Density, Tooling factor, Acoustic impedance – INFICON Maxtek PM-700 Plating Monitor User Manual
Page 78
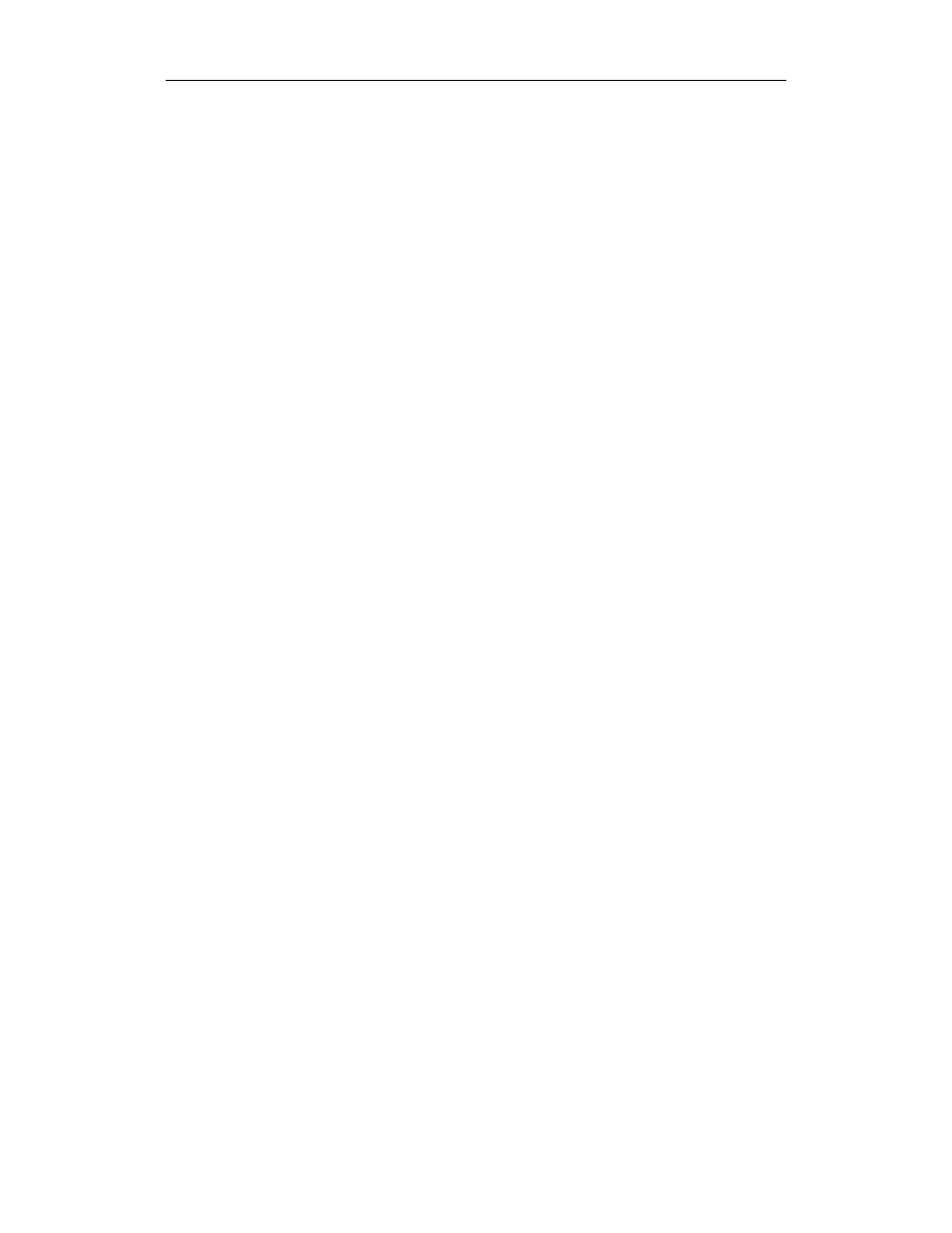
PM-700 SERIES PLATING MONITOR
70
To calibrate the monitor; material density, tooling factor and acoustic impedance
must be established in that order. Approximate values should be used initially.
Table 21 on page 72 provides density of some materials which should provide
guidance as to the approximate density. If the acoustic impedance is unknown,
use the value of quartz 8.83.
6.2.1 Density
This Material Density is probably available from your chemical supplier. If not,
follow the procedure below to establish the density.
1. Use a fresh sensor crystal.
2. Place test substrates as close as possible to the sensor crystal.
3. Make a trial deposition of sufficient thickness to permit adequate precision of
measurement by an out-of-bath thickness measuring device.
4. Determine the average thickness on the test substrate.
5. If the displayed thickness is lower than the actual measured thickness,
decrease the Density value. The displayed thickness will start increasing.
Stop when the displayed thickness equals the actual measured thickness.
Inversely, if the displayed thickness is higher than the measured thickness,
increase the Density value until the displayed thickness agrees with the
measured thickness.
The programmed material density will now be correct for that particular material.
Record this value for future use.
6.2.2 Tooling
Factor
1. Use a fresh sensor crystal.
2. Place a test substrate in a location which is representative of where the
production substrate will be located.
3. Make a trial deposition with the material density as determined above.
4. Determine the average thickness on the test substrate with a thickness
measuring device.
5. If the actual measured thickness is lower than the displayed thickness, increase
the Tooling Factor value. This will bring the displayed thickness up. Stop
when the displayed thickness equals the measured thickness. If the measured
thickness is higher than the displayed thickness, decrease Tooling Factor until
the displayed thickness agrees with the actual measured thickness.
The Tooling Factor should now be correct for the specific application measured.
6.2.3 Acoustic
Impedance
1. Use a heavily loaded sensor crystal with a crystal health of about 75%.
2. Plate on the sensor crystal until the crystal health approaches 50%.