3 operating modes, 4 connections and i/o, 5 digital i/o ratings – Lenze S94P01B2 User Manual
Page 10: Technical data 2.3 operating modes
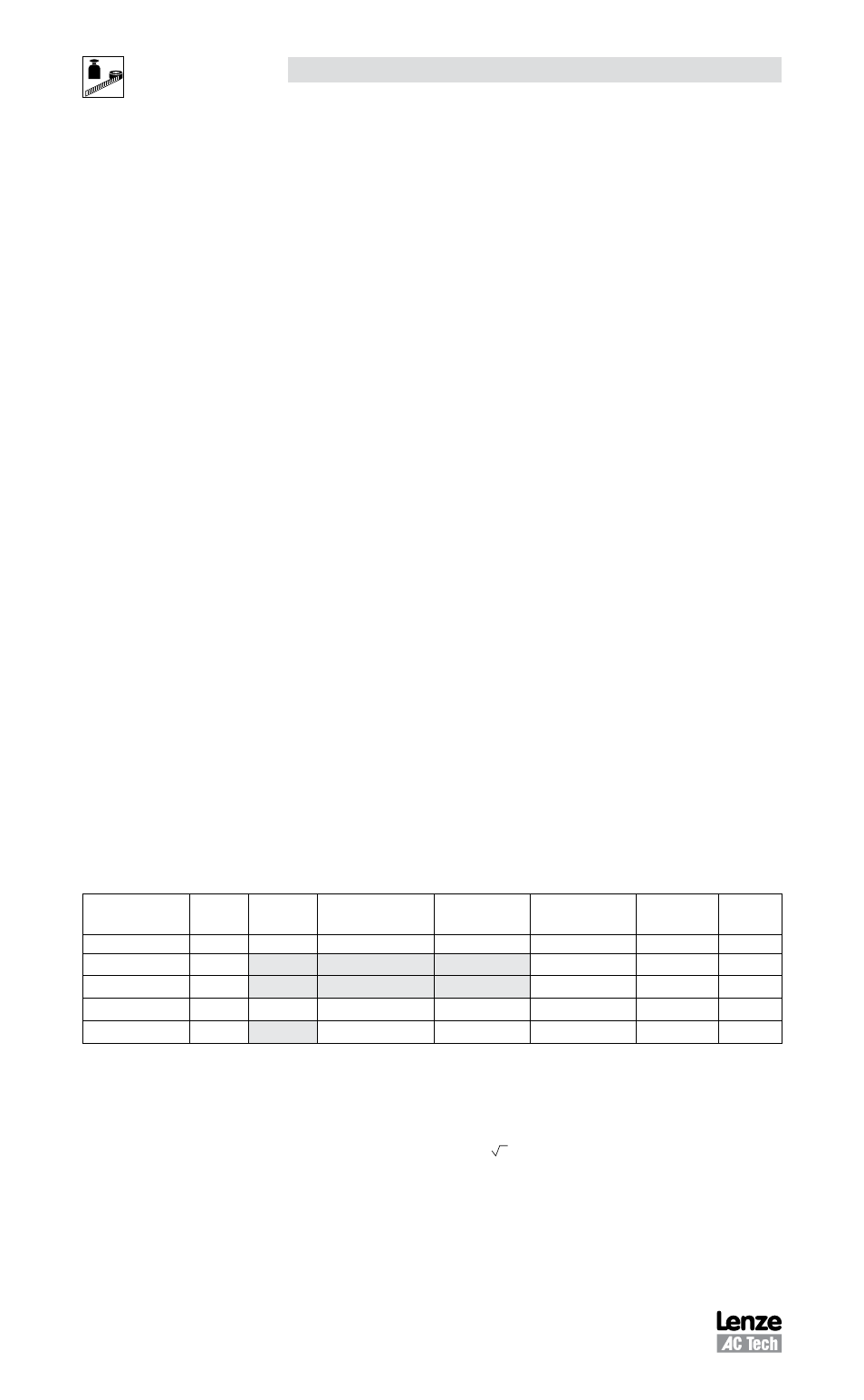
S94P01B2
8
Technical Data
2.3
Operating Modes
Torque
Reference
± 10 VDC 16-bit; scalable
Torque Range
100:1
Current-Loop Bandwidth Up to 1.5 kHz*
Velocity
Reference
± 10 VDC or 0…10 VDC; scalable
Regulation
± 1 RPM
Velocity-Loop Bandwidth Up to 200 Hz*
Speed Range
5000:1 with 5000 ppr encoder
Position
Reference
0…2 MHz Step and Direction or
2 channels quadrature input; scalable
Minimum Pulse Width
500 nanoseconds
Loop Bandwidth
Up to 200 Hz*
Accuracy
±1 encoder count
* = motor and application dependent
2.4
Connections and I/O
Mains Power
4-pin removable terminal block
(P1)
RS232 Port
Standard 9-pin D-shell (DCE) Connector
(P2)
I/O Connector
Standard 50-pin SCSI.
(P3)
- Buffered Encoder Output
A, B & Z channels with compliments (5V @ 20mA)
(P3)
- Digital Inputs
12 programmable, 1 dedicated (5-24V)
(P3)
- Digital Outputs
4 programmable, 1 dedicated(5-24V @ 15mA)
(P3)
- Analog Input
1 differential; ±10 VDC (16 bit)
(P3)
- Analog Output
1 single ended; ±10 VDC (10-bit)
(P3)
Encoder Feedback (primary)
Standard 15-pin D-shell
(P4)
24VDC Power “Keep Alive”
2-pin removable terminal block
(P5)
Regen and Bus Power
5-pin removable terminal block
(P6)
Motor Power
6-pin pin removable terminal block
(P7)
Resolver feedback (option bay)
Option module with standard 9-pin D-shell
(P11)
Encoder Feedback (option bay)
Option module with standard 9-pin D-shell
(P12)
Comm Option Bay
Optional Comm Modules (CAN, Ethernet, RS485)
(P21)
Windows® Software:
MotionView (Windows 98, NT, 2000, XP)
2.5
Digital I/O Ratings
Scan
Times
Linearity
Temperature Drift
Offset
Current
Input
Impedance
Voltage
Range
Units
ms
%
%
%
mA
Ohm
VDC
Digital Inputs
(1)
512
Depend on load
2.2 k
5-24
Digital Outputs
512
15 max
N/A
30 max
Analog Inputs
512
± 0.013
0.1% per °C rise
± 0 adjustable
Depend on load
47 k
± 18
Analog Outputs
512
0.1% per °C rise
± 0 adjustable
10 max
N/A
± 10
(1) Inputs do not have scan time. Their values are read directly by indexer program statement.
Notes for Power Ratings Table in section 2.6:
(1) At 240 VAC line input for drives with suffixes “S1N”, “S2F”, “Y2N”. At 480 VAC line input for drives with suffixes “T4N”.
a. The output power is calculated from the formula: output kVA = [(
3
) x U
LL
x I
rated
] /1000
b. The actual output power (kW) depends on the motor in use due to variations in motor rated voltage, rated speed and
power factor, as well as actual max operating speed and desired overload capacity.
c. Typical max continuous power (kW) for PM servo motors runs 50-70% of the kVA ratings listed.
(2) At 16 kHz, de-rate continuous current by 17%
(3) Leakage Current is typically >3.5mA. Contact factory for applications requiring <3.5mA