Unit controls and safety devices – Carrier 38CQ User Manual
Page 15
Attention! The text in this document has been recognized automatically. To view the original document, you can use the "Original mode".
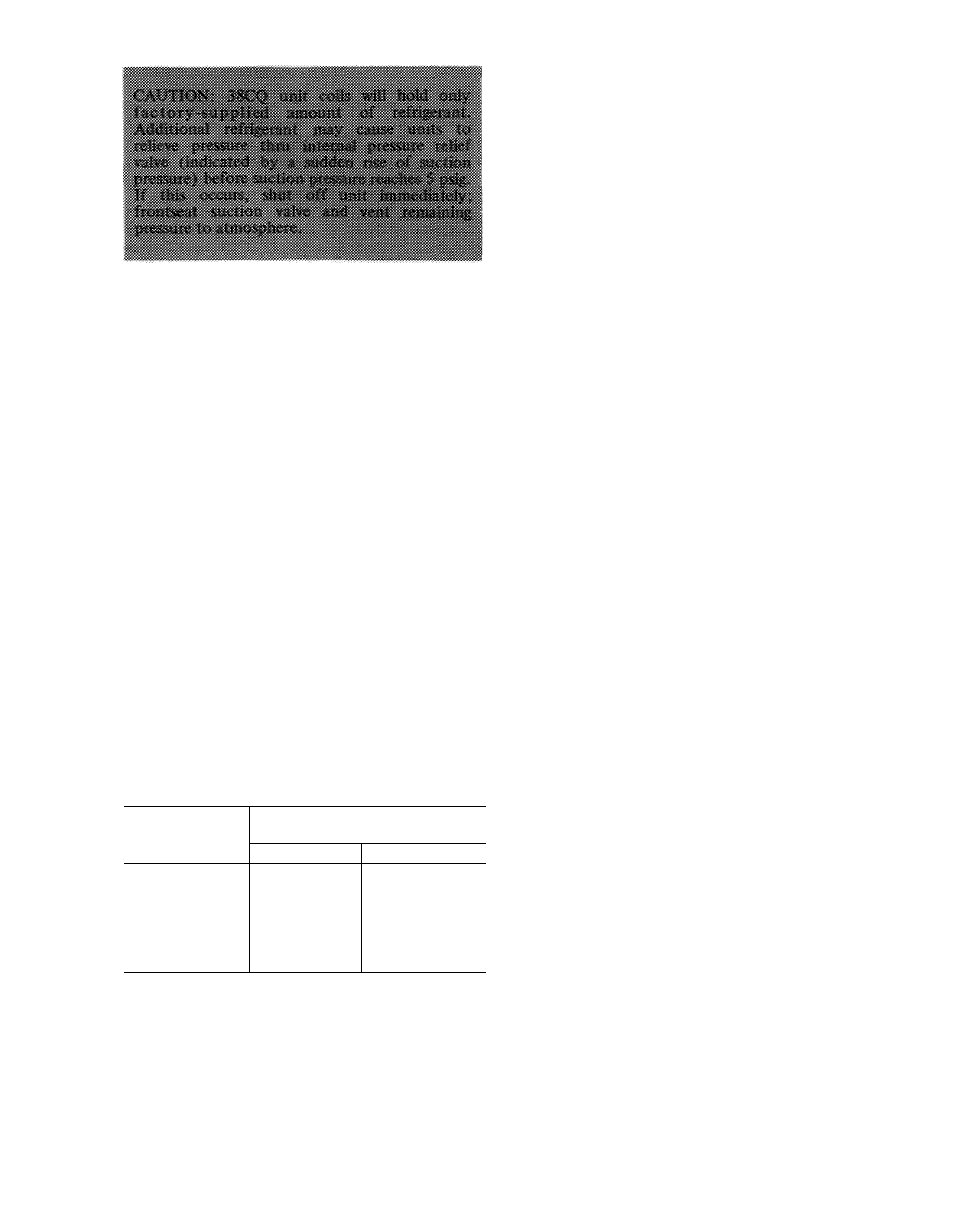
Unit Controls and Safety Devices
HIGH-PRESSURE RELIEF VALVE is located in
compressor. Relief valve opens at a pressure differ
ential of approximately 600 psi between suction
(low side) and discharge (high side) to allow
pressure equalization.
INTERNAL CURRENT AND TEMPERATURE
SENSITIVE OVERLOAD resets automatically
when internal compressor motor temperature
drops to a safe level (overloads may require up to
45 minutes to reset). When an internal overload is
suspected of being open, check by using an
ohmmeter or continuity tester. If necessary, refer
to Carrier Standard Service Techniques Manual,
Chapter 2, for complete instructions.
LIQUID LINE LOW-PRESSURE SWITCH (LLPS)
is connected in liquid line to work with compressor
internal thermostat in providing loss-of-charge pro
tection during the heating cycle. Control is
mounted on liquid line.
With a high-side leak, pressure gradually de
creases until low-pressure control stops the com
pressor. (Low-pressure control settings are shown
in Table 8.)
Table 8 — Pressure Switch Settings
UNIT
38CQ
LIQUID LINE
LOW-PRESSURE SWITCH
Cut-in (psig)
Cutout (psig)
015
020
027
033
20 + 5
5+3
039
044
048
With a low-side leak there is always some
pressure in the liquid line. However, compressor
motor temperature increases because of in
sufficient suction gas cooling. This causes internal
thermostat to actuate and stop compressor. When
compressor stops, system pressure equalizes and
contacts on pressure control open. The compressor
cannot restart until leak is repaired and system
recharged.
CRANKCASE HEATER is connected across line
side of contactor and operates continuously.
The purpose of the heater is to keep the
crankcase warm during the off cycle and thus
prevent dilution of the oil with refrigerant. This
assures good lubrication and prevents loss of oil
from crankcase during start-up.
If the electrical disconnect switch to the out
side unit has been off for an extended period of
time, the crankcase heater should be energized for
24 hours before starting the compressor
DEFROST CONTROL, consisting of a defrost
timer, defrost thermostat and defrost relay, inter
rupts normal system heating operation every 90
minutes to defrost outdoor coil, if the coil satu
rated
suction
temperature
indicates
freezing
temperatures. Defrost control simultaneously stops
outdoor fan, energizes reversing valve solenoid to
return system to cooling cycle (outdoor unit as
condenser, indoor unit as evaporator), and acti
vates accessory electric heater.
For the heat pump to defrost, 2 conditions are
necessary:
1. Defrost timer contacts must be closed.
2.
Refrigerant temperature from outdoor unit
must be cold enough to cause defrost ther
mostat contacts to close. Contacts close at 31
(±4) F.
Every 90 minutes of elapsed running time, the
defrost timer contacts close for 10 seconds. If the
defrost thermostat contacts are closed, the unit
defrosts. The defrost timer limits defrosting period
to 10 minutes. Normally the frost is removed and
the defrost thermostat contacts will open to
terminate defrosting before 10 minutes have
elapsed. Defrost thermostat contacts open at 80
(±6) F liquid refrigerant temperature. When de
frosting is terminated, the outdoor fan motor is
energized and reversing valve solenoid is de
energized returning unit to heating cycle.
HEAT PUMP CIRCUITS shown in Fig. 32 are
refrigerant flow diagrams for heating and cooling
cycles.
AccuRater^''^ (Bypass Type) Servicing
— See Fig.
33 for bypass type AccuRater components. The
piston has a refrigerant metering hole thru it. The
retainer forms a stop for the piston in the
refrigerant bypass mode, and a sealing surface for
liquid line flare connection. To check, clean or
replace piston:
1. Shut off power to unit.
2. Pump unit down using Pumpdown Procedure
described previously.
3.
Remove liquid line flare connection from
AccuRater.
4. Pull retainer out of body being careful not to
scratch flare sealing surface. If retainer does not
pull out easily, carefully use vise grips or pliers
to remove retainer.
5. Slide piston out by inserting a small soft wire,
with small kinks, thru metering hole. Ensure
metering hole, sealing surface around piston
cones and fluted portion of piston are not
damaged.
15