4 the lenze automation system with profibus, 1 brief description of profibus, The lenze automation system with profibus – Lenze PROFIBUS Controller-based Automation User Manual
Page 14: Brief description of profibus, 4the lenze automation system with profibus
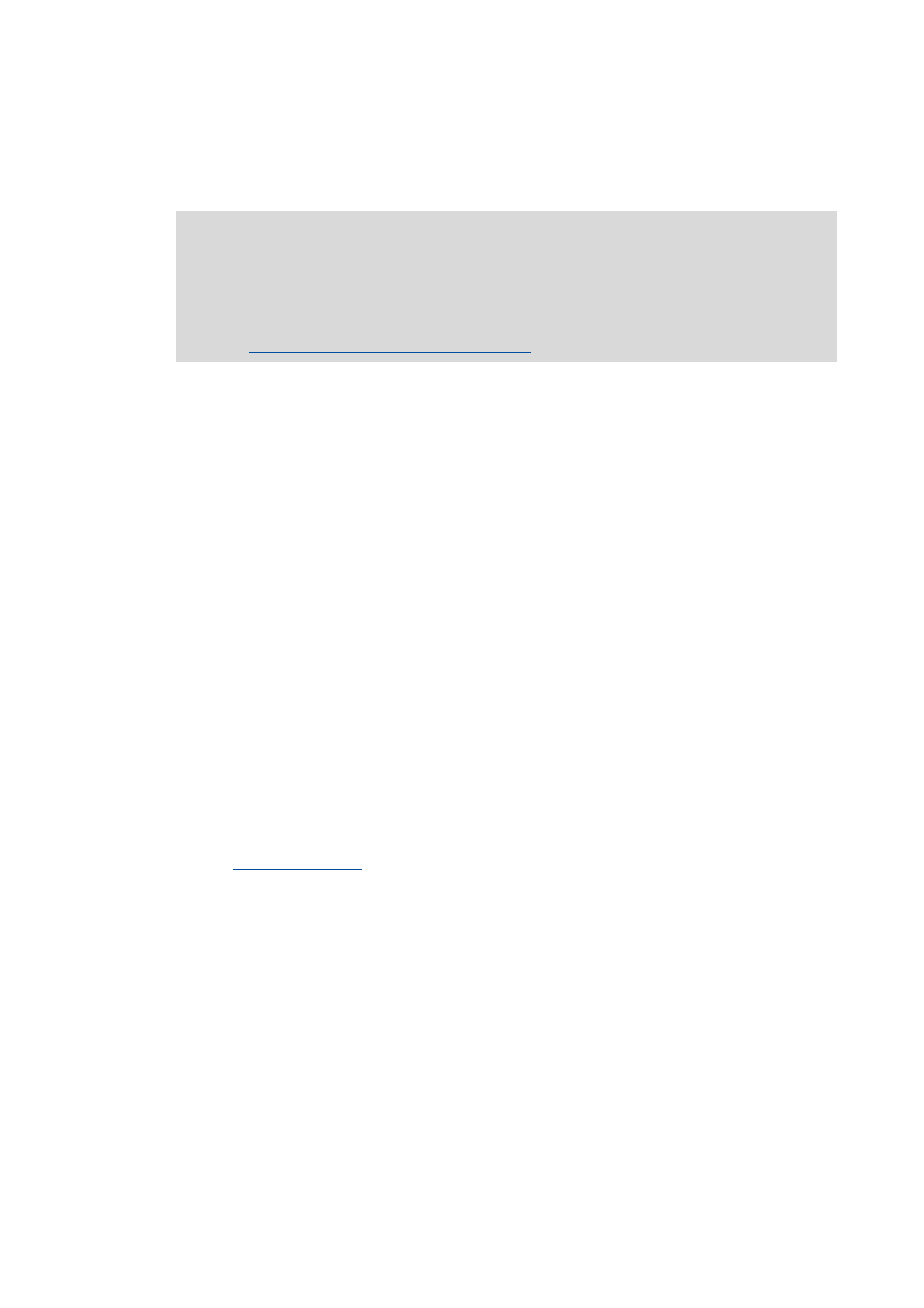
4
The Lenze automation system with PROFIBUS
4.1
Brief description of PROFIBUS
14
Lenze · Controller-based Automation · PROFIBUS® Communication Manual · DMS 4.3 EN · 04/2014 · TD17
_ _ _ _ _ _ _ _ _ _ _ _ _ _ _ _ _ _ _ _ _ _ _ _ _ _ _ _ _ _ _ _ _ _ _ _ _ _ _ _ _ _ _ _ _ _ _ _ _ _ _ _ _ _ _ _ _ _ _ _ _ _ _ _
4
The Lenze automation system with PROFIBUS
This chapter provides basic information about ...
• the structure of the Lenze automation system using the PROFIBUS bus system;
• the Lenze Engineering tools required for commissioning;
• the interaction of the components.
4.1
Brief description of PROFIBUS
Today, PROFIBUS is the most commonly used fieldbus system. As it comes with the widest range of
various field devices, PROFIBUS is occasionally prioritised over more modern bus systems. Due to the
low bandwidth and synchronisation mechanisms, PROFIBUS is only provided as a logic bus as part
of the Lenze automation system.
We recommend using PROFIBUS for the following applications:
• Equipment and extension of system parts that have already been automated with PROFIBUS
before.
• Use of field devices that are not available for e.g. EtherCAT or CANopen.
• Combination of PROFIBUS as logic bus and EtherCAT as logic/motion bus
Tip!
Detailed information about PROFIBUS can be found on the website of the PROFIBUS &
PROFINET user organisation:
Note!
In the Lenze automation system PROFIBUS is exclusively used as Logic bus.
The Motion functionality is not supported when PROFIBUS is used. Always use EtherCAT
to connect inverters to be controlled via the central motion functionality.