01 basic troubleshooting, 02 power source problems, 01 power source problems – Tweco 200DC Inverter Arc Welding Machine User Manual
Page 55: Section 5, Basic troubleshooting -1, Power source problems -1, Weldskill 200ac/dc inverter
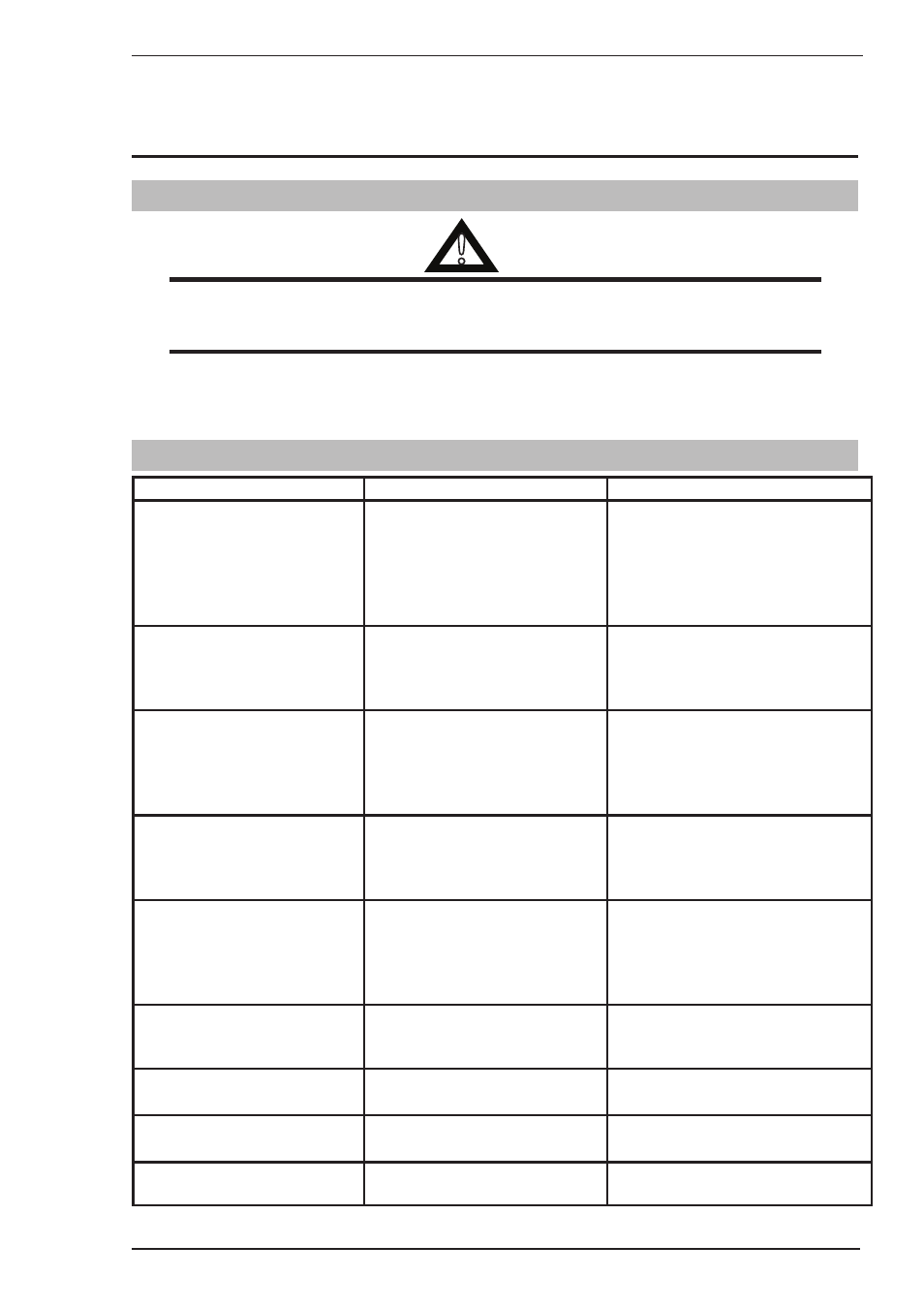
WELDSKILL 200AC/DC INVERTER
Manual 0-5207
5-1 POWER SOURCE PROBLEMS AND ROUTINE SERVICE REQUIREMENTS
SECTION 5:
POWER SOURCE PROBLEMS AND ROUTINE SERVICE
REQUIREMENTS
5.01 Basic Troubleshooting
!
WARNING
There are extremely dangerous voltage and power levels present inside this product. Do not attempt
to open or repair unless you are a qualified electrical tradesperson and you have had training in
power measurements and troubleshooting techniques.
If major complex subassemblies are faulty, then the Welding Power Source must be returned to an ac-
credited CIGWELD Service Provider for repair. The basic level of troubleshooting is that which can be
performed without special equipment or knowledge. Refer also to section 4 for solving welding problems.
5.02 Power Source Problems
FAULT
CAUSE
REMEDY
1 Mains supply voltage is
ON, power indicator is
illuminated however unit
will not commence welding
when the torch trigger
switch is depressed.
A
B
Power source is not in the
correct mode of operation.
Faulty torch trigger.
A
B
Set the power source to the
correct mode of operation with
the process selection switch.
Repair or replace torch trigger
switch/lead.
2 Mains supply voltage is
ON. Indicator light is not lit
and welding arc cannot be
established.
A
B
Primary control fuse is blown.
Broken connection in primary
circuit.
A
B
Replace primary control fuse.
Have an Accredited CIGWELD
Service Provider check primary
circuit.
3 Fault Indicator is illuminated
and unit will not commence
welding when the torch
trigger switch is depressed.
Duty cycle of power source has
been exceeded.
Leave the power source
switched ON and allow it to
cool. Note that fault indicator
must be extinguished prior to
commencement of welding.
4 Welding output continues
when torch trigger released
A
B
Trigger mode selection is in 4T
(LATCH) mode
Torch trigger leads shorted
A
B
Change to 2T (NORMAL) mode
Repair or replace Torch / trigger
lead
5 Welding output voltage
is present when the
torch trigger switch is
depressed but arc cannot be
established.
Poor or no work lead contact.
Clean work clamp area and ensure
good electrical contact.
6 Welding output voltage is
not present when torch
trigger depressed
Faulty trigger switch / lead
Repair or replace Torch / trigger
lead
7 TIG electrode melts when
arc is struck.
TIG torch is connected to
the (+) VE terminal.
Connect the TIG torch to the (-)
VE terminal.
8 Arc flutters during TIG
welding.
Tungsten electrode is too
large for the welding current.
Select the correct size of tungsten
electrode.
9 No HF output in HF mode
HF Circuit faulty
Have an Accredited CIGWELD
Service Provider check HF circuit.
Table 5-1: Power Source Problem