Brake drum and liner maintenance, Recommended work practices, Procedures for servicing brakes – Great Plains NTA3007 Operator Manual User Manual
Page 142
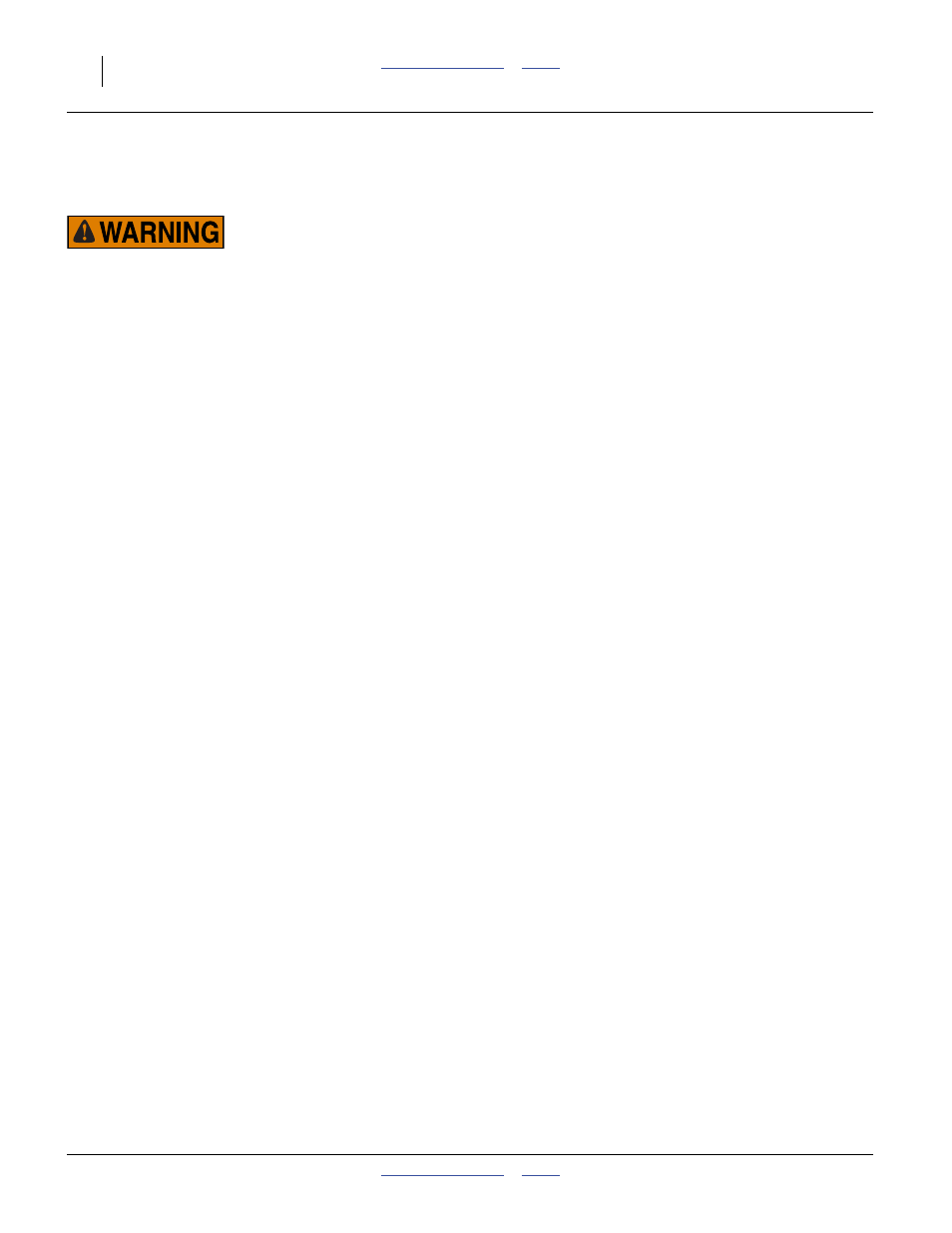
138
NTA907 or NTA3007
Great Plains Manufacturing, Inc.
166-371M
2012-07-02
Brake Drum and Liner Maintenance
Great Plains recommends having brakes serviced by trained
and fully equipped brake technicians.
Non-Asbestos Fibres Hazard:
Most recently manufactured brake linings are asbestos-free.
However, non-asbestos brake linings may contain one or more of a
variety of ingredients, including glass fibres, mineral wool, aramid
fibres, ceramic fibres and silica that can be health risks if inhaled.
Scientists disagree on the extent of the risks from exposure to these
substances. Exposure to silica dust can cause silicosis, a
non-cancerous lung disease. Silicosis gradually reduces lung
capacity and efficiency and can result in serious breathing
difficulty. Some scientists believe other types of non-asbestos
fibres, when inhaled, can cause similar diseases of the lung. Silica
dust and ceramic fibre dust are known to the State of California to
cause lung cancer. U.S. and international agencies have also
determined that dust from mineral wool, ceramic fibres and silica
are potential causes of cancer.
For silica, U.S. OSHA has set a maximum allowable level of
exposure of 0.1 mg/m
3
, 8-hour time-weighted average.
Some manufacturers of non-asbestos brake linings
recommend that exposures to other ingredients be kept
below 1.0 f/cc, 8-hour time-weighted average.
Scientists disagree, however, to what extent adherence to
these maximum allowable exposure levels will eliminate the
risk of disease that can result from inhaling non-asbestos
dust.
The following procedures for servicing brakes are
recommended to reduce exposure to non-asbestos fibre
dust, a cancer and lung disease hazard. A Material Safety
Data Sheet (MSDS) is available from Federal Mogul Friction
Products, U.S. telephone (540) 662-3871. Request MSDS
WNRE-05-155-4.
Use caution to avoid creating, breathing or ingesting dust
when servicing brakes. Check for applicable laws,
regulations and insurance/enterprise policies prior to
commencing work.
Recommended Work Practices
Separate Work Area - Service brakes in an area where
these precautions are always taken for all work. Wear
clothes used only for brake work.
Respiratory Protection - Wear a respirator equipped with a
high-efficiency (HEPA) filter approved by U.S. NIOSH or
MSHA for brake work.
Wear respiratory protection at all times during brake
servicing (including grinding or machining brake drums),
beginning with the removal of the wheels, through shop
cleanup after completion of brake work (including emptying
vacuums, changing HEPA filters and rag disposal).
Procedures for Servicing Brakes
• Service the removed brake assembly in a negative
pressure enclosure. The enclosure should be equipped
with a HEPA vacuum and worker arm sleeves. With the
enclosure in place, use the HEPA vacuum to loosen and
vacuum residue from brake parts.
• Alternatively, use a catch basin with water and a
biodegradable, non-phosphate, water-based detergent to
wash the brake drum and other brake parts. Apply the
solution with low pressure to prevent dust from becoming
airborne. Allow the solution to flow between brake drum
and brake support. Thoroughly wet the wheel hub and
brake assembly components to control dust, prior to
removal of brake shoes. Wipe parts clean with a cloth.
• If an enclosed vacuum system or brake washing
equipment is not available, carefully clean the brake parts
in open air. Use a fine mist from a pump spray bottle to
wet parts. Use a solution containing water, and, if
available, a biodegradable, non-phosphate, water-based
detergent. Thoroughly wet the wheel hub and brake
assembly components to control dust, prior to removal of
brake shoes. Wipe parts clean with a cloth.
Dust Control - Use only HEPA-equipped vacuum cleaners.
Never blow dust with an air gun. Do not dry brush parts.
Cleaning Fluids - NEVER use carcinogenic solvents,
flammable solvents, or solvents that can damage brake
components as wetting agents.
Work Area -. Clean work areas with a HEPA-equipped
vacuum cleaner or by damp wiping. NEVER use an ordinary
shop vac, compressed air or dry sweepers.
When replacing a HEPA filter, wet the used filter with a fine
water mist. Bag and carefully dispose of the used filter.
Hygiene - Wash hands immediately after brake work, and
before eating, drinking or smoking. Clean clothes with a
HEPA-equipped vacuum before removing them. Keep food
and drink out of the work area.
Shower after work. Do not wear work clothes home. Use a
vacuum equipped with a HEPA filter to vacuum work clothes
after they are worn. Launder them separately.
Waste Disposal - Dispose of discarded linings, used rags,
cloths and HEPA filters with care, such as in sealed and
labelled plastic bags. Consult applicable EPA, national,
regional and local regulations on waste disposal.
Regulatory Guidance - OSHA, NIOSH, MSHA, and EPA,
are regulatory agencies in the United States. These
references are to provide further guidance to employers and
workers employed within the United States. Employers and
workers employed outside of the United States should
consult the regulations that apply to them for further
guidance.