Balancing specifications – Spicer Double Cardan Constant Velocity Joint Assemblies User Manual
Page 33
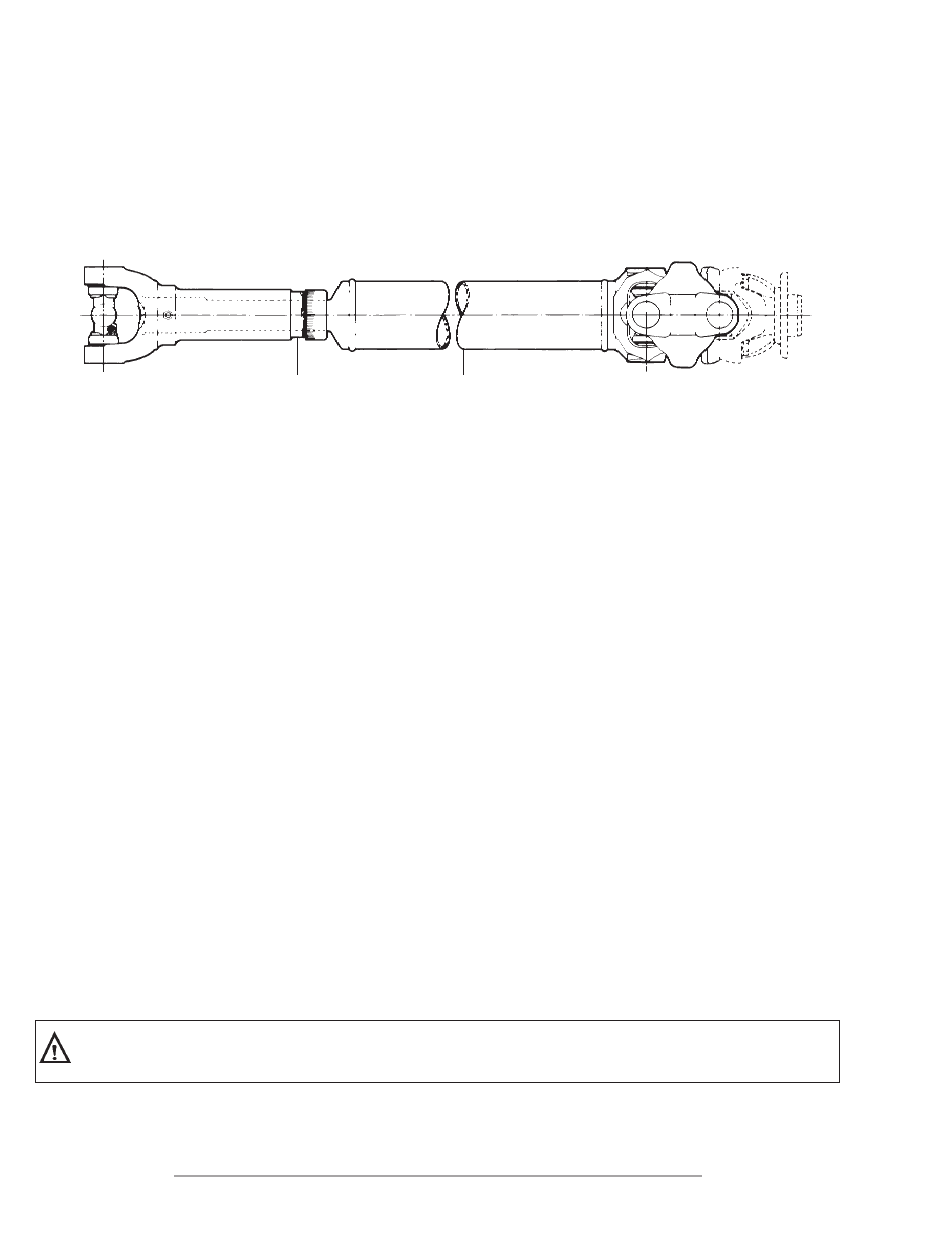
34
BALANCING SPECIFICATIONS
A driveshaft will not run smooth and vibration-free unless it is straight and in balance. When rebuilding or fabricat-
ing any Spicer driveshaft in this catalog, the runout and balancing specifications illustrated must be considered the
minimum requirements for satisfactory performance. A driveshaft which does not meet these minimum requirements
may wear out and/or fail prematurely.
Balancing Equipment and Operation
Driveshafts should be assembled, straightened, and dynamically balanced by properly trained operators only upon
commercially manufactured equipment specifically designed for this purpose. The following procedures and specifi-
cations are the minimum acceptable. Be sure to follow all of the instructions provided by the manufactureer of the
equipment you are using.
1. After assembly and before welding, pre-straighten driveshafts to .005” T.I.R. next to each weld location to help
prevent excessive bending of tubes when straightening after welding.
2. After welding, straighten shaft to the T.I.R. readings shown above.
3. Dynamically balance the entire shaft at the speed representative of the speed shaft will encounter in its normal
application, unless the driveshaft fabrication equipment manufacturer recommends otherwise.
4. Balance driveshaft to within one ounce-inch for each ten (10) pounds of weight, divided proportionally at each
end of the shaft. The weight of the shaft should be based on the total assembly, less flange yokes and end yokes.
Additional information on driveshaft service is available in our driveshaft service manual (publication no. 3264-2).
CAUTION: A driveshaft rotating at speeds of 500 RPM or greater must be dynamically balanced. Failure to
properly dynamically balance a driveshaft could cause serious personal injury or death.
Straightening Requirements After Welding
(Mid-Point of Tube)
.005” T.I.R.
.010” T.I.R.