6 data transfer, Data transfer – Lenze E84DxxxxxxxxxR User Manual
Page 30
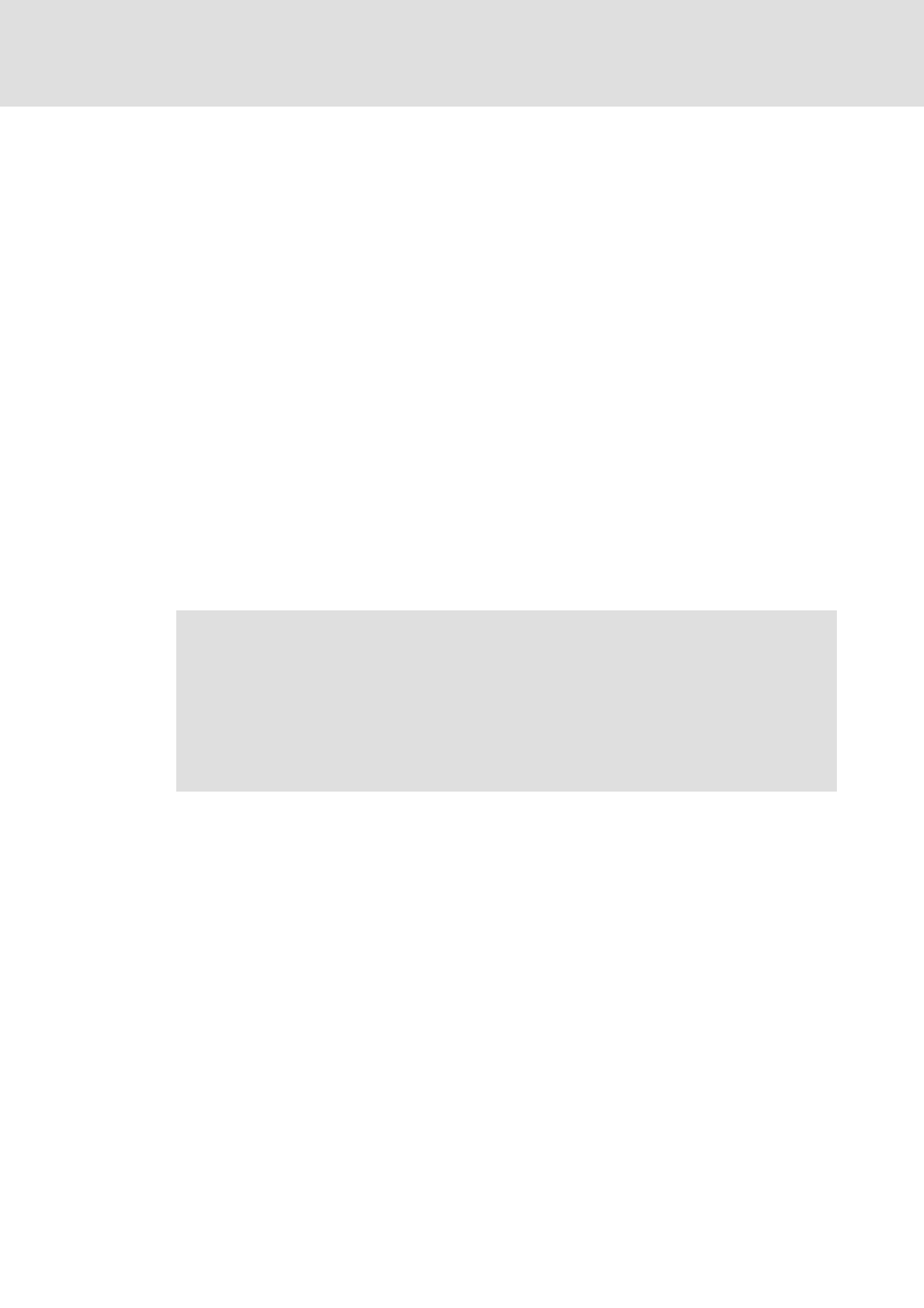
Communication manual 8400 protec PROFINET
Data transfer
30
L
EDS84DPNET EN 4.0 - 11/2010
6
Data transfer
PROFINET transmits parameter data, configuration data, diagnostic data, alarm messages,
and process data between the host system (IO controller) and the controllers participating
in the fieldbus (IO devices). Depending on their time-critical behaviour, the data are
transmitted via corresponding communication channels.
Communication channels
The process data channel transmits process data.
– With the process data the controller is actuated.
– The transmission of process data is time-critical.
– Process data are transmitted cyclically between the IO controller and the IO devices
that are part of the fieldbus according to the provider/consumer model (continuous
exchange of current input and output data).
– The IO controller can directly access the process data. In the PLC, for instance, the
data are directly assigned to the IO area.
– In the case of Inverter Drives 8400 protec, maximally 16 process data words (16 bits/
word) can be exchanged for each direction.
– Process data are not stored in the Inverter Drive 8400 protec.
– Process data are e.g. setpoints, actual values, control and status words.
Parameter data are transmitted via the acyclic channel.
– Usually the transmission of parameter data is not time-critical.
– Access to the parameter data depends on the PROFIdrive profile.
– Examples of parameter data are operating parameters, motor data, and diagnostic
information.
– The acyclic channel provides access to all Lenze codes.
– Parameter changes must be saved via code C00002 of the Inverter Drives 8400
protec.
Note!
Please observe the direction of the flow of information!
• Process input data (Rx data):
– Process data from the drive controller (IO device) to the IO controller
• Process output data (Tx data):
– Process data from the IO controller to the drive controller (IO device)