Af-60 lp™ micro drive programming guide, 1-8* stop adjustments, 1-9* motor temperature – GE Industrial Solutions AF-60 LP Micro Drive User Manual
Page 21
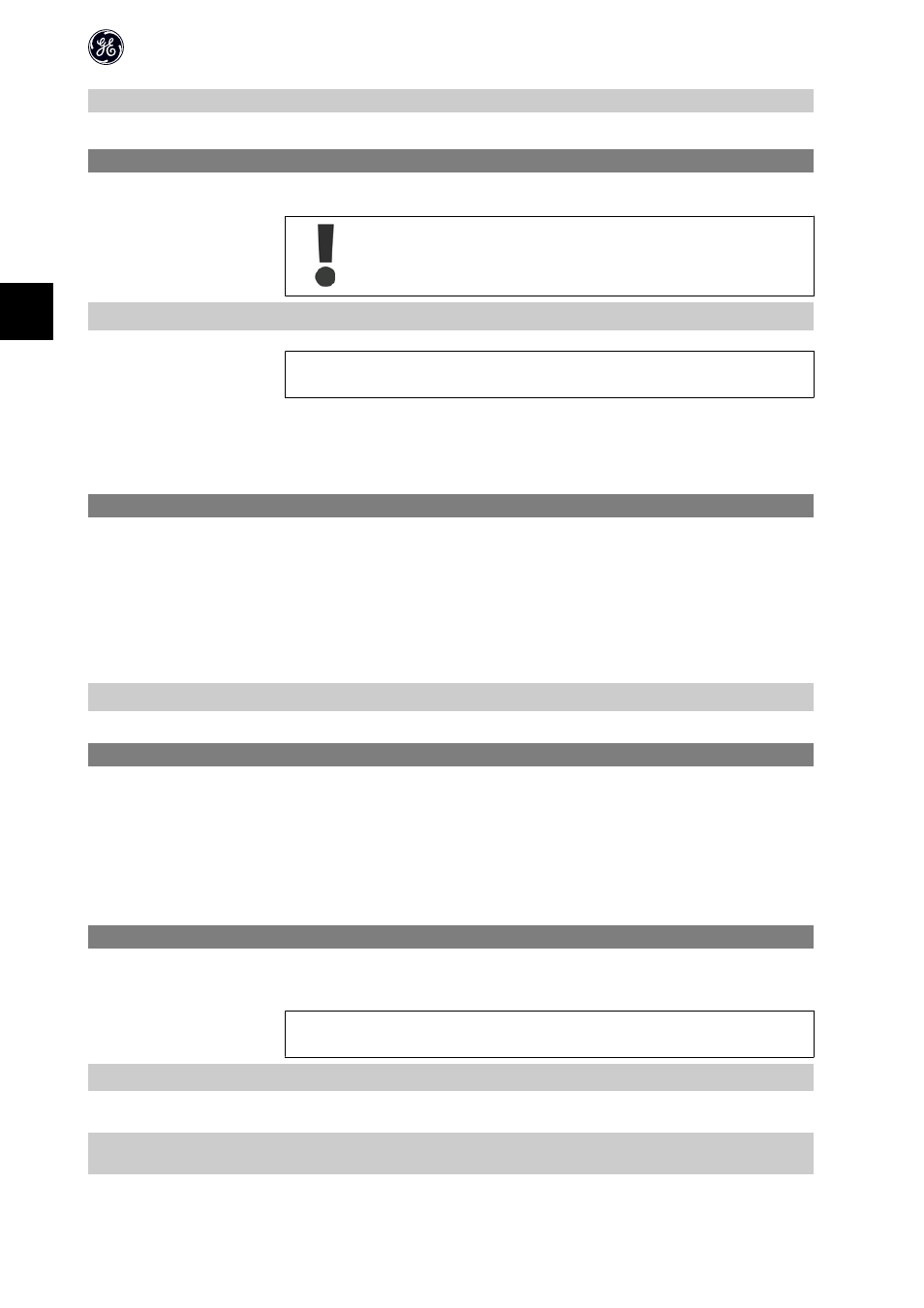
[1]
DC Brake/Delay Time
Motor is energized with DC braking current (par. 2-01) during start delay time.
[2]
*
Coast/Delay Time
Drive is coasted during start delay time ( Driveoff).
1-73 Start Mode
Option:
Function:
The Start Mode parameter is used to catch a spinning motor after eg. mains drop-out.
This function is not suitable for hoisting applications.
[0]
*
Disabled
Catch a spinning load disabled.
[1]
Enabled
Frequency converter enabled to catch spinning motor.
NB!
When catch a spinning load is enabled par. 1-71, Start Delay, and par. 1-72, Start Function, have no function.
4.2.6. 1-8* Stop Adjustments
To meet the need for various stop functions in different application these parameters offer some special stop features for the motor.
1-80 Function at Stop
Option:
Function:
The selected function at stop is active in following situations:
•
Stop command is given and output speed is ramped down to Min. Speed for Activating Functions at Stop.
•
Start command is removed (standby), and output speed is ramped down to Min. Speed for Activating Functions
at Stop.
•
DC-brake command is given, and DC-brake time has passed
•
While running and calculated output speed is below Min. Speed for Activating Functions at Stop.
[0]
*
Coast
The drive is coasted.
[1]
DC hold
The motor is energized with a DC current. See par. 2-00 DC Hold Current for more information.
1-82 Min. Speed For Function at Stop [Hz]
Range:
Function:
0.0 Hz
*
[0.0 - 20.0 Hz]
Set the speed at which to activate par. 1-80 Function at Stop.
4.2.7. 1-9* Motor Temperature
With an estimated motor temperature monitor the frequency converter is able to estimate motor temperature without having a thermistor mounted. It is thus
possible to receive a warning or an alarm, if motor temperature exceeds upper operational limit.
1-90 Motor Thermal Protection
Option:
Function:
Using Electronic Overload the motor temperature is calculated based on frequency, speed and time. GE recommends
using The Electronic Overload function, if a thermistor is not present.
NB!
Electronic Overload calculation is based on motor data from group 1-2*.
[0]
*
No Protection
Disables temperature monitoring.
[1]
Thermistor Warning
A thermistor connected to either digital or analog input gives a warning if upper limit of motor temperature range is
exceeded, (see par. 1-93, Thermistor Resource).
[2]
Thermistor Trip
A thermistor connected to either digital or analog input gives an alarm and makes the frequency converter trip if upper
limit of motor temperature range is exceeded, (see par. 1-93, Thermistor Resource.
AF-60 LP™ Micro Drive Programming Guide
20
4