Model mp, mpa, mpai – Xylem MPAI User Manual
Page 93
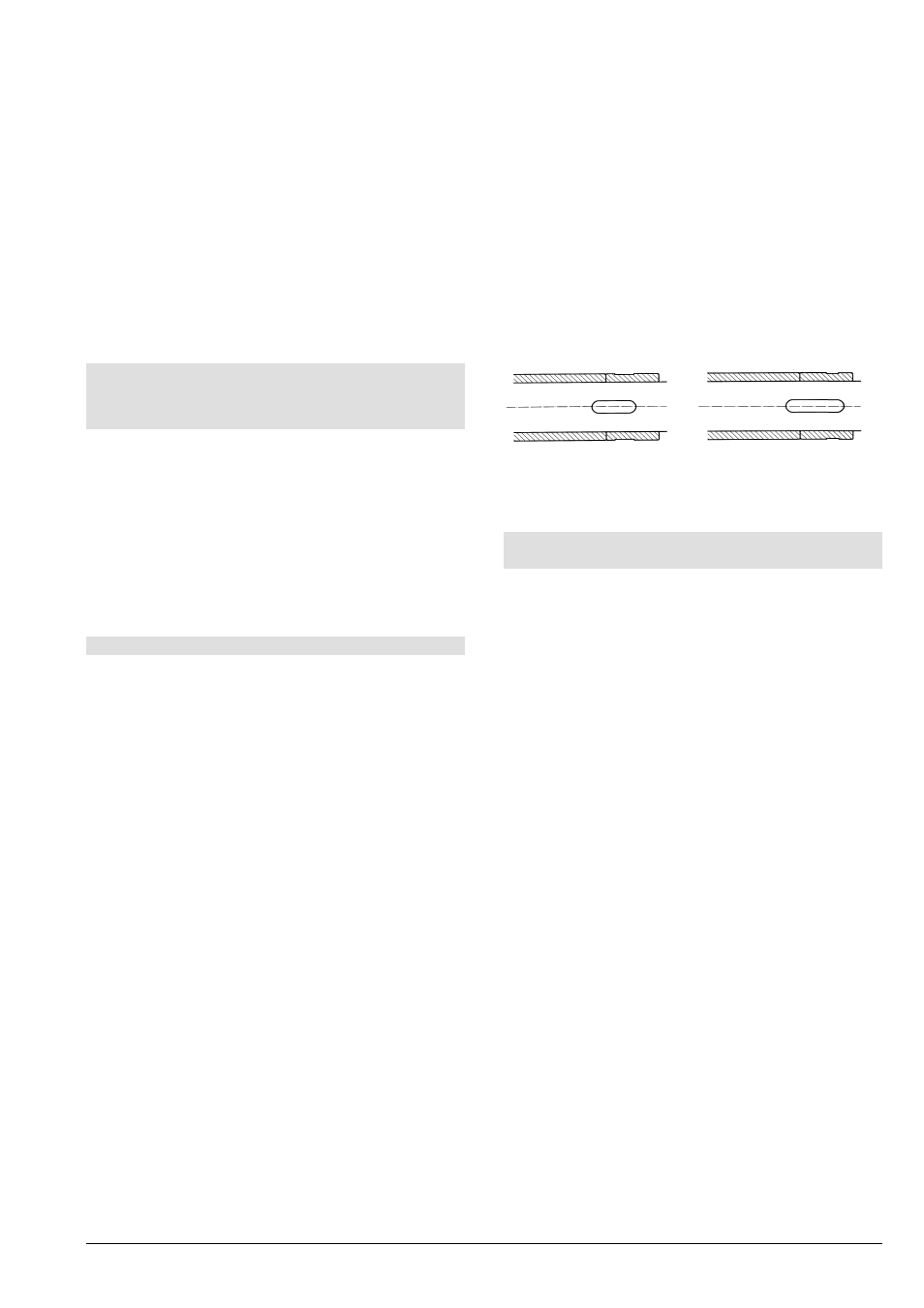
Installation, Operating and Maintenance Instruction
Model
MP, MPA, MPAI
MP 100-english
page 89
Revision 04
Article No 771074011
Issue 11/2011
Model MPAI (Baugrößen 40.1 und 40.2)
Screw on the inducer (101), thereby fix the shaft
on the coupling against twist.
Model MPAI (Sizes 65.1, 65.2, 100.1, 100.2, 125.1
and 125.2)
Insert the key (PF5) and put the inducer (101) off.
Insert the washer (29).
Tighten the first nut (28), then turn it back approx.
¼ turn, secure with the locknut.
Put the suction casing (3) in place, screw in the tie
bolts (25) and tighten the nut (M1) (see the
appendix for the tightening torque).
Turn the shaft (24) and check for easy motion.
8.7 Replacement of the shaft sleeve with a
packing gland / Replacement of the
mechanical seal
This section describes the replacement of the shaft
sleeve for designs with a packing gland or the
replacement of the mechanical seal.
Clean and check condition of all parts that have been
removed. In case of doubt, components should be
replaced. Wearing parts (roller bearings) and seals
must always be replaced.
If parts or half-open pumps are to be stored for any
length of time, they must be protected from dirt and
corrosion.
8.7.1 Model with Packing Gland (Code "P")
See the "Appendix" in the Operating Instructions for
relevant sectional drawing.
Instructions are valid for shaft seals on the intake side
(MP) and discharge side (MP, MPA, MPAI).
Dismantling
Dismantle pump on the appropriate side as
described in Point 3 (Replacing Roller Bearings)
Remove bearing cap (12), spacer sleeve (72) and
splash ring (73).
Remove feather key (PF3).
Unscrew nuts (M3) and remove packing box gland
(69).
Pull out worn packing rings (P).
Pull off shaft protective sleeve (44), draw out O-
Ring (OR4).
Depending on how worn the bearing surface is
(less than 0.5mm diameter) the shaft protective
sleeve (44) can be levelled (take finishing cut and
polish or grind). If the shaft protective sleeve (44)
is very worn it must be replaced.
Remove rest of packing rings (P) from the packing
chamber and clean all other parts. Degrease shaft
(24) but do not lubricate yet.
Assembly
Slide on O-Ring (OR4) and apply lubricant with a
brush (e.g. silicon grease).
Lubricate the shaft protective sleeve (44) in the
borehole) so that the O-ring groove remains clean
(start approx. 10-15mm inside). Standard O-rings
made of EP rubber are not resistant to oil
emulsive lubricants and must not come into
contact with them. Once resistance has been
ensured (e.g. beef dripping as lubricating agent or
oil resistant O-rings) the entire shaft (24) may be
lubricated.
Slide on the shaft protective sleeve (44), insert
new packing rings (P) (see Operating Instructions)
and fix loosely with the packing box gland (69)
(nuts (M3). When sliding on the shaft protective
sleeve (44) take care that the O-ring can slide
easily into the groove.
Insert the feather key (PF3) and slide on the
spacer sleeve (72). Pump must be assembled in
the following direction.)
MP, MPA 40, 65 and 100
MP, MPA 125
44 72
44 72
Slide on splash ring (73) and bearing cap (12)
For further assembly work see Point 3 (Replacing
Roller Bearings) "Assembly".
8.7.2 Model with Standard Rotating Mechanical
Seal (Code "SA, SB, SC, SD, SE and SF")
See the "Appendix" in the Operating Instructions for
relevant sectional drawing.
Instructions are valid for shaft seals on the intake side
(MP) and discharge side (MP, MPA, MPAI).
Shaft protective sleeves (44) and the mechanical seals
(GLRD) are different. The parts must be marked so that
they can be mounted in the same position.
Dismantling
Dismantle pump on the appropriate side as
described in Point 3 (replacing roller bearings)
Remove bearing cap (12), spacer sleeve (72) and
splash ring (73).
Remove feather key (PF3).
Remove seal cap (18). Pre-treat fitting surface
between the seal cap and the casing with branded
penetrating agent.
Slide off shaft protective sleeve (44U and 44B),
pull out O-ring (OR4).
Press out the countering of the mechanical seal
(GLRD) from the seal cap (18) using even
pressure. Attention: The seal has very sharp
edges if it breaks danger of injury
Slide the rotating unit of the mechanical seal off
the shaft protective sleeve (44). If the mechanical
seal has securing screws these must be loosened
earlier.
Clean and check all parts for wear. Mechanical
seals must always be replaced. Repairing
mechanical seals is only to be recommended with
specialist training.
Assembly
Placing the pump in a vertical position is
advantageous for assembly).
Always use a lubricant when mounting mechanical
seals. We recommend lubricating the O-ring or