USG Casting Fireplace Surrounds User Manual
Page 21
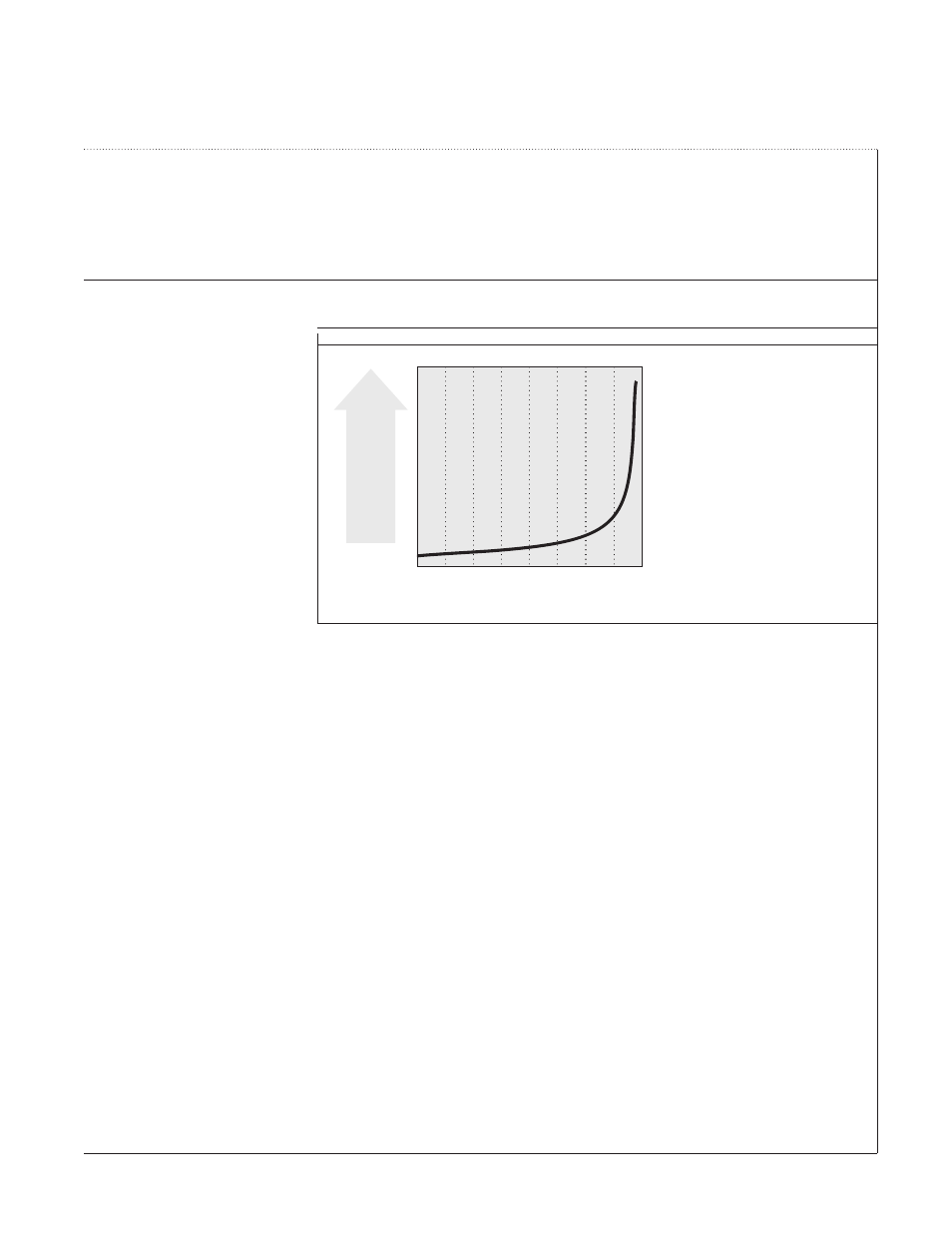
The chart below shows the importance of fully drying the parts.
Fully Drying Parts Increases Compressive Strength
The compressive strength of the finished part increases only slightly until 93% of the free water has been
removed. Strength then increases dramatically as the remaining water is removed.
Controlled drying conditions are best. Drying equipment can be designed to remove the excess water in a specified
time. A forced-air dryer with controlled humidity is the quickest and best way to dry the part, and will yield the best
results. Rarely will gypsum cement castings become 100% dry without the use of a forced-air dryer.
When a newly made wet part is placed in the dryer, rapid evaporation of the free water begins. The initial
evaporation keeps the part cooler than the temperature in the dryer. Water from the interior of the casting will
move to the outside surface to replace evaporating moisture. As evaporation continues, sufficient water does
not move to the surface of the part to keep it cool and the surface temperature will rise although the center of
the part is still moist.
When the part’s surface temperature reaches that of the dryer air, the remaining free water comes to the sur-
face slowly and evaporates. As this occurs, the temperature of the part increases throughout. When the center of
the part reaches the temperature of the dryer air, drying is complete. One way to know if the part is completely dry
is to weigh the part at intervals during the drying process. When the part does not lose weight after it is weighed at
least three times, it is considered dry.
Recommended maximum dryer temperature for most gypsum cements is 110° to 120° F. Higher temperatures
(130° – 140° F) may be used initially, but must be reduced during the drying process as water is removed from
the part. Extended high temperatures may calcine, or overheat, the surface. Humidity controls in the dryer can
facilitate a quicker drying process. It is important to size the dryer so it matches your production plans.
Make sure you do not allow your parts to undergo “thermal shock.” It is best to gradually raise and lower tem-
peratures in the dryer to avoid cracking from quick changes in temperature. For more information on drying, see
USG publication IG502, Drying Plaster Casts.
21
Casting Fireplace Surrounds
Percent Excess Water Evaporated
Compressive
Strength-PSI
0
100
75
50
25