Great Plains NTA3007 Operator Manual User Manual
Page 98
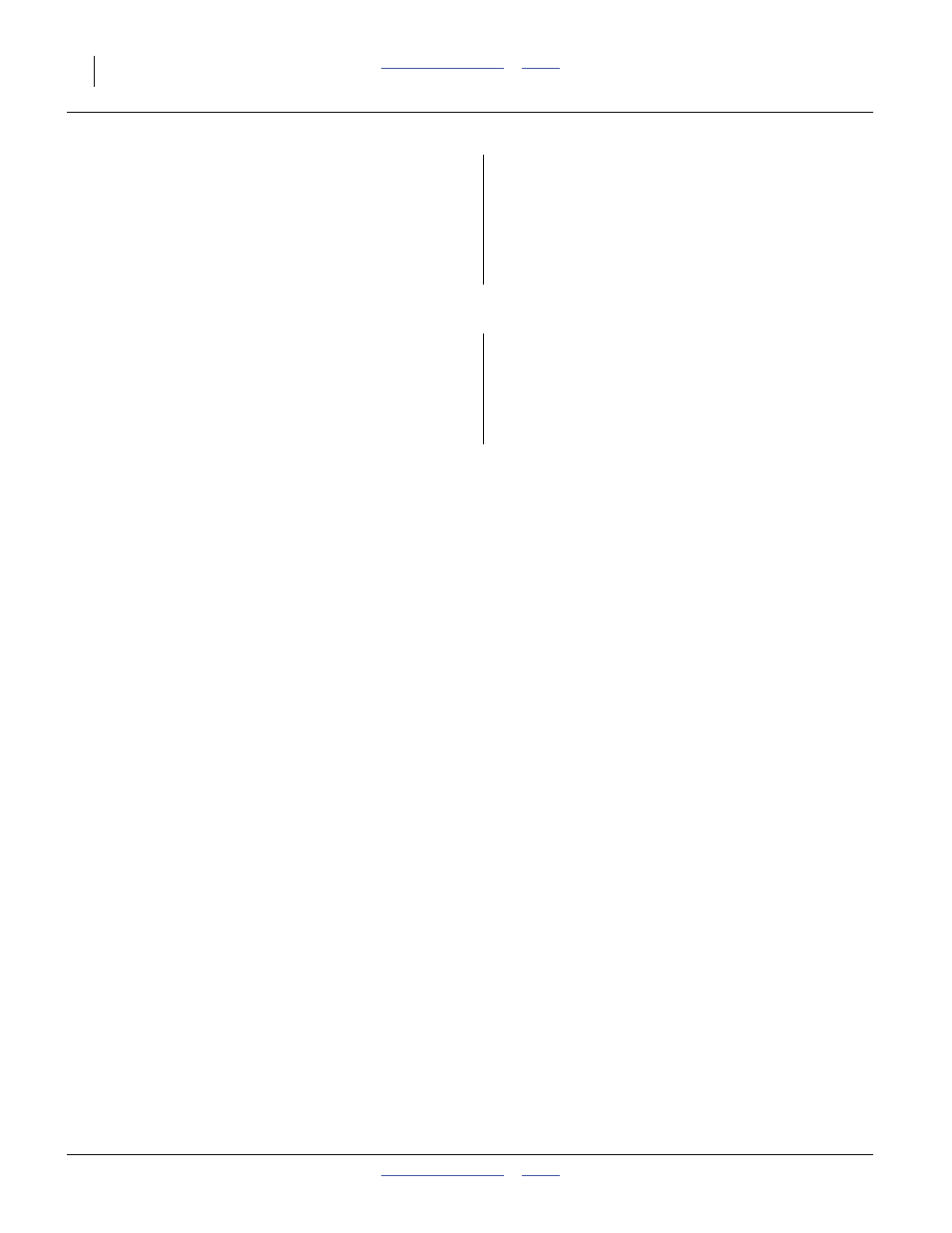
94
NTA907 or NTA3007
Great Plains Manufacturing, Inc.
166-371M
2012-07-02
28. Determine the amount of rate change for each
degree of control arm rotation from the target setting.
If the calibrated rate was
higher than target (as in our example),
examine lower gearbox setting values.
If the calibrated rate was
lower than target,
examine higher gearbox setting values.
29. Adjust the control arm by the number of degrees
needed to adjust for the calibration difference.
The rate of the arm adjusting crank is more than one
scale degree per turn, and the crank can only be
pinned at quarter turns. Pin it when the indicator is
closest to the corrected setting.
30. To validate the adjustment, run the calibration again,
starting at step 14 on page 92, using the new
Variable Rate Gearbox scale setting.
This validates the gearbox adjustment, and will
generate a new, more precise Calibration Constant.
31. With the present meter satisfactorily calibrated,
re-mount the final drive gear removed (if any) from
the meter on the other hopper.
32. Repeat the calibration procedure for the other
hopper, starting at step 1 on page 90.
33. Continue at “Calibration Close-Out” on page 96.
Metric
U.S. Customary
1 degree lower reduces rate by
201.3 - 195.4, or 5.9 kg
179.6 - 174.3, or 5.3 lbs
2 degrees lower reduces by
201.3 - 189.4, or 11.9 kg 179.6 - 169.0, or 10.6 lbs
3 degrees lower reduces by
201.3 - 183.5, or 17.8 kg 179.6 - 163.7, or 15.9 lbs
Metric
U.S. Customary
The calibration difference was:
17 kg
15 pounds.
Adjusting down 3 degrees is a nearly ideal correction.
So adjust the gearbox to a final scale setting of:
slightly above 59
slightly above 59