Rockwell Automation FlexPak Plus NRG DC Drive User Manual
Page 7
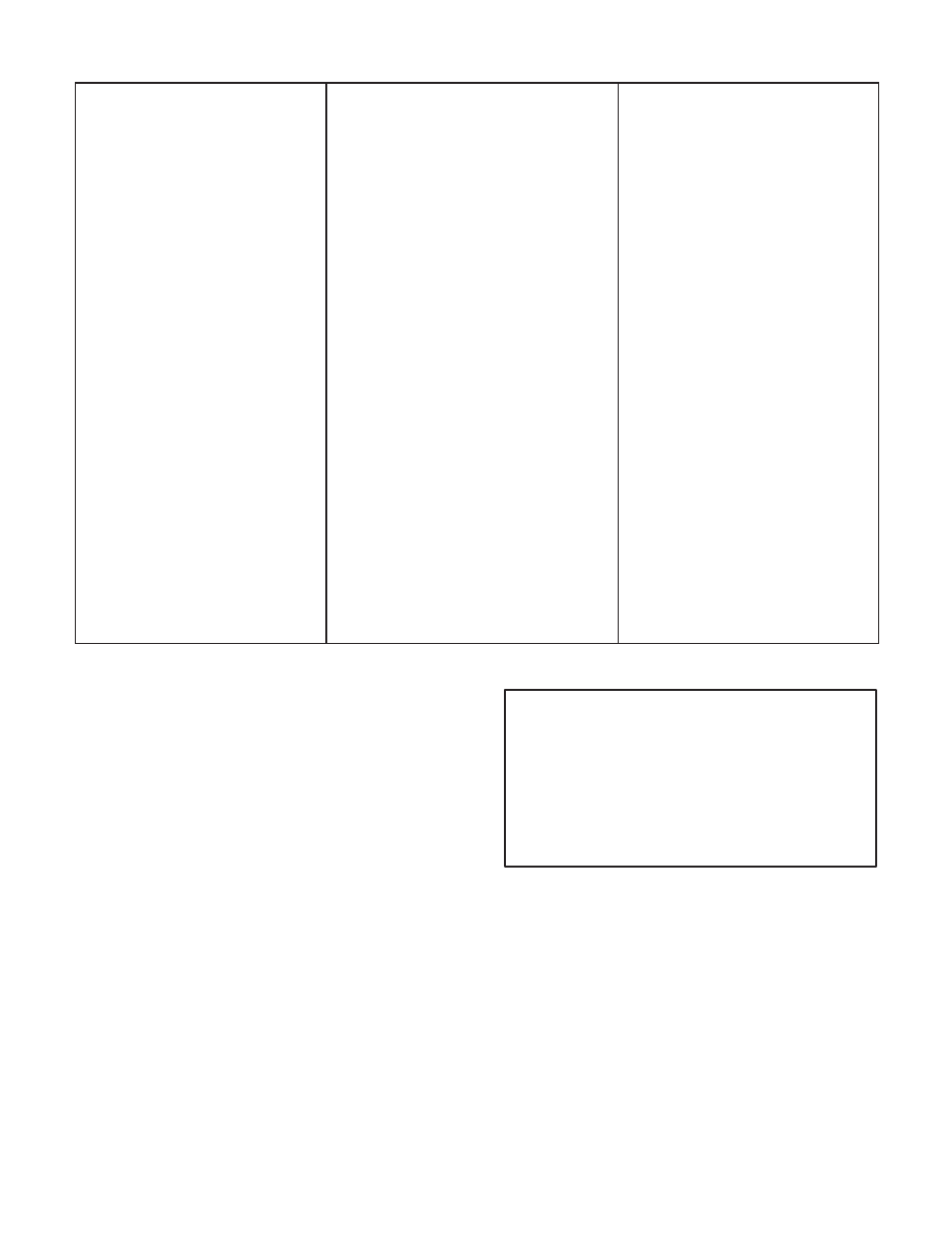
6
Table 2.B - Specifications
AĆC Line input Voltage
230/460 VAC (nominal, 60 HZ)
220/440 VAC (nominal, 50 Hz)
three phase only
Line Voltage Variation
"10% of nominal
AĆC Line Frequency
Three Phase, 50/60 Hz
Line Frequency Range
48Ć62 Hz
Output Voltages
(armature and field)
See Table 2.D
ControllerĆDrive HP Range
3Ć20 (with 230 VAC input)
3Ć40 (with 460 VAC input)
Direction Control
Standard: Unidirection
Optionally: Forward/Reverse
Maximum Speed Adjustment
70 to 100% of base motor speed
(user adjustable)
Minimum Speed Adjustment
up to 30% of base motor speed
(user adjustable)
Operator Speed Adjustment
Infinitely adjustable with
optional control pot
(up to 100% of base speed)
Operator Torque Adjustment
Infinitely adjustable at optional control
pot
(10 to 150% of rated load)
IRDrop Compensation
0 to 12% of rated load
(user adjustable)
Controllable Speed Range
20:1
Current Limit
Factory shipped: 150% of full load
User adjustable: 10 to 150% of full load
Regulator (with 95% load change)
3 to 5% with voltage feedback
1.0% with specified tachometer feedback
0.5% with specified tachometer feedback
Minimum Load for Stable Operation
5%
Acceleration/Deceleration Rates
0.5 to 30 sec. linear time
(userĆadjusted separately)
Armature Circuit Overload Capacity
150% of armature current rating
for 1 minute (max.)
Efficiency (rated speed/rated load)
Controller only: 97%
Complete drive including
motor 85% (typical) ➀
Displacement Power Factor
68% (typical) ➀
Transient Protection
MOV and Output RC Circuit
Controller Service Factor
1.0
Duty
Continuous
Ambient Temperature
(storage and operational)
0
°
to 55
°
C (32
°
to 131
°
F)
Relative Humidity
(storage and operational)
5 to 95% (without condensation)
Operational Altitude
To 3300 ft (1000 m) above
sea level without derating
Controller Weight (approx.)
37 lb (87.8 Kg)
Controller Dimensions (LWD)
(A) = 18.75x10.62x8.00 in.
(476x270x203 mm)
(B) = 18.75x10.62x9.50 in.
(476x370x241 mm)
A - 3Ć10 HP/230V, 3Ć20 HP 460V
B - 15Ć20 HP/230V, 25Ć40 HP 460V
➀
Typical percent shown. Exact figure dependent on motor base speed and frame size.
2.4 Specifications
- The more important specifiĆ
cations for the FlexPak Plus controller are listed in Table
2.B. Refer also to Table 2.D where other ratings are indiĆ
cated in relation to dĆc motors of specific horsepower.
2.4.1 Line Frequency - The FlexPak Plus controller is
able to operate without modification from a threeĆphase
power source having a frequency range from 48 to 62
Hz.
2.4.2 Voltage Tolerance - The FlexPak Plus controller
delivers output current and voltage, as listed in Table
2.D. It will also operate within these regulation specificaĆ
tions even with incoming line voltage at +/Ć10% of nomiĆ
nal.
2.4.3 Line Impedance Requirements - The FlexPak
Plus controller must be connected to a plant power supĆ
ply with maximum permissible available symmetrical
RMS fault current no greater than 5000 amperes. (Refer
to Table 2.D.)
WARNING
DO NOT OPERATE THE FLEXPAK PLUS CONĆ
TROLLER ON POWER SUPPLIES WITH AVAILĆ
ABLE SHORTĆCIRCUIT CURRENTS IN EXCESS
OF 5000 AMPERES. DAMAGE TO EQUIPMENT
AND PERSONAL INJURY MAY OCCUR. EXTERĆ
NAL DISCONNECT MEANS MUST HAVE ABILĆ
ITY TO INTERRUPT A 5000 AMP RMS CURRENT
FAULT.
2.4.4 Relay Control Circuit - The regulator board is
set up for use with 24 VDC main contactors having a coil
resistance greater than or equal to 100 ohms, 14C300
only; 14C301 to 14C305 is 1000 ohms. The control logic
sequences the contractor and the control relay on the
regulator so that current flow thru the main contactor is
never broken in normal operation by the contracts. ReĆ
fer to Figures 5.1, and 5.2.
The standard controller includes an M contactor. HowĆ
ever, the Optional Basic Controller does not have an M
contactor. An M contactor is required to provide positive
power disconnect in all applications.