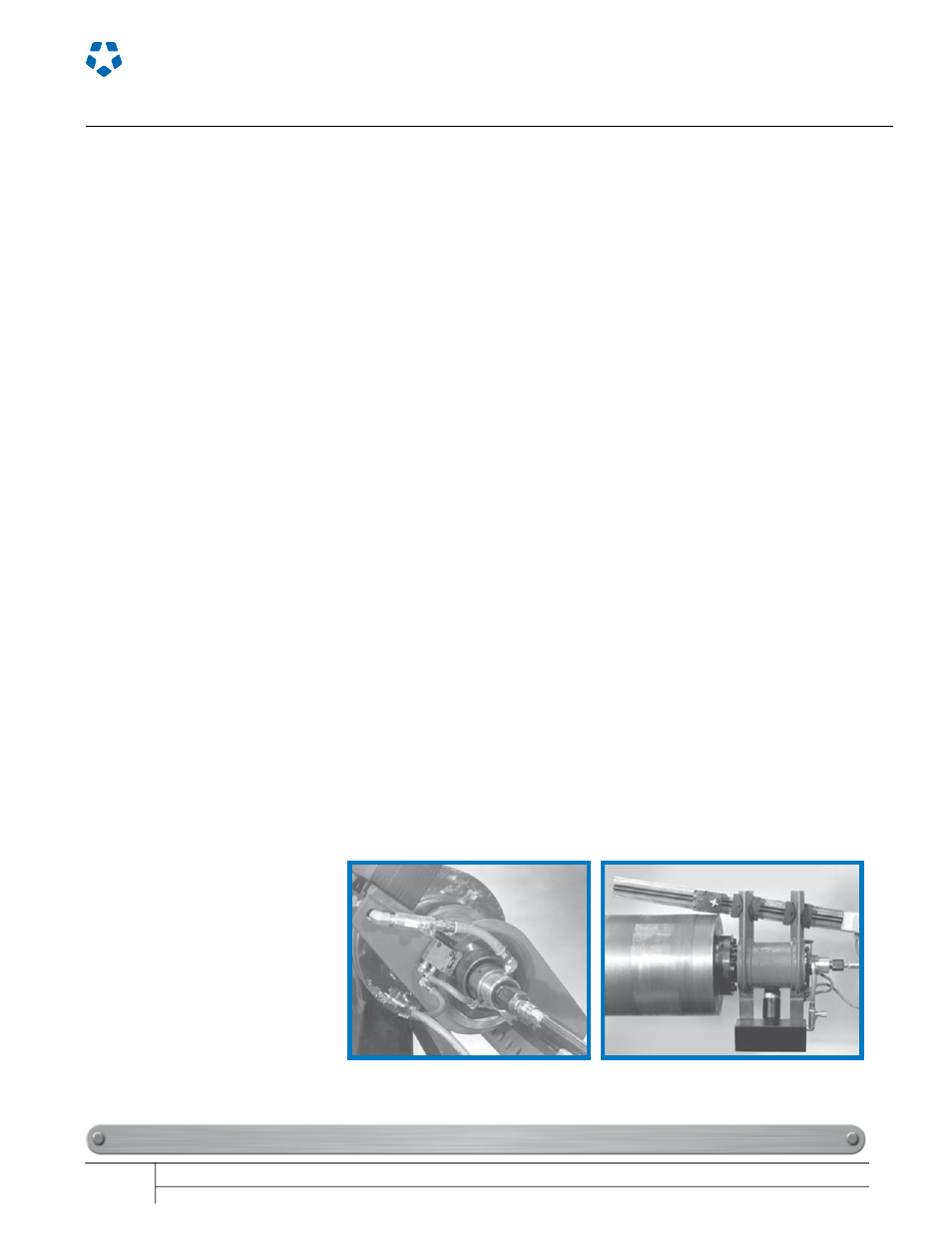
US
Metric
Climax Portable Machining & Welding Systems Web site: climaxportable.com
Worldwide Phone: 1.503.538.2185 N. America Toll-Free: 1.800.333.8311 Fax: 1.503.538.7600 E-mail: [email protected]
page 2
sPecifications
All dimensions should be considered reference. Contact your Climax Representative for precision dimensions. Specifications are subject to change without notice. There are no systems or components
on this machine that are capable of producing hazardous EMC, UV or other radiation hazards. The machine does not use lasers nor does it create hazardous materials such as gasses or dust.
Shaft diameter
Min.
8.0 inches
203.2 mm
Max. with standard tool holder
18.0 inches
457.2 mm
Max. with optional extender
24.0 inches
609.6 mm
Cutting reach
Min. with standard tool holder
0 inches
0 mm
Max. with standard tool holder
24.75 inches
628.7 mm
Min. with optional extender
3.25 inches
82.6 mm
Max. with optional extender
27.0 inches
685.8 mm
Max taper
2.5 inches/foot on diameter
63.5 mm/304.8 mm on diameter
(on 8 - 18 inch diameters)
(on 203.2 - 457.2 mm diameters)
Vertical tool travel, total
1.5 inches
38.1 mm
Tool feed, reversible
0 - 0.020 inches/rev
0 - 0.5 mm/rev.
Max. torque at tool head
450 ft-lb
610.1 N·m
Air motor
Rotational speed at max. rated Hp
520 rpm
520 rpm
Rotational speed at no-load
1100 rpm
1100 rpm
Air consumption at max. rated Hp
90 psi at 48 ft
3
/min
620 kPa at 136 cm
3
/min
Machine rotational speed
at max. rated Hp
21 rpm
21 rpm
at no-load
30 rpm
30 rpm
Cutter, square lathe tool bit
1
/
2
inch
12.7
mm
Operating weight
413 lbs
187.3 kg
Shipping weight
550 lbs
249.5 kg
Shipping dimensions
53 X 38 X 19 inches
1346.2 x 965.2 x 482.6 mm
The Portable Lathe mounts to the shaft via
a mounting plate which is drilled and coun-
terbored to match the shaft. The lathe spin-
dle then mounts to the plate on four studs.
The turning bar mounts to arms on the
main body and can be easily adjusted for
reach and turning radius.
Parallelism between the bar and the
spindle is set by adjusting two tool arm
anchors until they measure
equidistant from measuring flats on the
main body. Parallelism with the work piece
is set using jacking screws. Set screws
provide centering.
Typical set-up time is 30 minutes (once the
mounting plate is prepared).
A simple cam and valve arrangement activates the
pneumatic tool feed mechanism.
The turning bar may be set at an angle for
cutting tapers up to 2.5 inches/foot (63.5 mm/304.8
mm) on diameter.
set-uP