5 key features – Xylem iRIS 150 GPRS DATALOGGERS User Manual
Page 10
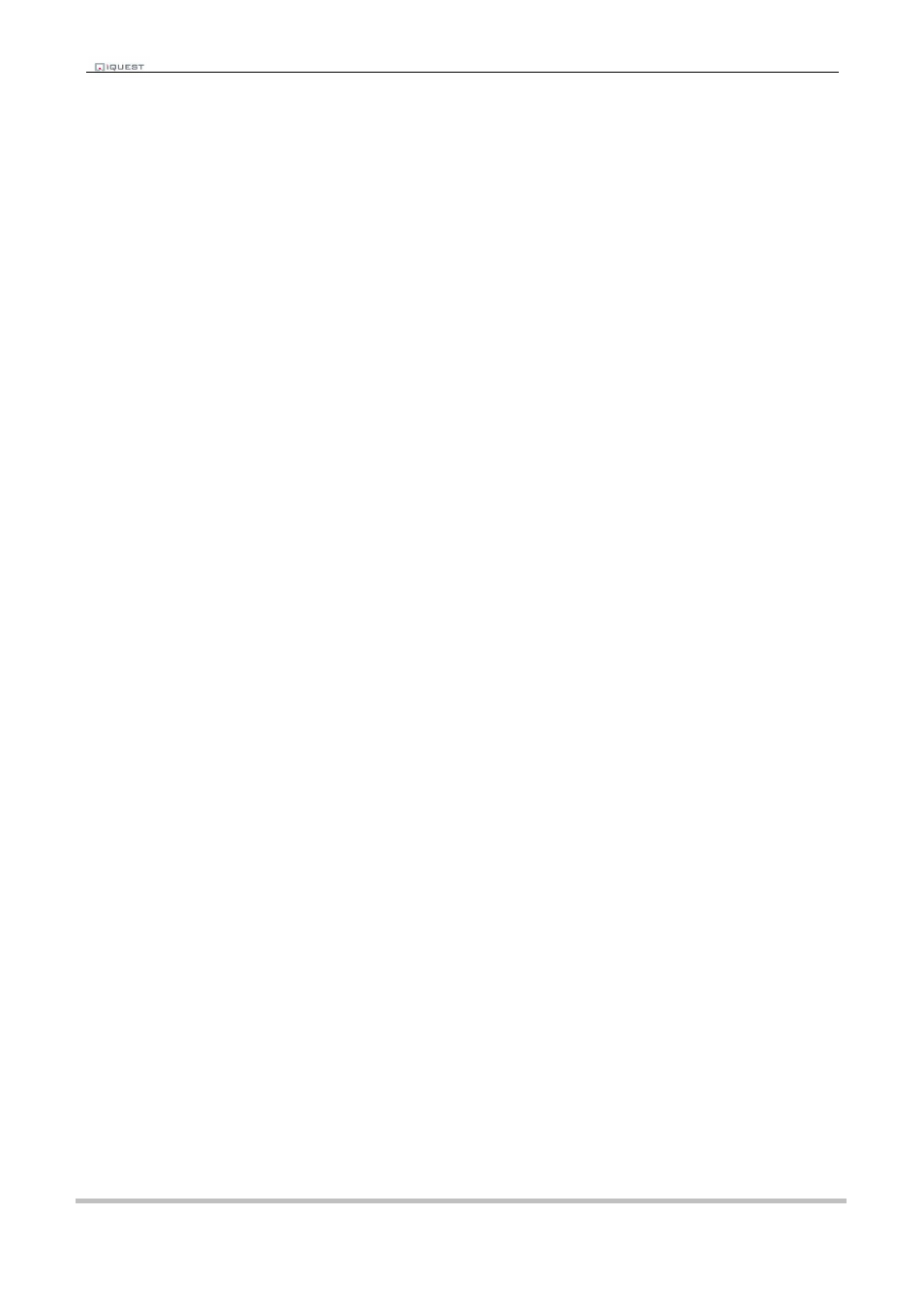
iRIS 150 V1.11 User Guide - 4
4
iQuest (NZ) Ltd - PO Box 15169, Hamilton, New Zealand Tel: +64 7 857-0810 Fax: +64 7 857-0811 Email: [email protected]
2.5 Key Features
2.5.1 Terminal Configuration
All configuration and set-up parameters are modified via a standard ASCII terminal connected to the RS232
serial interface. This means that the user can configure the device without needing to have specialised
configuration software installed on their computer specifically for this purpose. Refer to Section 5.2 for
details on the terminal configuration.
2.5.2 Data Logging
The iRIS supports the logging of data from four virtual sensors. Each of the four virtual sensors can obtain
information from one of the following ten data sources:
•
Analogue Input 1
•
Analogue Input 2
•
Pulse Counter attached to Digital Input 1
•
Pulse Counter attached to Digital Input 2
•
Simulated Pulse Counter enabled by Digital Input 1
•
Simulated Pulse Counter enabled by Digital Input 2
•
Frequency Counter attached to Digital Input 1
•
Frequency Counter attached to Digital Input 2
•
Up/Down Counter attached to Digital Inputs 1 & 2
•
Database location (data obtained from special script)
•
External DC power supply input – on change of state basis only.
•
SDI-12.
Each sensor can be set up to scale the raw data source into engineering units through the application of a
multiplier and offset (slope and constant). The scaled value can be logged to non-volatile memory up to
once per minute or immediately in event mode for pulse inputs. As all logged data is stored in integer
format, a logging multiplier can be applied to the scaled value to maintain resolution.
It is also possible to configure a sensor to also log minimum, maximum or a calculated flow rate (pulse
source only) values. Refer to the following descriptions in Section 2.5.3 and also Section 5.3.3 for further
detail on configuring these extended logging features as part of the Sensor Cfg menus.
2.5.3 Logged Data Array Identification
Each sensor’s logged data is identified by an array ID number. For the primary logged data, the ID is the
sensor number itself. For the optional supplementary data (min/max/deviation/flow or total), the array ID has
an offset added to the sensor number that it is derived from. These ID offsets are as follows:
Minimum:
+10
Maximum:
+20
Standard Deviation:
+30 (Not currently supported)
Flow Rate or Total:
+40
For example, Sensor 4 has been configured to log the average value, plus the maximum. Two data arrays
will be logged for this sensor at each log interval with IDs of 4 and 24 respectively. In HydroTel™ 2000
these will then relate to point identifiers of 4/0 and 24/0.
2.5.4 Alarm Processing
Each virtual sensor can be checked for two separate alarm conditions. Each alarm has separate trigger and
reset levels, as well as an activation delay or accumulation period depending upon the data type. The alarms
can also be used to control the digital output or to generate a call-back to a base station when the logger is
operating in telemetered mode. See Sections 4.2.5 for further details on digital outputs or Section 6.3.4 for
details on using Telemetry mode.