Rockwell Automation FlexPak Plus NRG DC Drive User Manual
Page 19
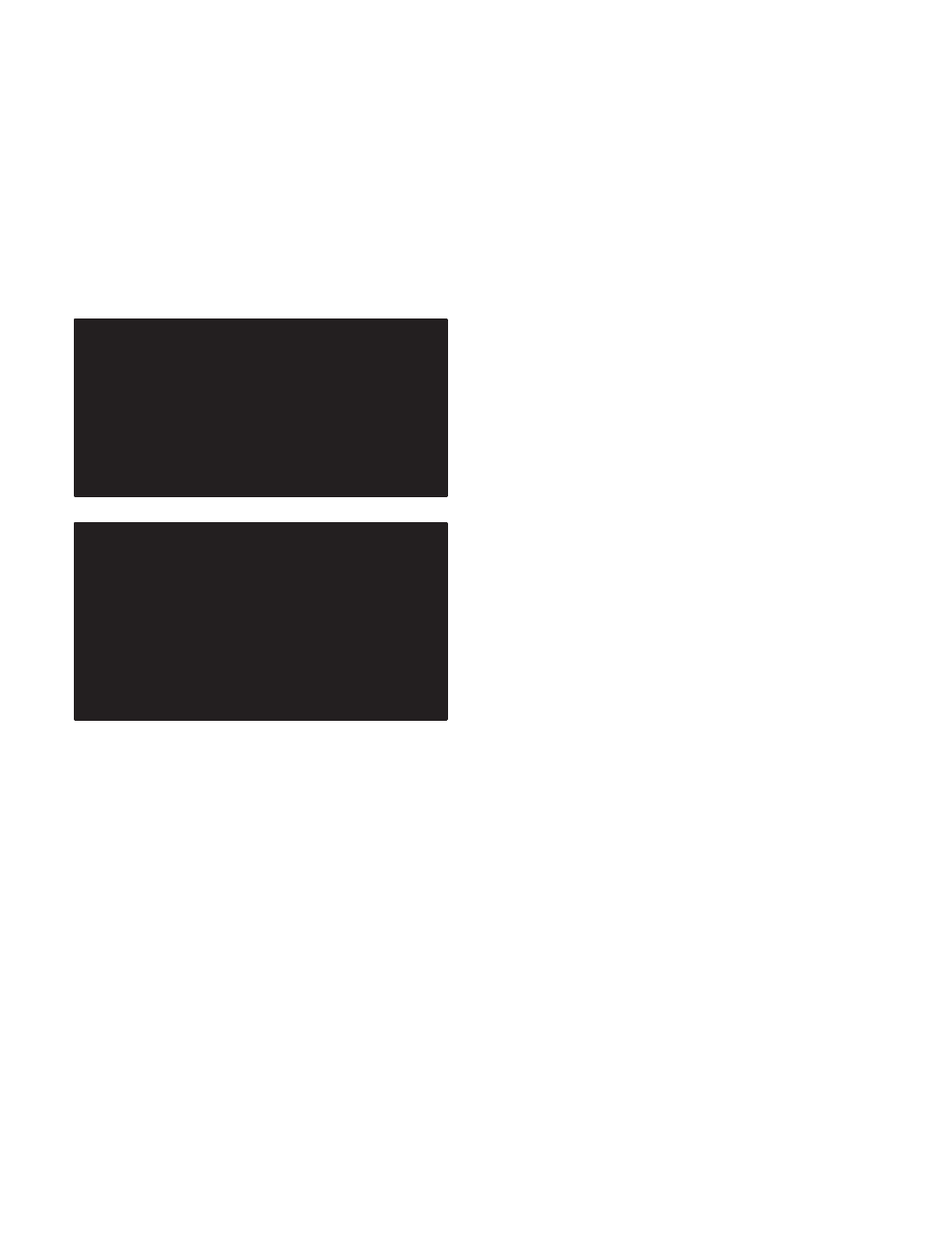
18
SECTION 5
TROUBLESHOOTING
5.0 General
- This Section details troubleshooting
information for the FlexPak Plus controller. Its organizaĆ
tion is as follows:
D General troubleshooting concepts (Paragraphs 5.1,
5.2, 5.3 and 5.4)
D Specific symptom/probable cause/recommended
procedures (Paragraph 5.5)
D Reference schematics, photos and diagrams of the
controller (Paragraph 5.6)
DANGER
CONTROLLER EQUIPMENT IS AT LINE VOLTĆ
AGE WHEN AĆC POWER IS CONNECTED TO
THE POWER UNIT IN THE FLEXPAK PLUS
CONTROLLER. THUS, AĆC POWER MUST BE
REMOVED FROM THE UNIT BEFORE IT IS SAFE
TO TOUCH THE INTERNAL PARTS OF THE
FLEXPAK PLUS. PERSONAL INJURY MAY REĆ
SULT UNLESS POWER IS REMOVED.
DANGER
THE FLEXPAK PLUS CONTROLLER SHOULD
BE SERVICED ONLY BY QUALIFIED ELECĆ
TRICAL MAINTENANCE PERSONNEL FAĆ
MILIAR WITH THE CONSTRUCTION AND OPĆ
ERATION OF ALL APPLICATION EQUIPMENT
IN THE SYSTEM. PERSONAL INJURY AND/OR
EQUIPMENT DAMAGE MAY OCCUR IF INDIVIDĆ
UALS ARE NOT FAMILIAR WITH THE HAZARDS
RESULTING FROM IMPROPER OPERATION.
In addition to stepĆbyĆstep troubleshooting procedures,
there are some generalized comments that should be
kept in mind at all times. These may be divided into wirĆ
ing errors (Paragraph 5.1), incoming aĆc line problems
(Paragraph 5.2), motor problems (Paragraph 5.3) and
mechanical problems (Paragraph 5.4).
A number of optional kits have also been developed to
assist in troubleshooting the drive. These are:
D Status/Diagnostic indicator kit which installs on the
faceplate of the drive & utilizes a LCD to visually
enunciate 13 critical drive functions in regards to their
status as well as indicating the specific fault area.
(Refer to Instruction Manual DĆ3963).
D The Diagnostor which is a portable device about the
size of a digital voltmeter. The Diagnostor will
exercise the regulator module and the digital driver
board and logically determine the operating condiĆ
tions of these modules. It also has the ability to
analyze the power bridge circuitry while the drive is
operating and determine if a problem exists within
the power bridge area. The diagnostor uses a LCD to
visually enunciate the logic output condition of its
test. Two terminals coupled with specified pushbutĆ
ton positions on the Diagnostor faceplate allow
access to various waveforms and voltages within the
controller via a scope or meter to assist in troubleĆ
shooting the drive.
D The test meter adapter kit provides a convenient
means of monitoring voltage on the regulator modĆ
ule with an external user supplied voltmeter (Refer to
Instruction Manual DĆ3970)
5.1 Wiring Errors
- The single most common probĆ
lem preventing normal dĆc drive operation is incorrect
wiring within a system. A maintenance person should
spend at least five minutes carefully looking over the
wiring before taking active steps involving tests and reĆ
placement. Remember that a loose or grounded wire
can occur in a controller that had previously been funcĆ
tioning correctly if initial wiring techniques were poorly
performed.
For those not familiar with proper FlexPak Plus controlĆ
ler wiring, other Sections in this manual may be conĆ
sulted. For more complex problems, Section 7 may be
used to uncover wiring problems in the optional ModifiĆ
cation Kits.
5.2 AĆC Line Problems
- The following are typical
problems located on the incoming aĆc line:
D AĆc line voltage incorrect for the specific controller,
which may operate on 230 or 460 VAC @ 60 Hz.
D Main disconnect switch contains fuses improperly
rated for the drive. (The fuses must be large enough
to prevent nuisance tripping yet small enough to
protect the circuit and equipment on the circuit.)
D AĆc conductors must be of adequate size for the
application.
D If an isolation transformer is used, it must be sized
according to the requirements of the drive system.
The transformer itself must be wired for the correct
output voltage (230/460 VAC) in relation to the
FlexPak Plus controller.