27 duty cycle limit (optional), 28 startup speed (required), 29 startup duty cycle (optional) – Winco DPG-2145-001 User Manual
Page 24
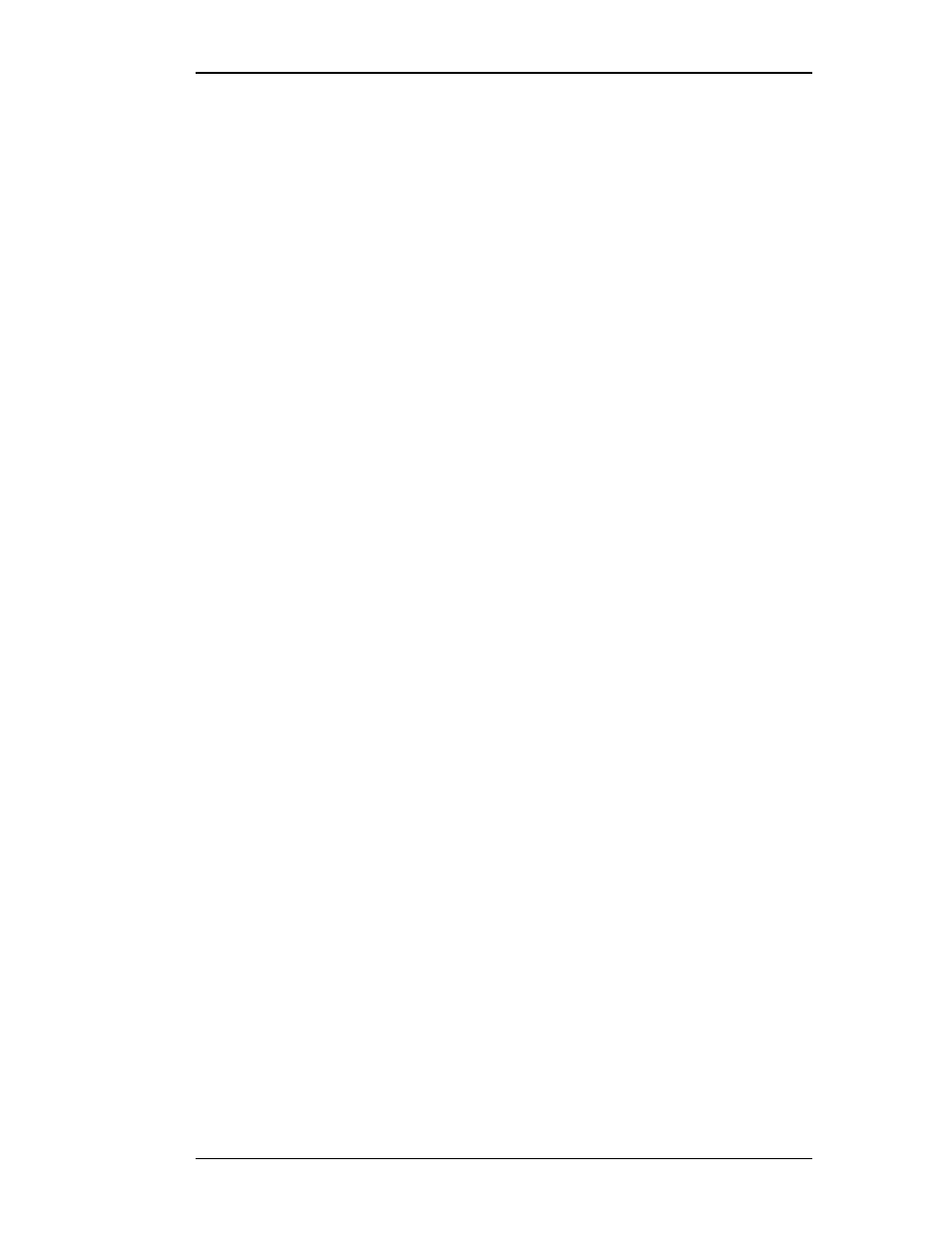
Manual 36526F
DPG-21XX-00X Digital Controllers
Woodward
16
3.27 Duty Cycle Limit (optional)
The Duty Cycle Limit parameter sets the absolute maximum amount of drive signal that
can be output to the actuator and thus serves as a mechanism for fuel limiting. Fuel
limiting is achieved by setting the maximum duty cycle or on-time allowed during one
cycle of the PWM (pulse-width-modulation) signal controlling the actuator drive circuit.
The value assigned to the duty cycle limit parameter is a percentage, and is limited to
values in the range 10% to 95%. The default value is 95%.
3.28 Startup Speed (required)
The Startup Speed parameter should be set to an engine speed at least 10% higher
than the fastest engine cranking speed but lower than the engine’s idle speed. This
allows the controller to determine whether the engine is cranking or running whenever
an
engine speed signal is present. See the ―Startup Sequence‖ example in Chapter 5.
If the Startup Speed value is set too low (less than crank speed) the controller’s target
speed will be ramped to the active set speed (Idle, Set Speed A, or Set Speed B)
before the engine has started. Therefore, when the engine does start, it may overspeed
or output excessive smoke because the startup ramp, having already completed, no
longer controls the rate of engine speed increase.
If the Startup Speed value is set too high (above the active set speed) then the Startup
Speed becomes the target speed that the controller must reach before the it considers
the startup sequence complete. Typically, the startup sequence ends when the engine
speed reaches the active set speed. The active set speed is the Idle Speed if the Idle
Hold Time parameter is a nonzero value or the ―selected set speed‖ (either Set Speed
A or Set Speed B).
To determine the proper value for this parameter the crank speed must be known.
There are two ways to determine the engine crank speed.
1) Use a meter to measure the frequency across the MPU+ and MPU-
terminals of the controller during cranking or . . .
2) Use a PC running the Universal PST application and read the value
of the Measured Speed in the View Status panel when the engine
is cranking. Note: From the Universal PST startup screen press the
View Status button, then press the Start Monitoring button to begin
reading values.
3.29 Startup Duty Cycle (optional)
The Startup Duty Cycle parameter is used to pre-load the PID output with a PWM duty
cycle value close to that needed for the actuator to allow enough fuel to idle the engine.
If the value is too low, then the engine crank time may be longer than desired because
the controller’s actuator output starts from a value much smaller than needed to begin
opening the fuel valve.
If the value is too high, then the engine may overspeed because the actuator opens
more than needed to start the engine.
There are two ways to determine a good value to use for this parameter.
1) Use a meter to measure the duty cycle across the ACT terminals of the
controller while the engine is running. Note: To determine if your meter is
reading the correct value: