Chapter 5. calibration instructions, Basic adjustments, Tuning methodology – Winco DPG-2145-001 User Manual
Page 35
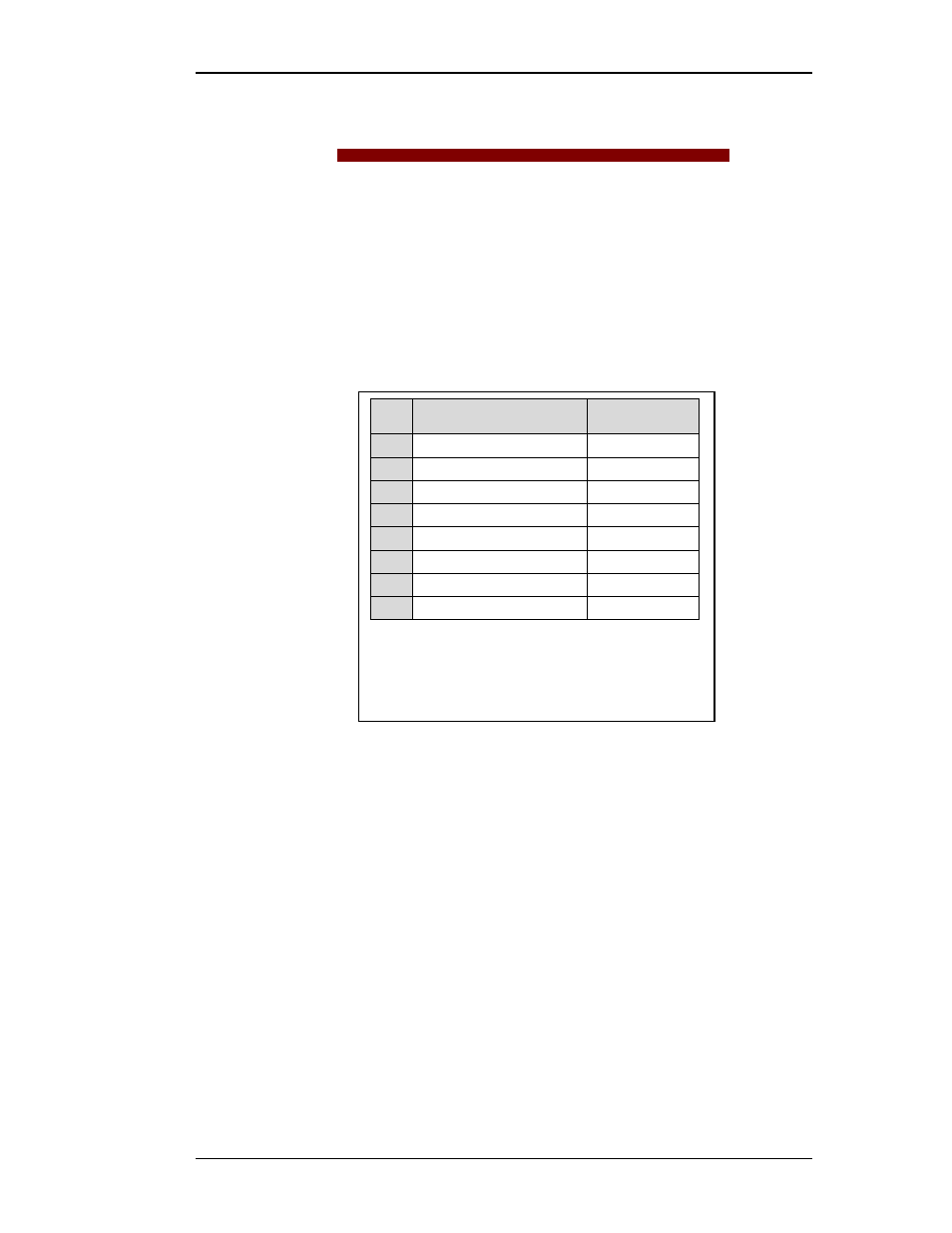
Manual 36526F
DPG-21XX-00X Digital Controllers
Woodward
27
No.
Parameter Name
Default Value
2
SET SPEED A
1000
5
PROPORTIONAL
25
6
INTEGRAL
50
7
DERIVATIVE
25
8
OVG @ SET SPEED A
20
11
GAIN FACTOR (note 1)
20
12
SPEED FILTER (note 2)
16
28
STARTUP SPEED
1000
NOTE 1: Modify Gain Factor only if you run out of
adjustment in a PID or OVG term.
NOTE 2: For the Speed Filter, typically the value 24
works well on small 3- or 4-cylinder engines. A value
of 16 is recommended for 6- or 8-cylinder engines.
Chapter 5.
Calibration Instructions
Basic Adjustments
The controller is programmed at the factory with default parameter settings. These
settings allow the controller to operate but usually require some further adjustments to
obtain the best system performance. In order to bring the engine up to a single speed
for the first time, the installer will probably need to adjust the parameters shown in the
table below.
The parameters listed are the primary ones to modify to get the controller tuned and the
engine running smoothly. It is recommended that you work with them first and leave all
the other parameters at their default values until you are satisfied with the basic engine
tuning.
Tuning Methodology
Once the engine is running, the following procedure may be used to discover more
optimum values for PID and the overall gain parameters (OVG). The goal would be to
find PID values that allow the controller to govern the engine well at a variety of
different speeds and loads while only requiring gain adjustment at those different
speeds.
Follow these steps:
1.
Set the integral and derivative terms to 0.
2.
Set the overall gain low (<20).
3.
Increase the proportional term until you get continuous oscillations greater
than 2 Hz.
4.
Reduce the proportional term by 25% to 50%.
5.
Now experiment with small value changes in the derivative to dampen out
―ringing‖ in response to load transients.
6.
Add some integral to eliminate any steady-
state error in the engine’s speed
and help decrease error recovery time.
7.
The overall gain can be increased to improve response time while keeping
the ratios of the PID terms relative to each other constant.