Sc-3000 – Tweco SC-3000 User Manual
Page 51
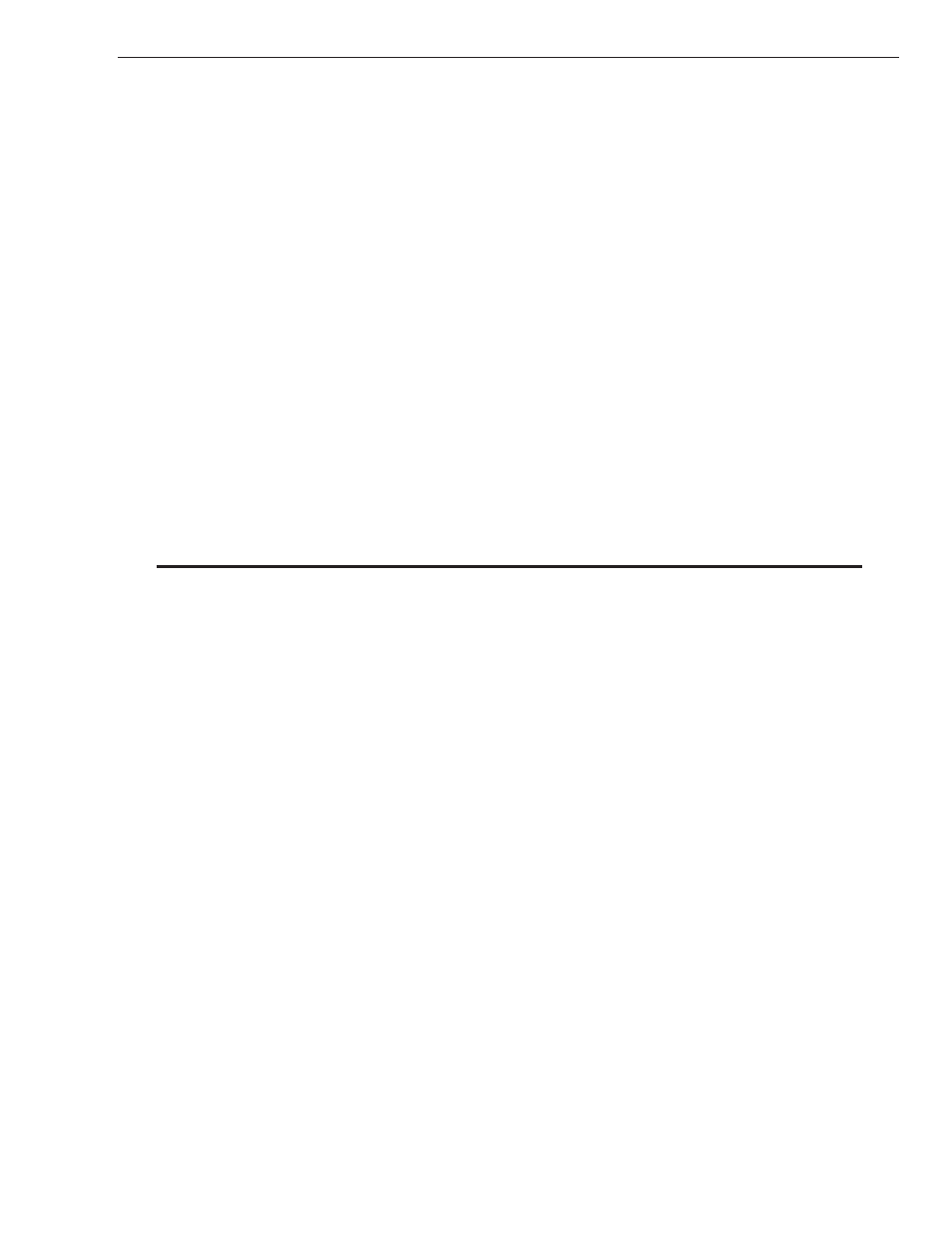
SC-3000
Manual 0-5100
4-11
OPERATION
Operation Sequence:
Assumes SW2, OK Source switch, on enclosure PCB set to “B” its factory default position.
1. CNC Start to THC Initial Position Start input.
a. If Preflow on THC terminal is set to zero the Torch moves to find plate then moves to pierce
height.
b. If Preflow is not zero Enable Ignition Plasma becomes active starting preflow via the plasma’s
Preflow On input (Refer to section 4.10 for more details).Torch moves to find the plate then
moves to pierce height.
2. Height found, torch at pierce height.
a. If Preflow on THC terminal is set to zero the Start (Enable Ignition Plasma) to plasma imitates
the plasma Preflow (default time 2 secs).. As Preflow time ends pilot arc is ignited.
b. If Preflow is not zero the Separate Ignition Plasma becomes active, sends Start to the Plasma.
The plasma whose preflow was already started by Enable Ignition Plasma, ignites its Pilot arc
immediately if plasma’s preflow timer has ended or as soon as it does end.
3. Arc Transfers, Plasma supply OK to Move on.
a. OK from plasma sent to THC Ready (Start XY) input. This moves torch to Elevate Height if
any set. This starts THC Pierce Delay.
NOTE
Torch remains at pierce or elevate height until THC Pierce Delay ends. This should be set equal to or longer than
CNC pierce delay. Longer allows torch to move away from the pierce slag before coming down to cut height.
b. At the same time, OK from plasma closes OK relay on SC3000 Enclosure PCB sending OK
to Move to the CNC.
• Motion delay for piercing is determined by CNC delay. In case CNC does not have ability
to set Pierce Delay then set SW2 to “A” and set desired pierce dwell time on THC Pierce
Delay. Torch will come down to cut height same time motion starts.
4. CNC Pierce dwell (delay) time ends.
a. CNC start moving torch horizontally.
5. THC Pierce Delay ends, torch moves down to Cut Height.
a. Control Delay time starts. THC is sampling the arc voltage, at end of control delay THC uses
the last stable sampled voltage as a reference to control height for rest of cut.
6. Corner
a. As the cutting table moves the torch through a corner or small radius the speed will be re-
duced. This causes the arc voltage to increase but we don’t want the THC to respond to this
change as it would move the torch into the plate. The CNC (cutting table controller) provides
a signal when it reduces speed which can be used to inhibit, disable or lock out the height con-
trol during these speed reductions.