Mechanical installation, Electrical installation – Banner Safety Mat Monitoring Modules User Manual
Page 6
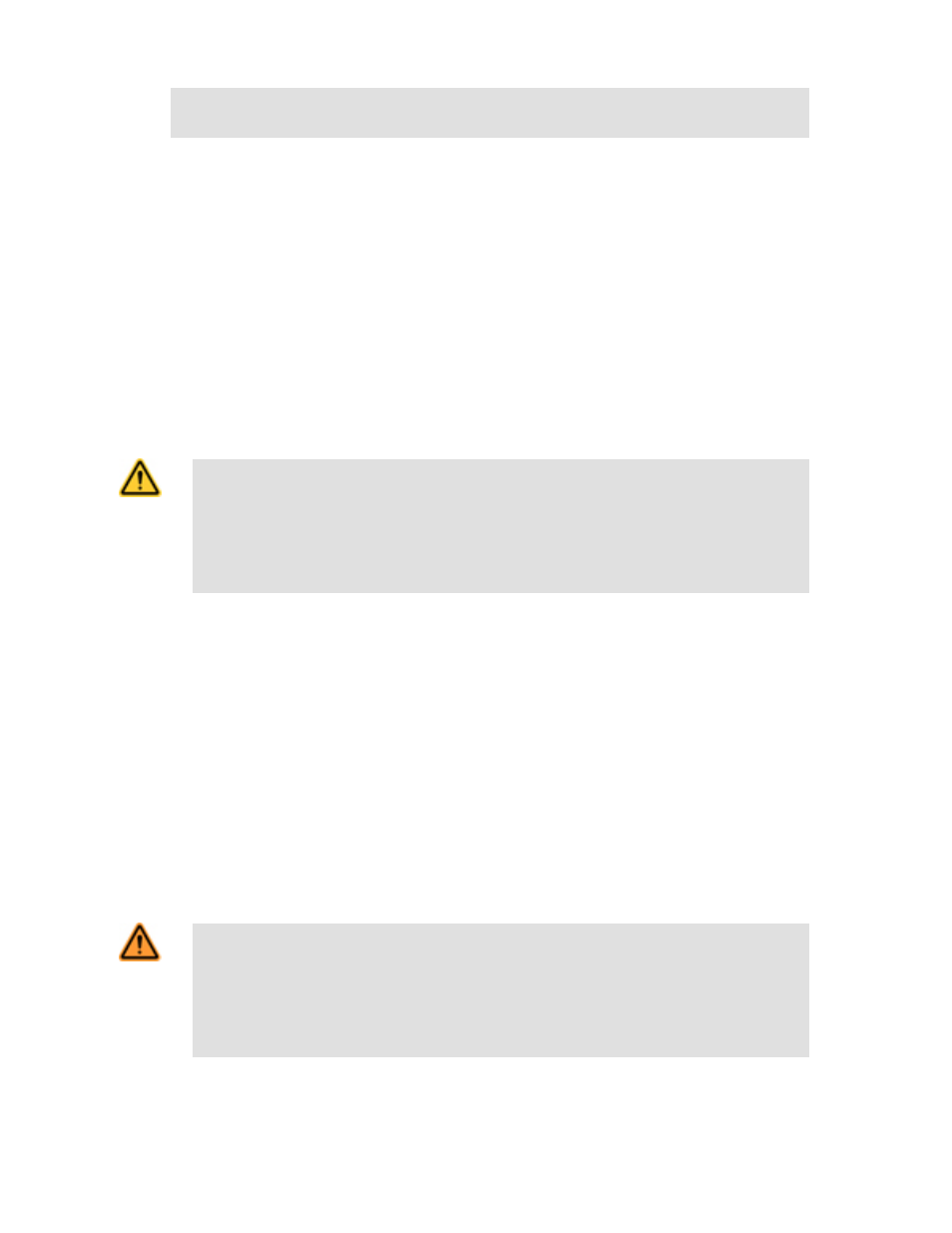
they are not conclusive determinations. The employer should consider all factors, including the physical ability
of the operator, when determining the value of K to be used.
If an individual can cross completely over the sensor and be no longer detected, supplemental safeguarding or other means should be
used to prevent unexpected startup and exposure to a hazard. At a minimum, the safety mat system (or the machine control) must be
manually reset and require re-initiation of the normal actuating means prior to the start or re-start of the machine cycle.
Mechanical Installation
Route the mat cable to the Safety Module location. The Safety Module must be installed inside an enclosure. It is not designed for ex-
posed wiring. It is the user’s responsibility to house the Safety Module in an enclosure with NEMA 3 (IEC IP54) rating, or better.
The Safety Module mounts directly to standard 35 mm DIN rail; see Dimensions.
Heat Dissipation Considerations. For reliable operation, ensure that the operating specifications are not exceeded. The enclosure must
provide adequate heat dissipation, so that the air closely surrounding the Module does not exceed the maximum operating temperature
stated in the Specifications. Methods to reduce heat build-up include venting, forced airflow (e.g., exhaust fans), adequate enclosure
exterior surface area, and spacing between modules and other sources of heat.
Electrical Installation
CAUTION: Shock Hazard
Always disconnect power from the Banner product and the guarded machine before making any connec-
tions or replacing any component. Electrical installation and wiring must be made by qualified personnel
and must comply with the NEC (National Electrical Code), ANSI NFPA79 or IEC 60204-1 and -2, and all
applicable local standards and codes. Use extreme caution to avoid electrical shock at all times. Seri-
ous bodily injury or death could result.
The Safety Module is powered by either a 12-24V dc supply at 4W or an ac supply (115V ac, model SM-GA-5A, or 230V ac, model SM-
HA-5A) at 7VA. The sensor circuit, which monitors the conductive elements (plates) of the safety mat, consists of two channels (A and B)
that issue a stop command (i.e., open the safety outputs) when an individual steps onto the safety mat, shorting the two channels togeth-
er.
It is not possible to give exact wiring instructions for a safety module which interfaces to a multitude of machine control configurations.
The following guidelines are general in nature.
Since the Safety Module functions by detecting the short circuit between the channels, resistance to electrical current flow in the contact
monitoring circuit impacts the operation and the safety of the system. Total resistance includes contact resistance of the internal mat
contacts, the number of mats in the circuit, and the wire resistance of the interconnect cables and connections.
The only limitation on the number of mats that can be connected in series is the amount of resistance. The total resistance within each
channel can not exceed 250 ohms when the Module is supplied by 24V dc or an ac power supply, and no more than 25 ohms when the
Module is supplied by 12V dc.
The resistance between the channels when shorted together (i.e., when an individual steps on the mat) can not exceed 150 ohms (24V
dc or an ac supply) or 10 ohms (12V dc supply).
WARNING: Multiple Safety Mats
Whenever two or more safety mats are connected to the same Safety Mat Monitor Module, the corre-
sponding conductive elements (plates) of all mats must be connected together in series, as shown in the
hookup drawing. Never connect the conductive elements (plates) of multiple safety mats in parallel;
this defeats the ability of the Safety Module to detect open connection wires to each mat, which
would create an unsafe condition that could result in serious injury or death.
NOTE: The minimum amount of time for the Module to detect a STOP condition is 15 ms. This "recovery time" (OFF state) is required for
the internal integrity tests to complete, allowing a reliable reset to occur. A lockout may occur if the Module is cycled too quickly. To clear
the lockout, the inputs must be re-cycled, meeting the minimum recovery time requirements.
SM-xA-5A Safety Mat Monitoring Modules
6
www.bannerengineering.com - tel: 763-544-3164
P/N 122364_Web
rev. C