Rockwell Automation FlexPak Plus NRG DC Drive User Manual
Page 40
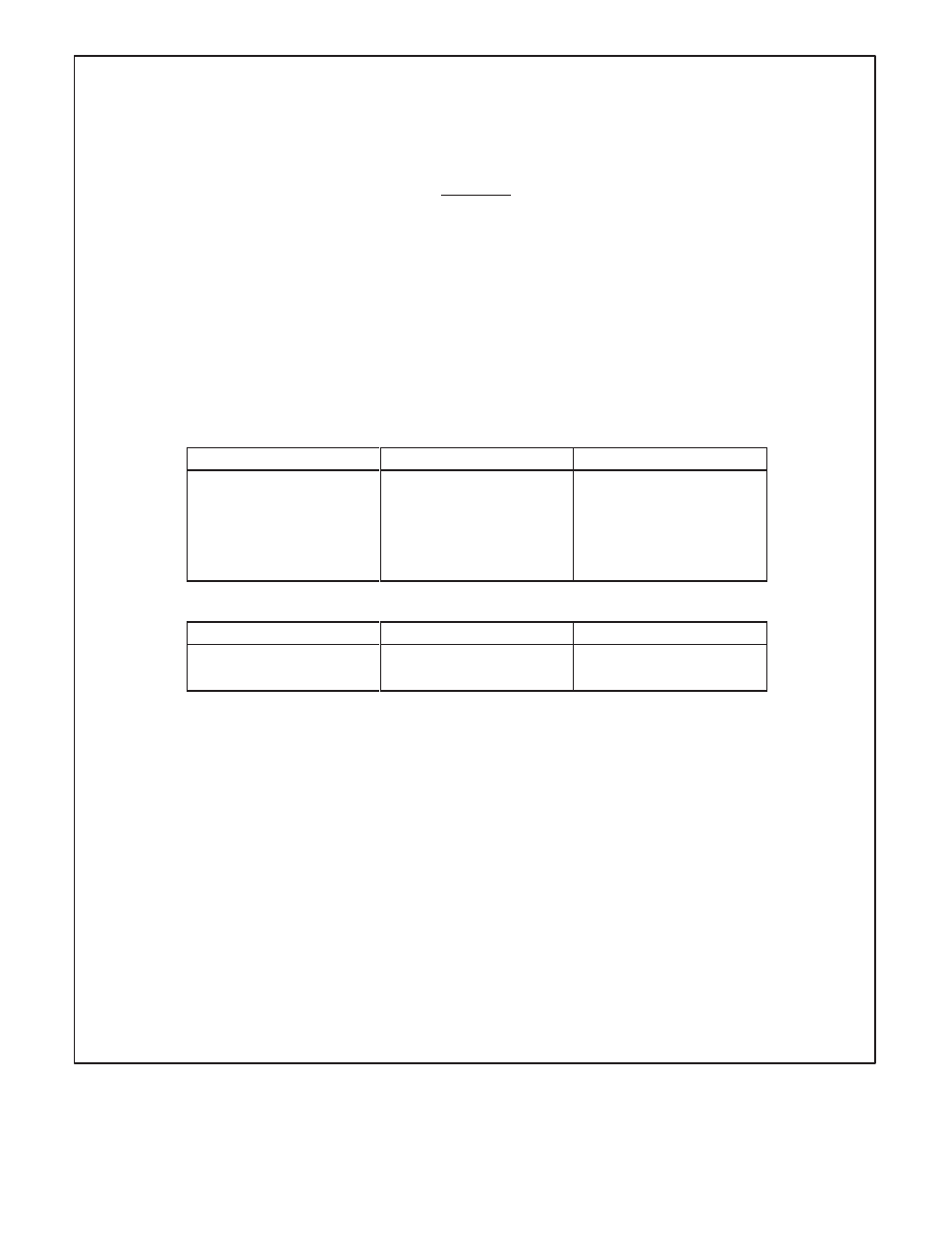
39
NOTE SHEET
1>
Function of panel rating, see Sh. 8.
2>
If motor has series field, wire between 45/52 and FM contact is removed, and series field
kit installed.
3>
This contact is present only on Assy. No. 802220–RB & SB.
4>
For Current Scaling, see table on Sh. 9.
5>
For Feedback select, see table on Sh. 9.
6>
Remove jumper (J4) if Auto/Manual switch is used.
7>
Remove jumper (J9) if Reverse Contactor kit is used.
8>
Wiring for tachometer input leads must be tightly twisted with two full turns per inch,
minimum. Leads must be run physically separated from all power circuit wiring. (See note 14
for insulation temp. rating.)
9>
For DC tach, jumper is connected in this location.
100% Voltage
Tach
Motor (RPM)
23V
35V
58V
69V
88V
115V
175V
175V
20VDC/1000 RPM
20VDC/1000 RPM
50VDC/1000 RPM
20VDC/1000 RPM
50VDC/1000 RPM
100VDC/1000 RPM
50VDC/1000 RPM
100VDC/1000 RPM
1150
1750
1150
3450
1750
1150
3450
1750
10>
For AC tach, jumper is connected in this location.
100% Voltage
Tach
Motor (RPM)
52V
79V
155V
45VAC/1000 RPM
45VAC/1000 RPM
45VAC/1000 RPM
1150
1750
3450
11>
Aux. Contact rating: 1 Amp @ 30 VDC or 0.5 Amp @ 120 VAC (Resistive).
12>
User convenience terminal for #14 AWG max. wire size.
13>
All wiring for remote Speed Pot. and Torque Pot. must utilize tightly twisted wire with two
full turns per inch, minimum. All wiring for remote operators must be run in separate con-
duit, isolated from all power wiring. (See note 14 for insulation temp. rating.) See I/M
for details.
14>
Recommended insulation Temp. Rating: 75
_
C.
W/D 30070-1 (Sheet 10 of 13)
Figure 5.17A - Technical Notes