Warning, Notice regarding mpces – Banner Interface Modules User Manual
Page 4
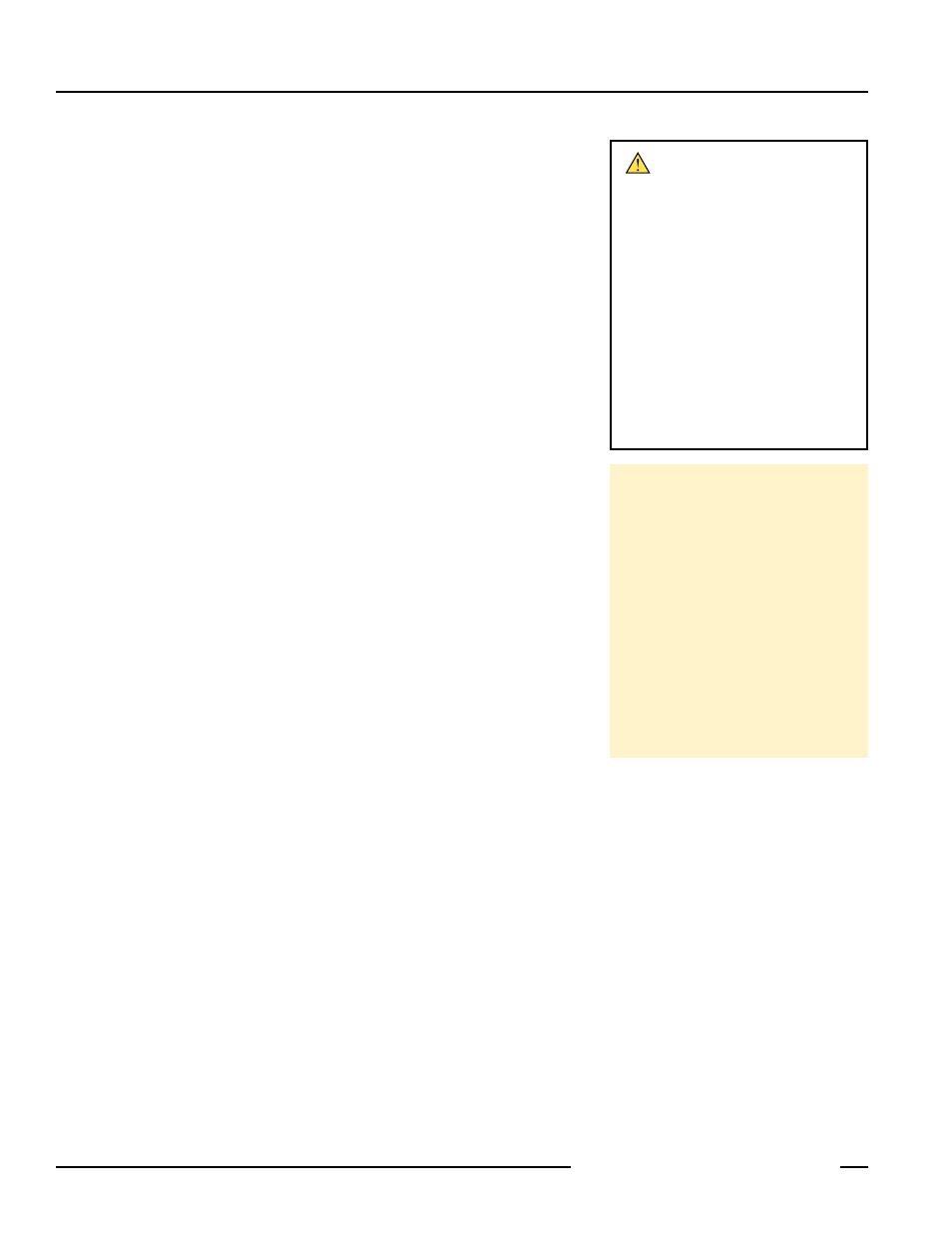
Models SC-IM9.. – Safety Controller Interface Modules
4
P/N 131845
Banner Engineering Corp. • Minneapolis, MN U.S.A.
www.bannerengineering.com • Tel: 763.544.3164
As the SC-IM9.. Module contacts are rated at 10 amps, they can be used as MPCEs to directly
start and stop dangerous motion, or they may be used to power larger MPCE devices. It is
important to note that any MPCE element must be part of the EDM loop.
To satisfy the requirements of Safety Category 3 or 4 of ISO 13849-1 (EN 954-1) and control
reliability (OSHA/ANSI), all MPCEs must each offer at least one normally closed forced-
guided monitor contact. One normally closed monitor contact from each MPCE is connected
to the Safety Controller's monitoring contact feedback input, as shown in the hookups. (Each
of the Safety Controller's 22 safety inputs—S1 through S22—can be configured as external
device monitoring inputs. Refer to the SC22-3 manual and PCI software interface for more
information.) Both single N.C. contacts (21–22) from each contactor are pre-wired in series in
each contactor pair for single-channel EDM monitoring.
If the MPCEs are controlled by the SC-IM9.. Module, the normally closed contacts of both
the Module and the MPCE can be switched in series to the same EDM input. In operation,
if the MPCE fails in the energized condition, the associated monitor contact will remain
open. As a result, the Safety Controller will detect the MPCE failure and prevent successive
machine cycles. It is the user’s responsibility to monitor the contactors’ N.C. contacts, to
ensure that any single failure will not result in a hazardous condition and will prevent a
successive machine cycle.
Many types of mechanisms are used to arrest dangerous machine motion. Examples include
mechanical braking systems, clutch mechanisms, and combinations of brakes and clutches.
Additionally, control of the arresting scheme may be hydraulic or pneumatic. As a result,
an MPCE may be one of several control types, including a wide variety of contactors and
electromechanical valves. If your machine documentation leaves any doubt about the proper
connection points for the Interface Module output contacts, do not make any connections.
Contact the machine builder for clarification regarding connection to the MPCEs.
WARNING . . .
Not for Use
As a Stand-Alone Safety Module
1. DO NOT connect E-stop switches,
2-hand-control switches, safety interlock
switches, or similar devices directly to this
Interface Module.
2. ALWAYS connect terminals 21–22 of this
Interface Module to the monitoring input of
the SC22-3 Safety Controller (see Figure 2).
This Module does not have the circuitry required
to perform a self-check. A single fault inside the
unit can go undetected and create an unsafe
condition. Failure to properly connect this
Module to the SC22-3 Safety Controller could
result in serious injury or death.
NOTICE Regarding MPCEs
To achieve control reliability, two
machine primary control elements (MPCEs)
are required to control each machine hazard.
Each MPCE must be capable of immediately
stopping the dangerous machine motion,
irrespective of the state of the other. Some
machines offer only one primary control
element. For such machines, it is necessary to
duplicate the circuit of the single MPCE to add
a second MPCE.
MPCEs must offer at least one forced-guided
auxiliary contact which is wired to the Safety
Controller's monitoring contact feedback input
(see hookup diagram).