Manufacturing – USG Casting Fireplace Surrounds User Manual
Page 15
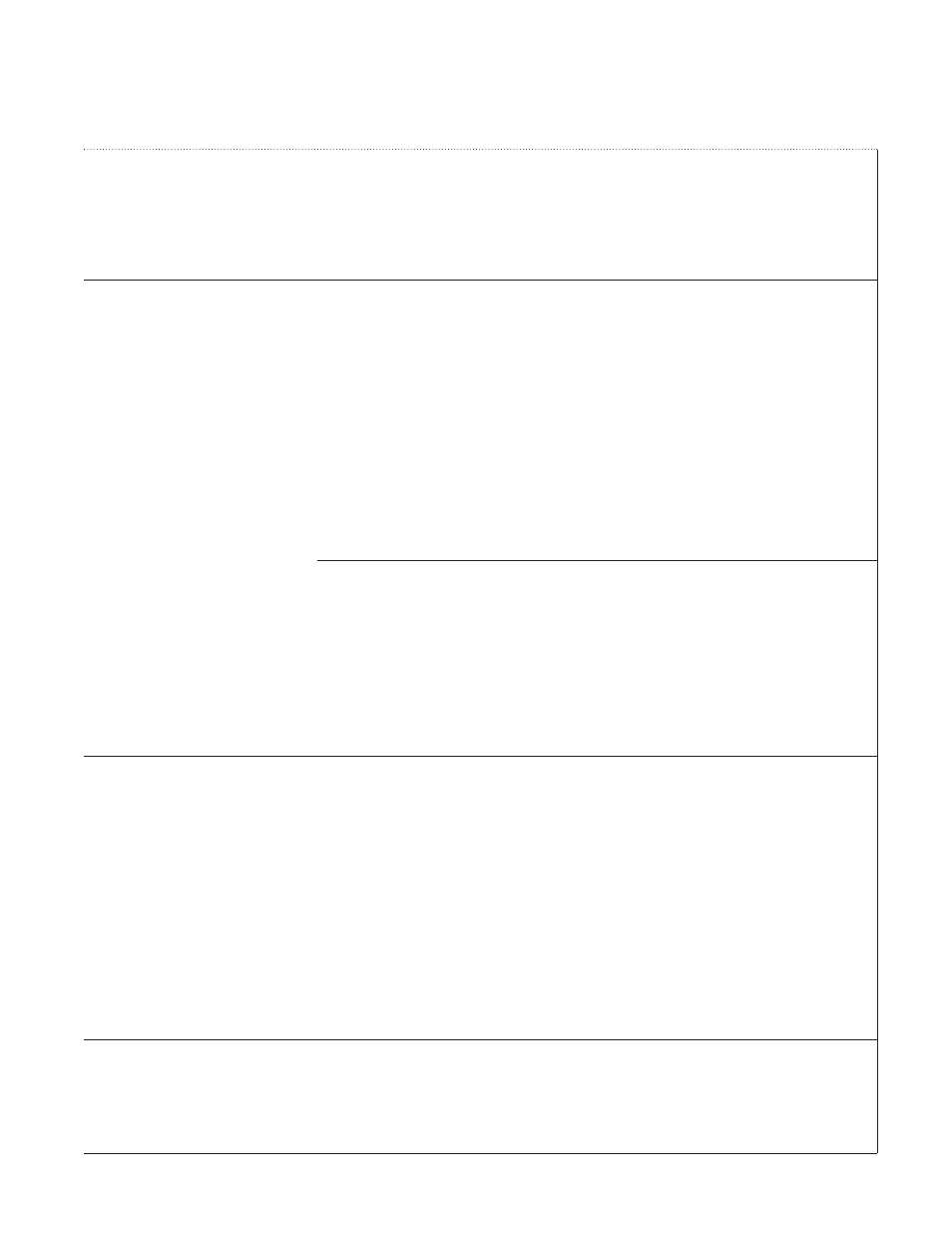
There are basically three ways to manufacture fireplace ornamenta-
tion: hand-layup, spraying or solid-casting. The best process to
use depends on many factors. It may seem that the more automated
process is better and more efficient, but product design, number
of pieces per finished unit, and the required level of production are
also factors. It is always good to do some development work by hand
until the manufacturing issues have been resolved. If the target
market is low-end with high production, it is especially important
to understand the manufacturing needs of a high-production shop.
Fireplace surrounds can be fabricated in one piece, three pieces, or many pieces. Your decision on the number of
parts in the finished unit will affect the fabrication method and the arrangement of your casting area, packaging,
shipping, and installation.
The initial design and manufacture should use the hand-layup process to make the fireplace surround parts.
We do not recommend an immediate investment in spray equipment, because the choice of spray equipment
should wait until other manufacturing details are ironed out. Some designs lend themselves to spraying and
some do not, so in the first phase of business development ensure that the spray system will actually produce
the appropriate quantity and quality of products.
Hand-layup
This process uses layers of glass fiber mat that have been impregnated with the gypsum slurry. Initially, a coat of
gypsum slurry is applied to the mold face to ensure there is no air entrainment, and when this coat has stiffened but
not set, a coat of gypsum slurry and a layer of glass fiber mat are applied behind the first coat. Additional layers of
mat saturated with slurry are added until the proper thickness is achieved (at least 3/8”). After each glass coat is
applied, it is important to compact the glass and slurry before the next layer is added. Use a small roller or your
hands (protected by thin rubber gloves). Good compaction will impregnate all of the fiber with the slurry and keep
any air voids from occurring, resulting in good strength development and a high quality part. The proper ratio of
glass to slurry is 5% - 6% glass by weight of the total weight of the slurry. For example, to determine 5% fiber using
H
YDROCAL
FGR at 30 consistency (30 parts water to 100 parts H
YDROCAL
FGR), you would take 30 + 100 = 130 lbs.
of mix, multiplied by .05 = 6.5 lbs. of fiber. Hand-layup is usually done with H
YDROCAL
FGR or E
NDURACAST
gypsum
cements that have been formulated to provide sufficient working time to carry out the process. One of the most
common problems with this method is to use too little gypsum cement, and as a result “starve” the glass.
Spraying
This usually consists of a mixer, a pump, a spray head and the support systems that help the equipment function
properly. With this method, the slurry is sprayed into the mold at the same time as the glass is being chopped
into the slurry spray. As with hand-layup, the first coat on the mold contains no glass so there will be complete
capturing of the detail in the mold. Also, it is important to compact the glass with a roller or by hand to ensure
that all of the slurry has impregnated the glass. The spraying and compacting proceeds until the proper thickness
Manufacturing
15
Casting Fireplace Surrounds