Lubrication maintenance, Storage, Figure 4-11: rear jack storage position – Landoll 2111 Coulter Chisel User Manual
Page 80
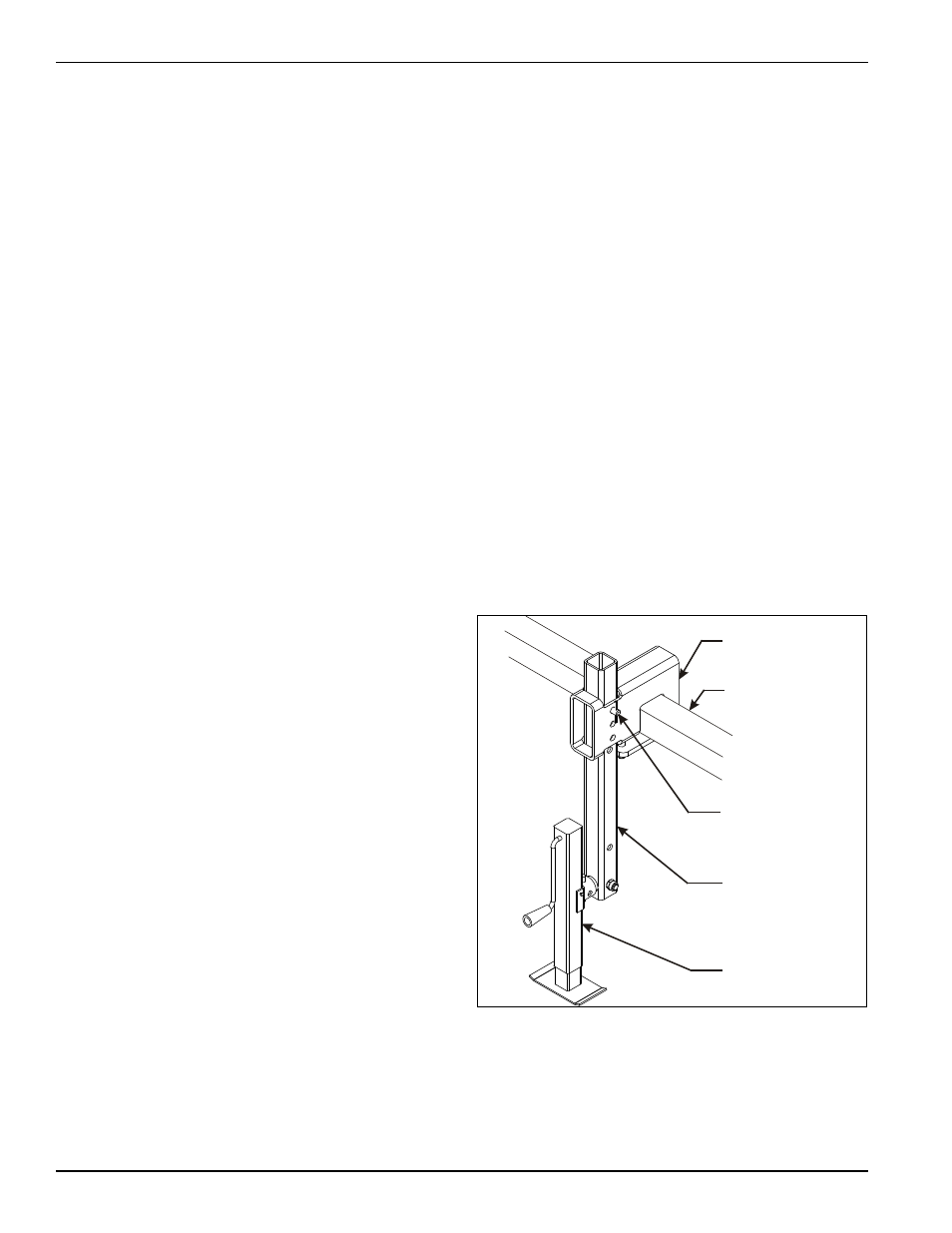
4-12
F-719-0413 Edition
OPERATION AND MAINTENANCE
Lubrication Maintenance
1.
Table 4-1 specifies the lubrication points and
intervals on the 2111 Coulter Chisel. Proper
maintenance of your machine will, under normal
operating conditions, help to keep it operating at or
near its peak performance for an extended period of
time. Proper maintenance is also a condition of
keeping your warranty in good status (See
Figure 4-10.)
2.
When lubricating the Coulter Chisel, SAE
multi-purpose EP grease, or EP grease with 3-5%
molybdenum sulfide is recommended. Wipe soil from
fittings before greasing. Replace any lost or broken
fittings immediately.
3.
Disc gang bearings are equipped with triple-lip seals
that will let grease pass and not harm the seal.
Regular lubrication will maintain a full grease cavity
and help purge any contaminants. Grease the
bearings before long periods of storage to prevent
moisture buildup within the bearing cavity.
4.
Wheel seals and walking tandem seals, when
properly installed, will allow grease to pass without
harm to seals. Regular lubrication will extend service
life, particularly in severe operating conditions.
5.
The Coulter Chisel is equipped with
maintenance-free bearings in the lifts and leveler.
These areas require no lubrication.
Storage
1.
The service life of the Coulter Chisel will be extended
by proper off-season storage practices. Prior to
storing the unit, complete the following procedures:
a.
Completely clean the unit.
b.
Inspect the machine for worn or defective parts.
Replace as needed.
c.
Repaint all areas where the original paint is worn
off.
d.
Grease all exposed metal surfaces of shanks,
points and coulters.
e.
Apply a light coating of oil or grease to exposed
cylinder rods to prevent them from rusting.
f.
Lubricate each point of the machine as stated in
“Lubrication Maintenance” on page 4-12.
2.
Store the unit in a shed or under a tarpaulin to protect
it from the weather. The ground tools and tires should
rest on boards, or some other object, to keep them
out of the soil.
3.
Slide the rear jack tube from transport position and
into slot from bottom of rear jack mount. Pin jack tube
in position. Attach jack to rear jack tube and pin in
position. Crank jack until the rear of the machine is
supported (See Figure 4-11.)
Figure 4-11: Rear Jack Storage Position
REAR JACK
MOUNT
LOCK PIN
AND 1/4 X 3
ROLL PIN
REAR JACK
SQUARE TUBE
JACK
REAR FRAME