USG Casting Fireplace Surrounds User Manual
Page 25
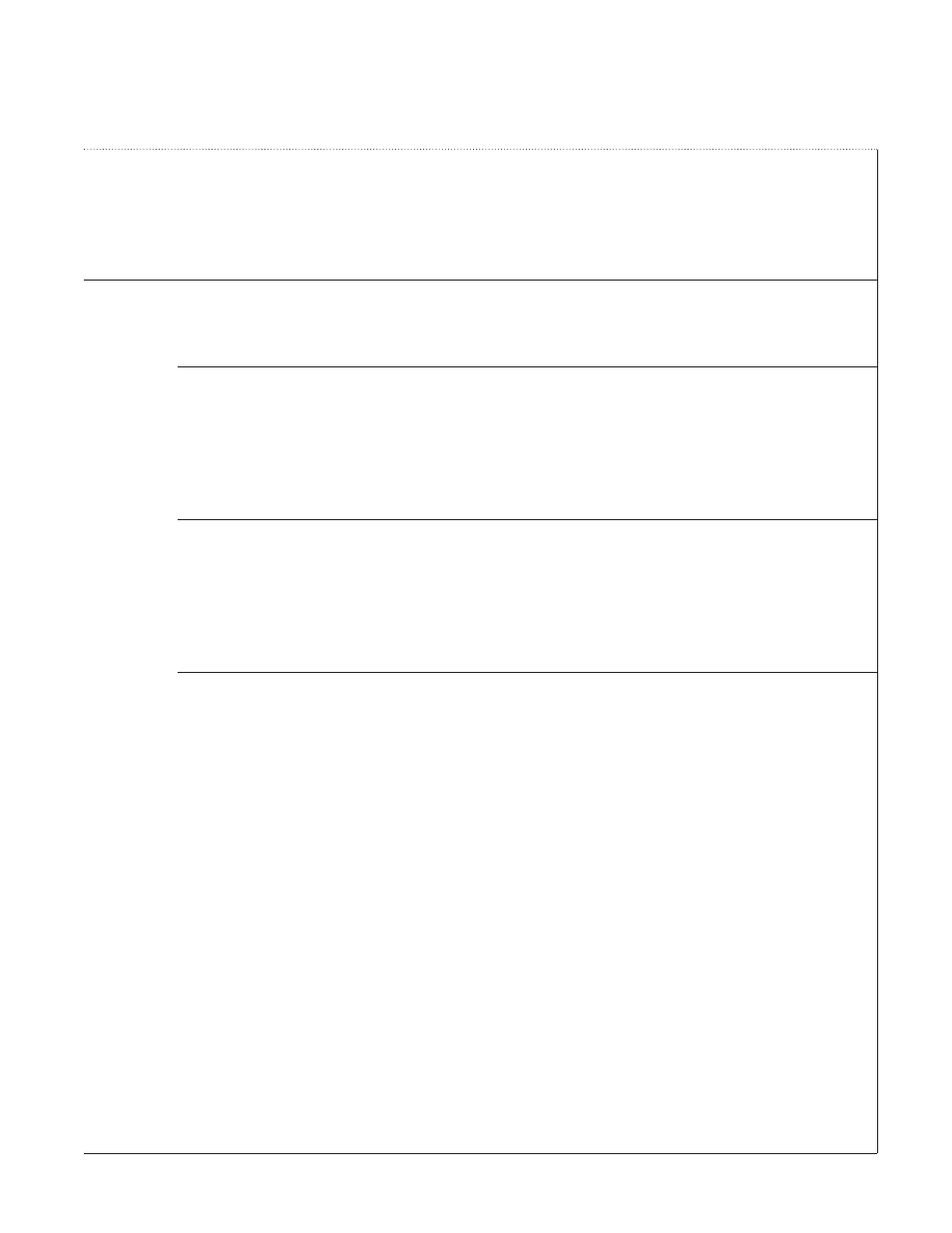
Decorative Materials
For a unique look, you can add other products to the slurry after the water and powder have been blended.
Obviously, some of these additions will prevent spraying, and every additive will reduce the strength of the
gypsum cement, depending how much is used. Therefore, use additives cautiously.
Colors or Stains
For a special effect, water-dispersible dyes or pigments can be added to the slurry. First disperse materials in
water using a high speed mixer, and then replace a portion of the mixing water with the pigment dispersion.
Putting the dye or pigment directly into the slurry will produce streaking or splotches of color.
Internal colorants are not a substitute for surface-applied coatings because the color will not be uniform in all
areas. Because the color is water-dispersible, the areas that dry first will be darker in color. This effect can work
where an antique coat or a wash coat is used as the final surface.
Sand or Other
To give the surface a texture to convey a stone-like look, add the material to the slurry of water and powder when
Fine Aggregates
the two are mixed. Use no more than 10%-15% of the total weight of powder and water. Using H
YDROCAL
FGR at 30
consistency as an example, a range of 13 to 19 lbs. of aggregate per mix (30 lbs. of water and 100 lbs. of powder)
would fall into the 10%-15% range. If the sand choice makes the slurry too thick in this weight range, reduce the
quantity of sand. Adding aggregate will reduce strength; adding aggregate plus additional water will reduce
strength even more. Unlike cements, there is no bond between the set gypsum and the aggregate.
Perlite, Beads, or
Difficult to use, these products are the most likely to result in dangerously low strength safety margins because
Other Weight
they require more water in the slurry. Thus, there is a two-fold strength reduction — first from the addition of the
Reduction Materials
material, and second from the extra water added to the slurry.
There are many different choices of materials and since each will have a different impact on the amount of
water required, there is no general rule for the acceptable quantity. Each raw material has different advantages as
well as disadvantages, so usage must be carefully analyzed.
However, there are some general points:
1. Most weight-reduction materials will float, so there is danger of an excessive amount in some areas producing
planes of weakness.
2. Large-diameter products affect the strength to a greater degree because the voids of low strength are larger.
3. Purchase porous particles like perlite in a treated state, or they will absorb tremendous amounts of water which
will reduce strength and impede drying.
4. The best choices for reducing weight (but also the most expensive) are man-made products like ceramic beads
or glass beads. These materials do not absorb water and are available in narrow particle size ranges. As with all
additives used in large quantities, it is best to evaluate their impact on your product performance before going to
market. It is possible to check strengths of formulas with these additives through local test labs for reasonable
costs. Contact your USG representative for assistance.
25
Casting Fireplace Surrounds