Climax AC5000 AUTOCLAD INTEGRATION PACKAGE User Manual
Ac5000 autoclad - integration package
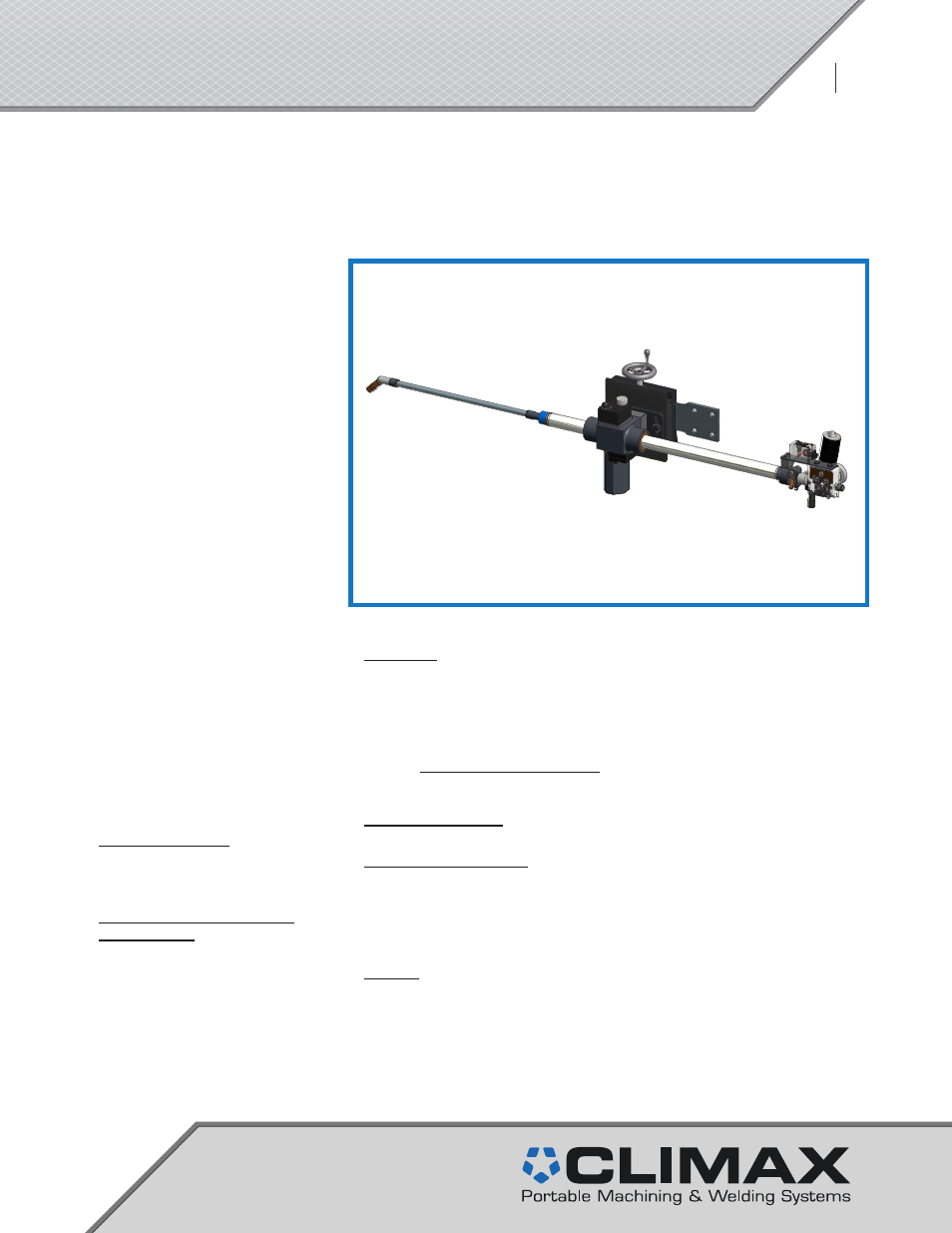
2014
AC5IP
Modular, Automated Cladding in either a full machine configuration or
as an integration package to incorporate into your existing setup.
2
AC5000 AUTOCLAD - INTEGRATION PACKAGE
The CLIMAX AC5000 AutoClad is a
great way to add automated cladding
to your arsenal. Modular options allow
you to configure either a full AutoClad
machine, or select just the components
you need to integrate automated
cladding into your existing setup.
This document contains information specific
to the Integration Package.
Please ask your salesperson about
configuring a complete machine.
Flexible & Versatile
• Select the level of integration you
need by selecting the appropriate
components to add automated
cladding to your existing setup.
• Select MIG or TIG options
• Weld diameters as small as 1.2
inches (30.5 mm) for MIG, and 2
inches (50.8 mm) for TIG, and up to
24 inches (609.6 mm) deep. And
with over 3 inches of bore size,
reach increases to 48 inches
(1219.2 mm) on certain models.
High Quality Welds:
• Achieve high-quality welds with
difficult-to-weld materials like
Nickel
Alloys, (Inconel™, Monel™,
Hastelloy™) and Stainless Steels.
• Water-Cooled Torch keeps the torch
cool, allowing long weld times,
maximizing productivity and
increasing consumable life.
• Optional wire feeding system
configurations:
Use the CLIMAX Shop Style wire
feeder and the quill mounted push
pull feeder for best wire-feeding
performance, or choose the
"feederless" version, allowing use
of the advanced MIG synergic
systems already in place at your
facility.
Simple, Safe Setup & Operation
• Cross slide provides variable torch
diameter settings. Also allows fine
adjustment of MIG stickout and TIG
arc length control. (Automatic
voltage control available for TIG
systems.)
• Use the Cross Slide Mounting Plate
to quickly mount the AC5000 Quill
Assembly to your existing setup.
Optional Offset Block provides
additional flexibility for setup.
• Optional Remote Control keeps
operator safely away from fumes,
flash, and heat, and allows operator
to make immediate changes to
welding & positioning, increasing
quality while saving time.
• Encoder allows operator to
precisely position weld start and
resume location, even when the
weld tip can not be seen.