Det-Tronics UD10 FlexVu Explosion-Proof Universal Display Unit User Manual
Page 9
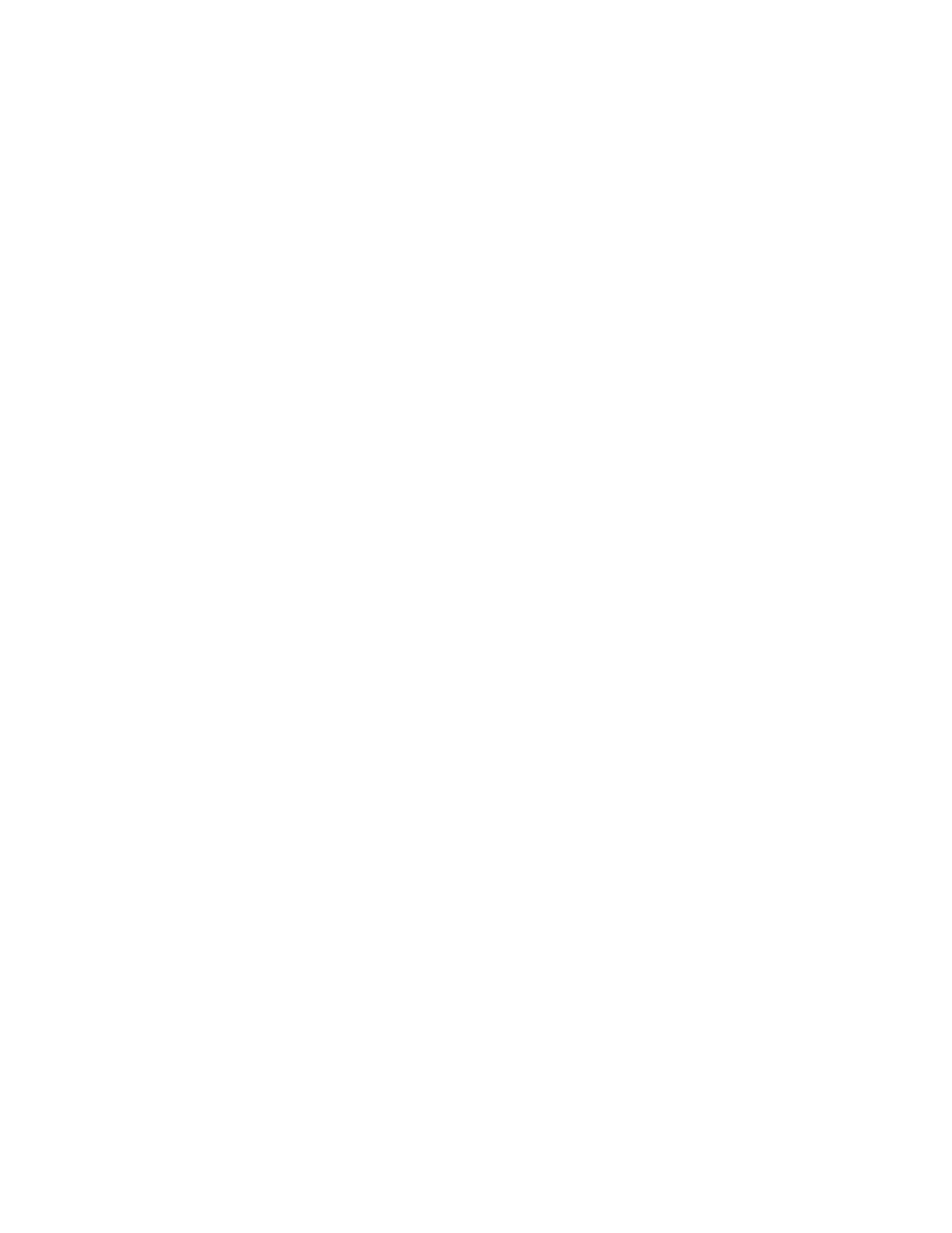
7
95-8661
4.2
WirinG
pOwER SUpply REQUIREmENTS
Calculate the total gas detection system power
consumption rate in watts from cold start-up. Select a
power supply with adequate capability for the calculated
load. Ensure that the selected power supply provides
regulated and filtered 24 Vdc output power for the entire
system. If a back-up power system is required, a float-type
battery charging system is recommended. If an existing
source of 24 Vdc power is being utilized, verify that system
requirements are met. The acceptable voltage range is
18-30 Vdc measured at the input to the UD10.
noTe
The power supply must meet the noise requirements
for HART systems. If noise or ripple on the main
power source could interfere with the HART
function, an isolated power source (Figure 11) is
recommended. (For detailed information regarding
power supply specifications, refer to the HART
Communication Foundation’s document “FSK
Physical Layer Specification” HCF_SPeC-54.)
wIRINg CABlE REQUIREmENTS
Always use proper cabling type and diameter for input
power as well as output signal wiring. 14 to 18 AWG
shielded stranded copper wire is recommended. Correct
wire size depends on the device and wire length. Refer
to the appropriate Appendix for additional information.
The maximum cable length from power source to UD10 is
2000 feet. Maximum cable length from UD10 to sensor
is 2000 feet.
noTe
The use of shielded cable in conduit or shielded
armored cable is highly recommended. In
applications where the wiring is installed in
conduit, dedicated conduit is recommended.
Avoid low frequency, high voltage, and
non-signaling conductors to prevent nuisance
eMI problems.
CautIon
The use of proper conduit installation techniques,
breathers, glands, and seals is required to prevent
water ingress and/or maintain the explosion-proof
rating.
SHIElD CONNECTIONS
The UD10 provides terminals for proper grounding of
wiring cable shields (located on the sensor, 4-20 mA,
and operating power terminal blocks). These shield
terminals are not connected internally, but are connected
to ground through capacitors. The capacitors ensure an
RF ground, while preventing 50/60 Hz ground loops.
Ground all shields as shown in the wiring examples
throughout this manual.
Important
For proper grounding, all junction boxes / metal
enclosures must be connected to earth ground.
The following are required for installations requiring CE
Mark compliance:
• For shielded cable installed in conduit, attach the wire
shields to the “shield” connections on the terminal
blocks, or to earth ground on the case.
• For installations without conduit, use double shielded
cable. Terminate the outer shield to earth ground on
the case. Terminate the inner shield to the “shield”
connection on the terminal blocks.
JUmpER SETTINg FOR 4-20 mA lOOp
In order for the 4-20 mA current loop to operate properly,
+24 Vdc must be applied to terminal P1-3. This can be
accomplished in one of two ways:
• For a non-isolated 4-20 mA loop, set jumper plug as
shown in Figure 4. This applies +24 Vdc to P1-3 via an
internal connection to terminals P2-2 and P2-5.
• If the 4-20 mA loop will receive power from a source
other than the UD10’s main power source (isolated),
set the jumper plug as shown in Figure 5 to remove
the internal connection.
FOUNDATION FIElDBUS (Optional)
Some UD10 models allow the use of either RS485/
MODBUS or Foundation Fieldbus communication via
connection to J2 on the terminal board. Four jumpers
are provided to select between the two protocols. If the
device is equipped for Foundation Fieldbus, it will be
shipped from the factory with the jumpers preset for that
mode. If the user wants to switch to RS485/MODBUS
(for example, to retrieve logs), the four jumpers can
easily be moved. Figures 6 and 7 show the jumper
settings for each mode of communication.
Note that the pin identification for the J2 connector
is different for each communication protocol. For
Foundation Fieldbus it is “– +”. For RS485/MODBUS
it is “B A com”.