Caution, Warning – Reznor R6GN Unit Installation Manual User Manual
Page 18
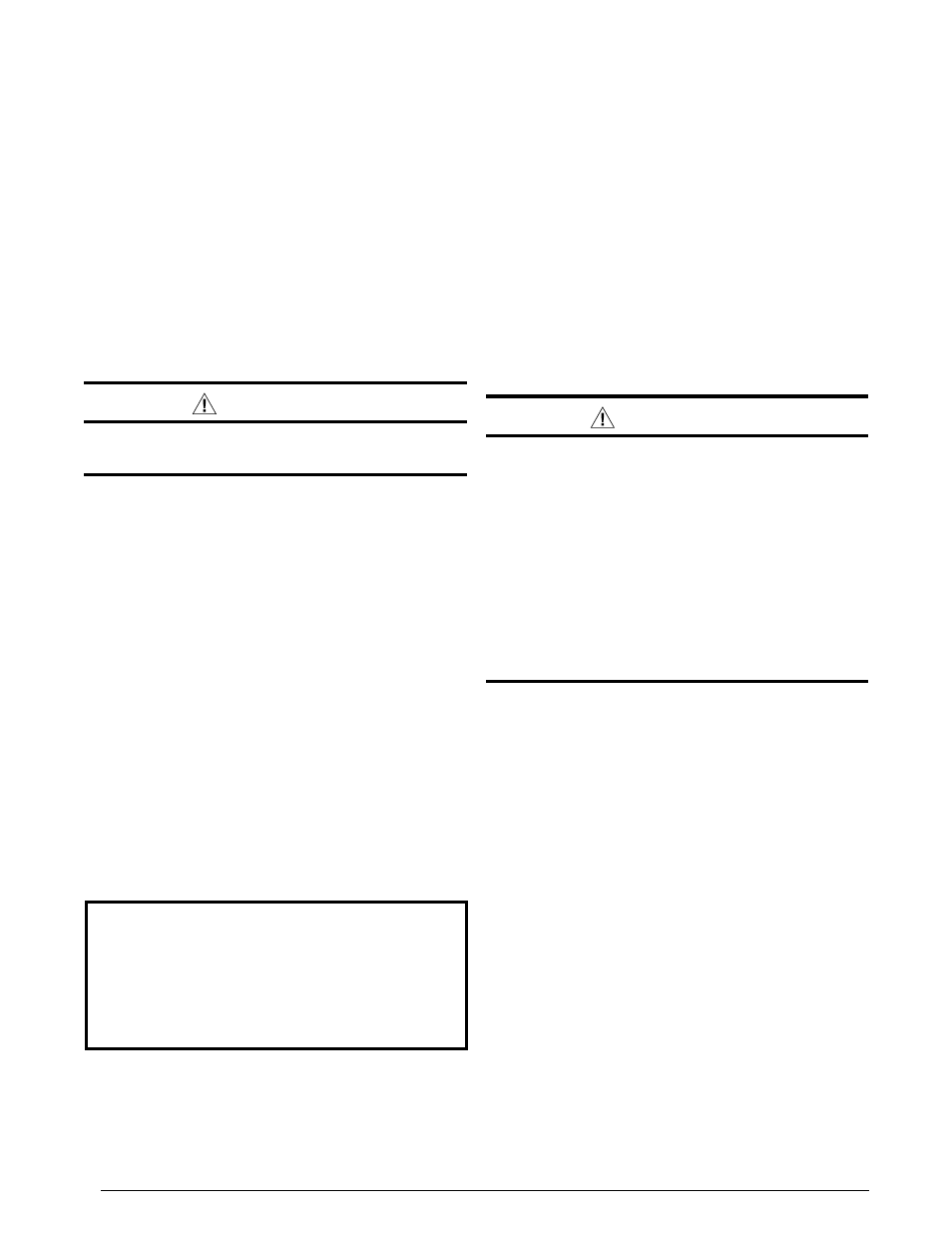
18
blowers should continue to run when the over-temperature
limit control switch opens.
3. Remove the close-off plate immediately after the over-
temperature limit control opens. If the unit operates
for more than four minutes with no return air, set the
thermostat below room temperature, shut off power to
the unit, and replace the over-temperature limit control.
NotE: On some low static/high airflow applications, the
Over-Temperature limit control may not function. To ensure
the limit is functioning properly, the outlet may also have to
be slightly restricted to achieve higher outlet temperatures
.
Verifying & Adjusting Firing Rate
The firing rate must be verified for each installation to
prevent over-firing of the unit.
cautIoN:
Do not re-drill the burner orifices. If the orifice
size must be changed, use only new orifices.
IMPoRtaNt NotE: The firing rate must not exceed the
rate shown on the unit data label. At altitudes above 2,000
ft., it must not exceed that on the data label less 4% for
each 1,000 ft.
Follow the steps below to determine the unit firing rate:
• For installations at 2,000 feet and less, the firing rate is
the same as shown on the unit rating label.
• For installations above 2,000 feet, compute the correct
firing rate as shown in the example on page 13.
1. Obtain the gas heating value from the gas supplier
(HHV).
2. Shut off all other gas fired appliances.
3. Start the unit in heating mode and allow it to run for at
least three minutes.
4. Measure the time (in seconds) required for the gas
meter to complete one revolution.
5. Convert the time per revolution to cubic feet of gas per
hour using Table 7 (page 33).
6. Multiply the gas flow rate in cubic feet per hour by the
heating value of the gas in Btu per cubic foot to obtain
the firing rate in Btu per hour. See example:
Manifold Pressure Adjustment
The manifold pressure must be set to the appropriate
value for your installation. To adjust the manifold pressure:
1. Obtain the required manifold pressure setting. Refer to
either Table 9 for natural gas or Table 10 for LP/propane
gas (page 34).
NotE: The values listed in the tables
are based on sea level values. At higher altitudes, the
heating value of gas is lower than the sea level heating
value.
2. Remove the regulator cap. Turn the high fire
adjusting screw clockwise to increase the pressure or
counterclockwise to reduce the pressure.
3. Replace the regulator cap after adjustments are
complete.
Refrigerant charging
WaRNING:
If repairs make it necessary for evacuation and
charging, it should only be done by qualified,
trained personnel thoroughly familiar with this
equipment. Some local codes require licensed
installation/service personnel to service this
type of equipment. Under no circumstances
should the owner attempt to install and/or
service this equipment.
Failure to comply with this warning could result
in property damage, personal injury, or death.
This Single Package Gas Heating / Electric Cooling unit
is fully charged at the factory and requires no charging
when installed accordingly. Units should be operating
with liquid sub-cooling readings between 13° F - 15° F.
If measurements indicate a lower or higher sub-cooling
reading, refrigerant levels must be adjusted to achieve
maximum system performance. The refrigerant charge
can be checked and adjusted through the service ports
located behind the service panel. Use only gauge lines
which have a “Schrader” depression device to actuate
the valve.
Refrigerant charging charts for 12.5 and 15 ton units
are included in these instructions. To identify proper unit
charge operation see Figure 13 (page 28) for 12.5 ton or
Figure 14 (page 29) for 15 ton.
NotE: Both refrigeration
stages must be operating when taking liquid temperature
and pressure measurements.
Refrigerant charging must be done by qualified personnel
familiar with safe and environmentally responsible
refrigerant handling procedures. See Unit Rating Plate
for proper amount of refrigerant.
Example:
• Time for 1 revolution of a gas meter with a 1 cubic
foot dial = 40 seconds.
• From Table 7, read 90 cubic feet gas per hour.
• Local heating value of the gas (obtained from gas
supplier) = 1,040 Btu per cubic foot.
• Input rate = 1,040 x 90 = 93,600 Btuh.
7. Adjustments to the firing rate can be made by adjusting
the gas manifold pressure. See the High Altitude Deration
section (pages 12 - 13) for additional information of
firing rate at elevations above 2000 ft.