Chapter 4 installing the drive, Hapter, Installing the drive – Rockwell Automation SP500 AC Drive Installation and Operation Manual User Manual
Page 39
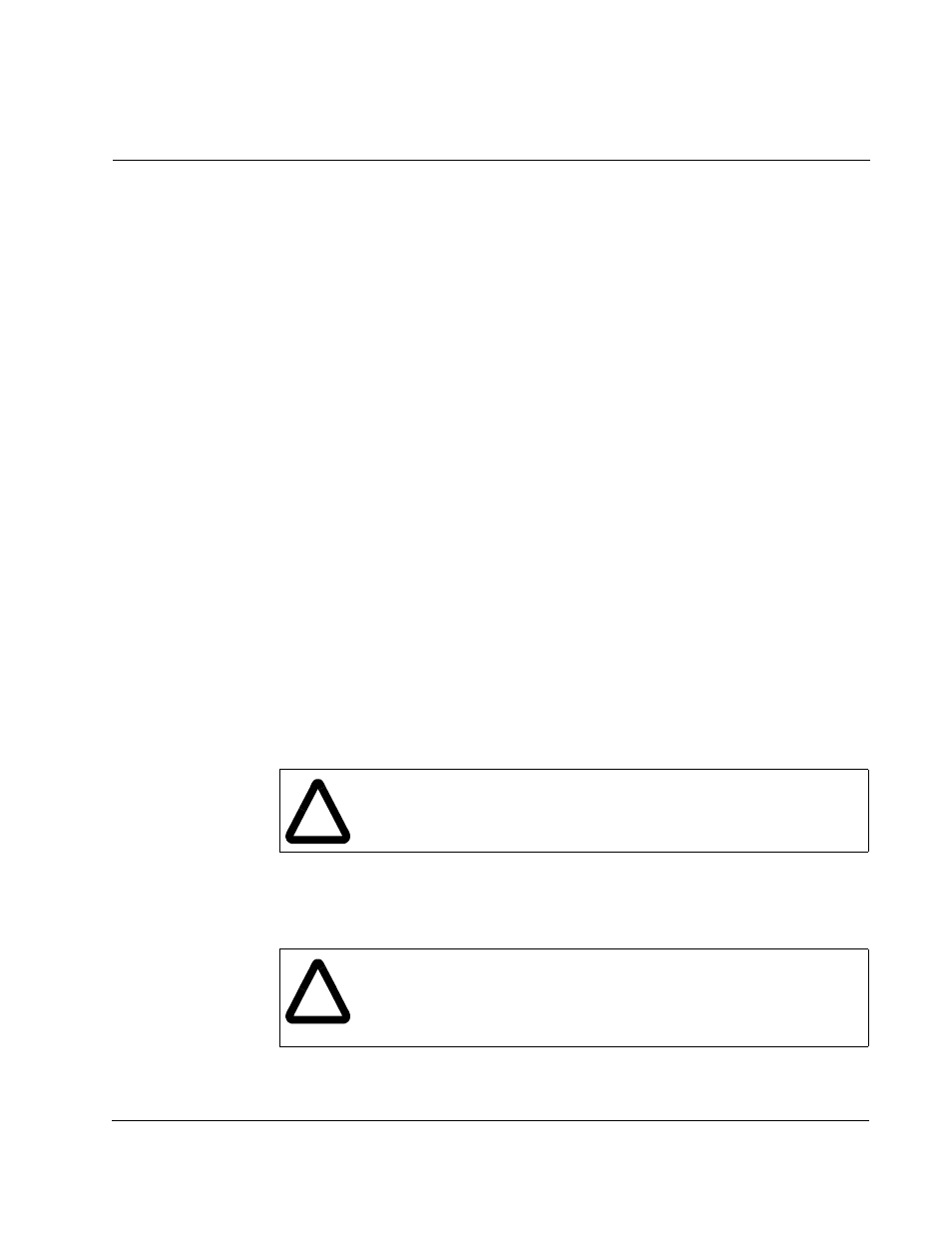
Installing the Drive
4-1
C
HAPTER
4
Installing the Drive
This chapter shows how to mount the SP500 drive and its external components. Also
shown are the entry areas for routing wiring in and out of the drive.
4.1
Mounting the Drive
Attach the drive to the selected flat, vertical surface using the mounting holes
provided. Enclosure A drives have two mounting holes, which are accessible after the
cover is removed. Enclosure B, C, and D drives have four mounting holes. In order to
maintain a flat mounting surface and to ensure that bolt tightness is maintained, use
washers under the bolt heads. Refer to figures 3.1 through 3.4 for drive mounting
dimensions. Use the following user-supplied mounting bolts and washers:
•
Enclosure A drives: two M6 (1/4”)
•
Enclosure B drives: four M8 (5/16”)
•
Enclosure C drives: four M8 (5/16”)
•
Enclosure D drives: four M8 or M10 (5/16” or 3/8”)
4.2
Routing Wires
All wiring should be installed in conformance with the applicable local, national, and
international codes (e.g., NEC/CEC). Signal wiring, control wiring, and power wiring
must be routed in separate conduits to prevent interference with drive operation. Do
not route wires behind the drive. Use grommets when hubs are not provided to guard
against wire chafing. Figures 4.1 through 4.4 show the wire routing, grounding
terminal, and power terminal strips of the SP500 drives.
Do not route more than three sets of motor leads through a single conduit. This will
minimize cross-talk that could reduce the effectiveness of noise reduction methods. If
more than three drive/motor connections per conduit are required, you must use
shielded cable. If possible, each conduit should contain only one set of motor leads.
!
ATTENTION: Do not route signal and control wiring in the same conduit
with power wiring. This can cause interference with drive operation.
!
ATTENTION: Unused wires in conduit must be grounded at both ends
to avoid a possible shock hazard caused by induced voltages. Also, if a
drive sharing a conduit is being serviced or installed, all drives using this
conduit should be disabled to eliminate the possible shock hazard from
cross-coupled motor leads.