8 ovg @ set speed a (required), 9 ovg @ set speed b (optional), 10 ovg @ idle speed (optional) – Winco DPG-2145-001 User Manual
Page 19: 11 gain factor (required), 12 speed filter (required)
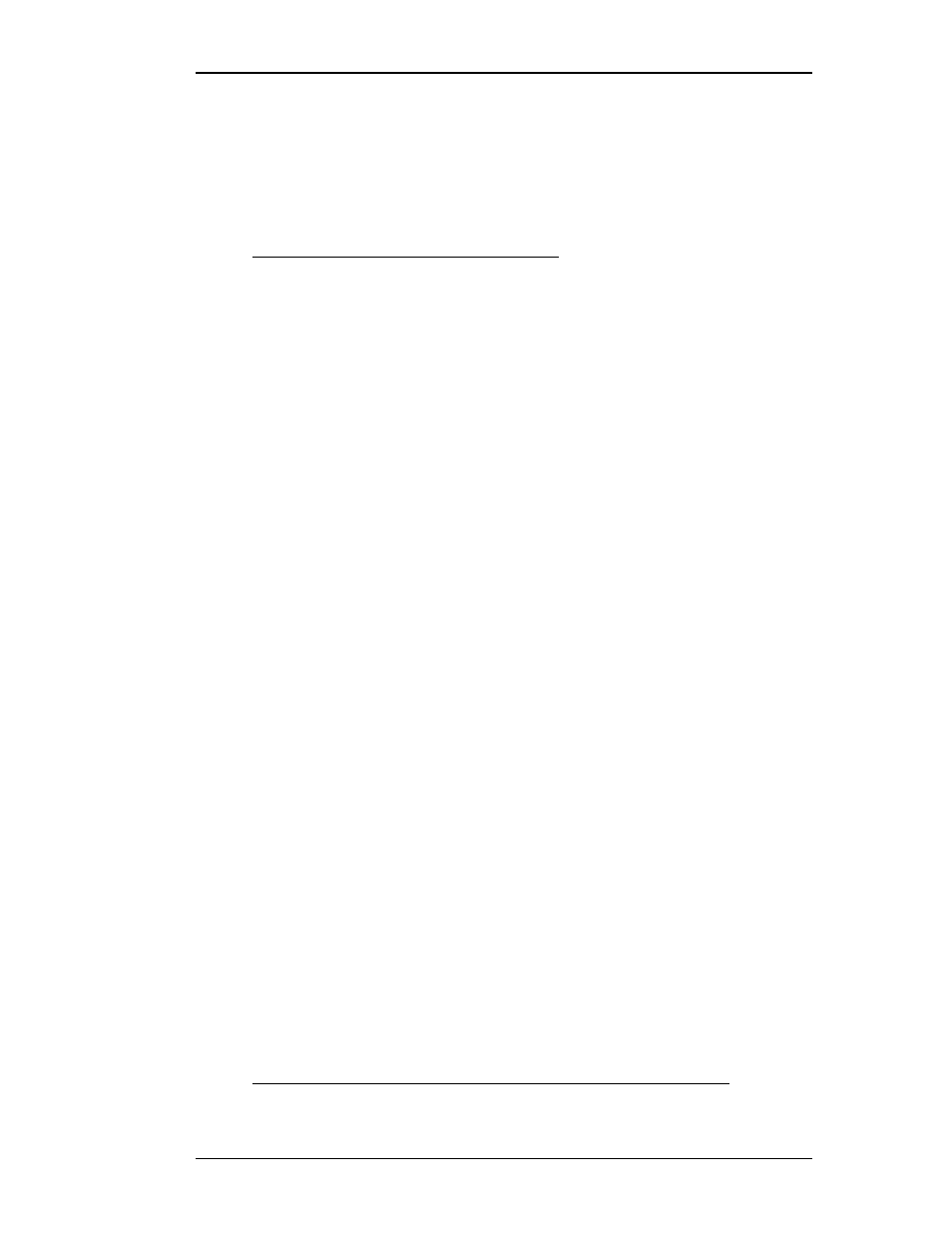
Manual 36526F
DPG-21XX-00X Digital Controllers
Woodward
11
3.8 OVG @ Set Speed A (required)
This overall gain acts as the multiplier on the three PID terms (proportional, integral,
derivative) when Set Speed A is selected as the active target speed. The controller’s
built-in gain potentiometer is adjustable from 1 to 99.
3.9 OVG @ Set Speed B (optional)
DPG-2145-00X and DPG-2155-00X Models
This overall gain acts as the multiplier on the three PID terms (proportional, integral,
derivative) when Set Speed B is selected as the active target speed. This overall gain
term is adjustable from 01 to 99.
3.10 OVG @ Idle Speed (optional)
This overall gain acts as the multiplier on the three PID terms (proportional, integral,
derivative) when the Idle Speed is the active target speed. The idle speed set point is
active only during startup when the idle hold timer is running. This overall gain term is
adjustable from 01 to 99.
3.11 Gain Factor (required)
The gain factor parameter is used to obtain more range of adjustment from the PID
terms. In other words, if any of the PID terms or the overall gain terms reach their
adjustment limits then this value can be modified to provide for more range of
adjustment in the PID and OVG terms.
For example, if the PID terms are set to 90, 80, and 50 respectively and the Gain
Factor is set to 20, then doubling the Gain Factor by setting it to 40 allows the PID
terms to be halved to 45, 40, and 25 respectively. These new settings are equivalent to
the previous settings with respect to the controller’s tuning response and now allow the
PID terms to be adjusted higher if needed.
3.12 Speed Filter (required)
This parameter indicates the number of flywheel teeth to use when computing an
average engine speed and is used to dampen out speed measurement variations that
can make PID tuning difficult. But, keep in mind the following.
Too much filtering will slow down the controller’s response
to speed changes.
Too little filtering can make the controller overly sensitive
and tuning difficult.
There is measurable acceleration and deceleration that occurs between cylinder firings.
As a general rule, less filtering is required the more engine cylinders there are. This is
because the number of acceleration-deceleration cycles increases and these
oscillations will have lower amplitude. With more cylinders, there is less time for the
speed to slow down before the next cylinder firing.
Rotational mass also affects the amount of speed signal filtering needed. The more
rotational mass, the less filtering is needed. The less rotational mass, the more filtering
is needed.
For installations using a magnetic pickup to sense engine speed
Typically, the value 24 works well on small 3- or 4-cylinder engines. A value of 16 is
recommended for 6- or 8-cylinder engines. The following formula can also be used to