D. heater will not turn off, Fk4b fan coil description and troubleshooting, I. integrated controls and motor (icm2) – Bryant FA4A User Manual
Page 7: Ii. pcb layout and description, Iii, sequence of operation, A. continuous fan mode
Attention! The text in this document has been recognized automatically. To view the original document, you can use the "Original mode".
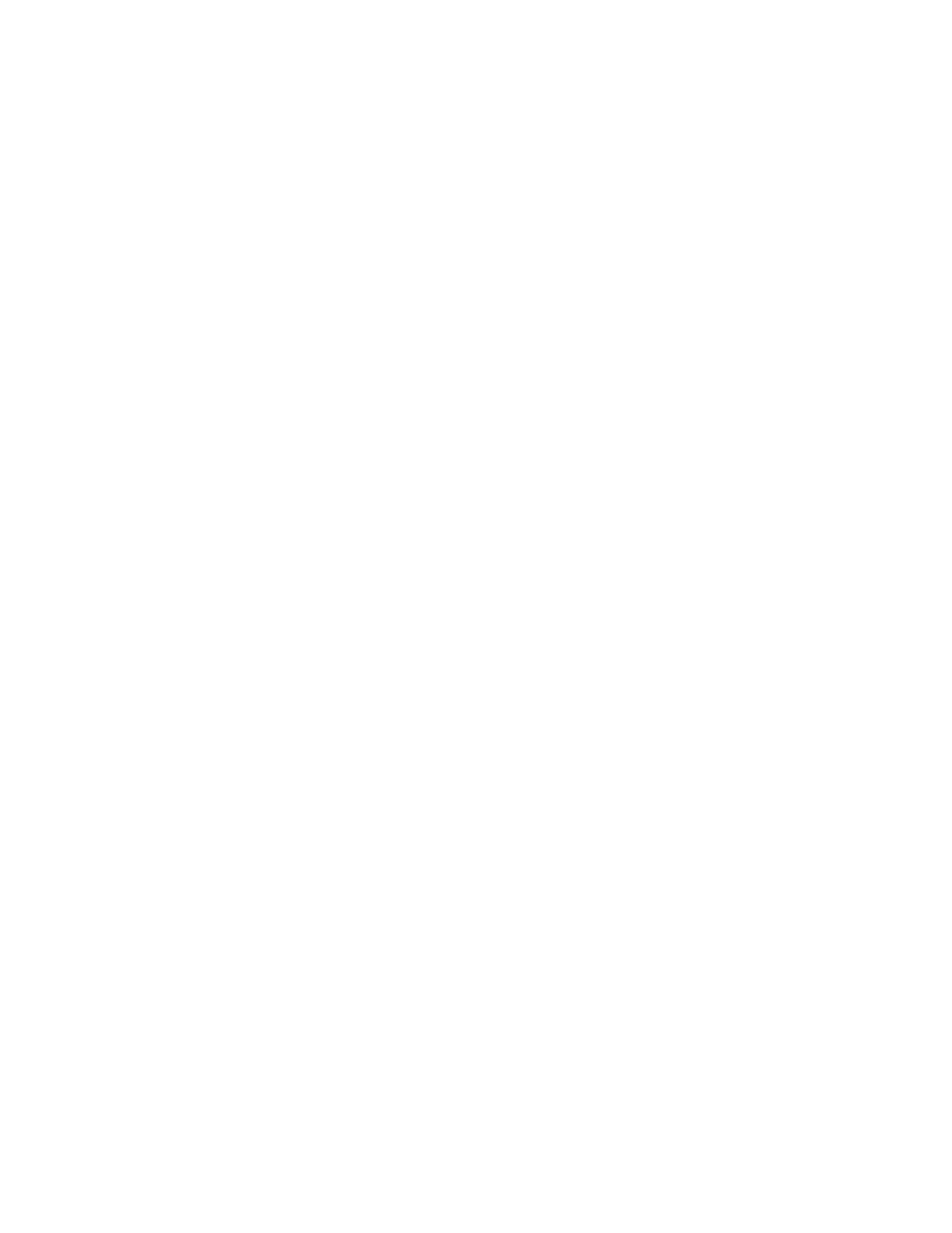
A U G / 1 4 / 2 0 0 8 / T H U 0 3 : 4 6
UTC TECH PUB
F A X N o , 3 1 7 2 4 0 6 6 6 2
2.
Check for faulty transformer. Check output voltage of
transformer secondary side R (red) and C (brown). Make
sure output is between IS and 30 vac. If output voltage is
low pud input voltage teçtç normaJ, replace transformer.
3. Check for miswired heater plug harness,
4. Check limit switch or sequencer failure. These switches
should have failed in open position. If output voltage is zero
V, replace Switch,
D. Heater Will Not Turn Off
1. Check low-voltage wiring for miswire.
2. Check for shorted elements to ground.
3. Replace sequencer contacts. They may be stuck closed.
E.
Nuisance
Trips
1. Check for low airflow due to dirty filters» blocked registers,
Of Undersized duct.
2.
Check blower motor and wheel for proper operation.
Excessive current draw of motor will cause internal over
load to trip.
3. The fan Speed may be low.
FK4B FAN COIL DESCRIPTION
AND TROUBLESHOOTING
The FK4B is similar to the discontinued FK4A only in that they
both have integrated controls and motor (ICM) and their own
Special
circuit board. The
greatest
difference between the 2 models
is the way each goes about delivering air.
Setting up desired airflow on the FK4B is obtained by the
selections made on Easy Select circuit board. The motor delivers
requested airflow as defined by signals received from Easy Select
Board and its internal programming. The major difference is that
the FK4B motor reacts to changes in system static pressures to
mainiain constant airflow.
Unlike conventional fan coils where static pressure affects airflow,
the FK4B is a constant airflow unit. The blower delivers requested
airflow up to about 0.7 in. of static pressure. The ÏCM2 is
pre-programmed and contains airflows for al) modes of operation.
Blower characteristics (airflow, torque, and spccd-vs-static pres
sure) are known from laboratory testing. If any 3 characteristics are
known, the fourth iS defined.
Requested airflow is known because of Easy Select board con
figuration and thermostat signals. Torque is known because it is
directly related to armature current which is measured by motor
control. Speed is measured from its generated back EMF. This
information is entered into an expression which calculates tOrque
from speed and airflow numbers. If calculation does not match
stored blower characteristics, torque is adjusted every 0.6 sec until
agreement is reached. The unit does not directly measure static
pressure, but does react to a^ change in static to maintain constant ■
airflow.
I.
INTEGRATED CONTROLS AND MOTOR (ICM2)
The ICM2 is similar to the ICMI used in FK4A series units, but
cannot be used as ,a replacement without some modification to
FK4A unit. Consult SMB 93-0052 for motor conversion kit. The
electronics of motor are built into rear of motor, deriving the name
ICM, (Sec Fig, 5.)
An ICM is first fed high voltage AC power through the 5-pin
connector. The AC power is then rectiEcd to DC by a diode
module. After rectification, DC signal is electronically communi
cated and fed in sequential order to 3 stator windings. The
frequency of.communication pulses dctemiines motor speed. The
rotor is permanently magnetized.
An ICM is powered with high voltage at all times. The motor will
not run with high voltage alone. Low voltage must be applied to
control plug to run motor-
II. PCB LAYOUT AND DESCRIPTION
NOTE:
Layout of actual PCB is depicted in Fig, 6 and 7,
The control is a single PCB which interfaces a variable-speed
ICM2 with Other System components.
Power for system is supplied from a 230-vac^ 60-Hz line. Class 2
voltage (24 vac nom.), used for thermostat connections, is derived
from a transformer located in close proximity to control. The
primary and Secondary of transformer are connected to control
board. The 24-vac secondary circuit includes a socket, soldered
into circuit at SEC2, to receive a 5-amp automotive-type fuse.
Connection to heater panel is made through 12-circuit connector
PI. Connections to thermostat are made at screw terminals. Line
voltage for ICM2 is made through 7-circuit connector P2. Eighteen
quick-connect terminals comprise field select taps for motor.
Fuse Data; 5 amp automotive-type ATC/ATO (tan)
32v
200 percent current Opening time of 5 sec maximum
A. Electrical ConnectiDna
Eighteen 0,lS7-in quick-connect terminals arc used to provide
programming selections for operating modes of ICM2. The 5
selection modes № listed belOw, For additional information, refer
to Easy Select Configuration Taps section.
AUX Heat Range ^(Violet Wire)
AC/HP Size-(Blue Wire)
Type—(Orange Wire)
AC/HP CFM Adjust-(Black Wire)
AC/HP Time Delay-(Grey Wire)
III, SEQUENCE OF OPERATION
A. Continuous Fan Mode
The thermostat closes circuit R to G, The G signal is sent directly
to ICM2.
B. Cooling Mode—Single Speed or 2-Speed High
Thermostat closes circuits R to Y/Y2 and R to O (heat pump only)
for single speed. A circuit from R to Y1 is also required for
2-spced high. The Y/Y2 signal is sent directly to 1CM2.
C. Cooling Mode—Two-Speed Low
Thermostat closes circuits R to Y1 and R to O (heat pump only).
The Yl signal is sent directly to ICM2.
D. Electric Heat Heating Mode
Thermostat doses circuit R to W2, W3, or E,
The terminal block positions W2, W3, and E arc tied together by
jumpers JWl and JW2, These jumpers are provided for field
staging of electric heater banks through use of thermostats. When
staging is a requirement, installer cuts jumpers and wires in
thermostats as is the common practice with other fan coils. To
ensure motor operation if any 1 of the inputs is energized^ the 3
electric heater inputs arc also interlocked through diodes Dl, D2^
and D3 to motor W input.
E.
Heat Pump Heating Mode—Single Speed or 2-Speed
High ■
Thcmiostai doses circuit R to Y/Y2 for single speed. A dreuit
from R to Yl is also required for 2-speed high. The Y/Y2 signal
is sent directly to ICM2,
F. Heat Pump Heating Mode—Two-Speed Low
Thermostat doses R to Yl. The Yl signal is sent directly to ICM2.
G. Heat Pump Heating With Auxiliary Electric Heat
Thermostat doses circuits R to Y/Y2 and/or R to Yl with R to W2,
W3, Or E (and R to 0 in the case of defrost).
See previously described modes for circuit paths.
In the event that electric heating is called for by thermostat while
heat pump is also operating in either heating or defrost mode,
electric heating signal will appear at motor connector pin 1 as
described previously. If necessary» the motor will modify its
airflow output to provide an airflow which is deEned as safe for
operation of electric heater.
-7-