Banner Safety Mat Monitoring Modules User Manual
Page 4
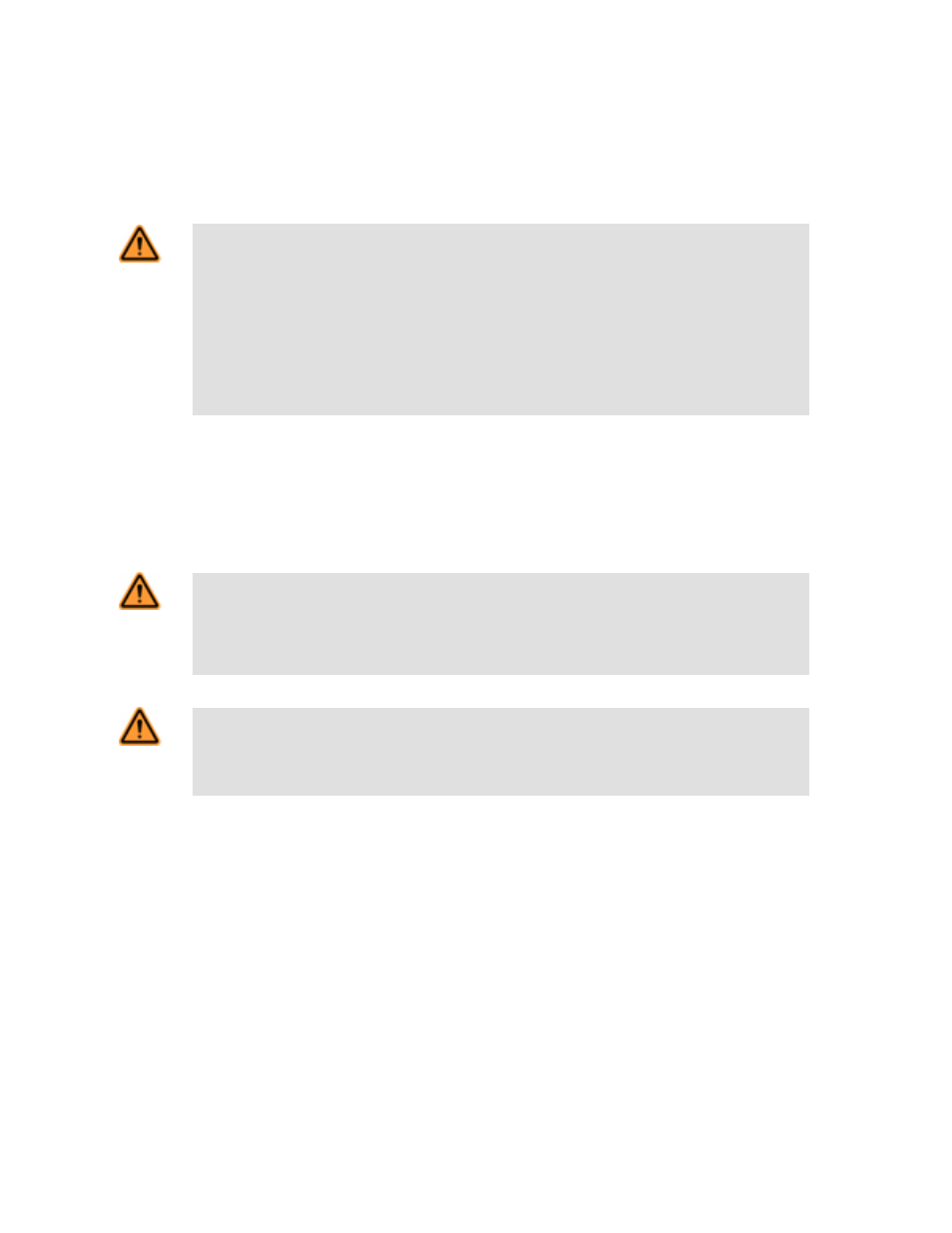
If Rm is:
Then
Less than 150 ohms AND you are using an AC
supply or DC supply greater than 20V dc
The mat resistance is acceptable and the safety mat checkout is complete.
Any other value
The resistance in the mat is too high for safe operation. Replace the safety mat. Repeat the mat resistance
checkout for the new mat.
WARNING: Safety Mat Resistance Values
Exceeding the maximum resistance
between the monitoring channels (usually due to degradation of the mat) can result in
the increase of response time or complete loss of the sensing function of the safety mat, when it is stepped on (shorted).
This can result in serious injury or death.
Exceeding the maximum resistance within a contact monitoring channel can result in the Module issuing a stop command (opening
the safety outputs) when no person is present.
To ensure proper operation, verify the quality and specifications of the mat being connected to this Module, and perform
periodic checks of the safety mat's resistance, as described in the Safety Mat Initial Checkout.
Reset Switch Connection
The reset circuit switch can be any mechanical switch, such as a normally open momentary switch, or a two-position key switch. The reset switch must be capable of
reliably switching 12 to 30V dc at 20 to 50 milliamps. As shown in the hookup drawings, the reset switch connects between Safety Module terminals S33 and S34.
The reset switch must be located outside of – and not be accessible from – the area of dangerous motion, and must be positioned so that any area of dangerous motion
may be observed by the switch operator during the reset procedure. See warning below.
WARNING: Reset Switch Location
All reset switches must be accessible only from outside, and in full view of, the hazardous area. Reset switches must also
be out of reach from within the safeguarded space, and must be protected against unauthorized or inadvertent operation
(e.g., through the use of rings or guards). If any areas are not visible from the reset switch(es), additional means of safeguarding
must be provided. Failure to do so could result in serious bodily injury or death.
WARNING: Reset Routine Required
U.S. and international standards require that a reset routine be performed after clearing the cause of a stop condition (e.g., arming an
E-stop button, closing an interlocked guard, etc.). Allowing the machine to restart without actuating the normal start command/
device can create an unsafe condition which could result in serious injury or death.
Automatic Reset Mode
The Safety Module may be configured (via hookup) for automatic reset. If no MSC contacts are monitored, install a jumper between terminals S32 and S35 (see hookups).
The Safety Module will reset (and its outputs energize) as soon as the switch returns to its armed (closed-contact) position.
Automatic reset is useful for some automated processes. However, if automatic reset is used, it is necessary to provide a means of preventing resumption of
hazardous machine motion, until an alternate reset procedure is performed. The alternate procedure must include a reset/restart switch, located outside the area of
dangerous motion and positioned so that any area of dangerous motion may be observed by the switch operator during the reset procedure. See Warning.
Connection to the Machine to be Controlled
The machine hookup diagram shows a generic connection of the Safety Module's redundant output circuits to the master stop control elements (MSCs). An MSC is defined
as an electrically powered device, external to the Safety Module, which stops the machinery being controlled by immediately removing electrical power to the machine and
(when necessary) by applying braking to dangerous motion. This stopping action is accomplished by removing power to the actuator of either MSC.
Overvoltage Category II and III Installations (EN 50178 and IEC 60664-1)
The Safety Module is rated for Overvoltage Category III when voltages of 1V to 150V ac/dc are applied to the output relay contacts. It is rated for Overvoltage Category II
when voltages of 151V to 250V ac/dc are applied to the output relay contacts and no additional precautions are taken to attenuate possible overvoltage situations in the
supply voltage. The Module can be used in an Overvoltage Category III environment (with voltages of 151V to 250V ac/dc) if care is taken either to reduce the level of
electrical disturbances seen by the Module to Overvoltage Category II levels by installing surge suppressor devices (e.g., arc suppressors), or to install extra external
insulation in order to isolate both the Safety Module and the user from the higher voltage levels of a Category III environment.
SM-xA-5A Safety Mat Monitoring Modules
4
www.bannerengineering.com - tel: 763-544-3164
P/N 122364 rev. C