Brake lathes, Brake lathe operation – AMMCO 700 Vehicle Brake Lathe User Manual
Page 9
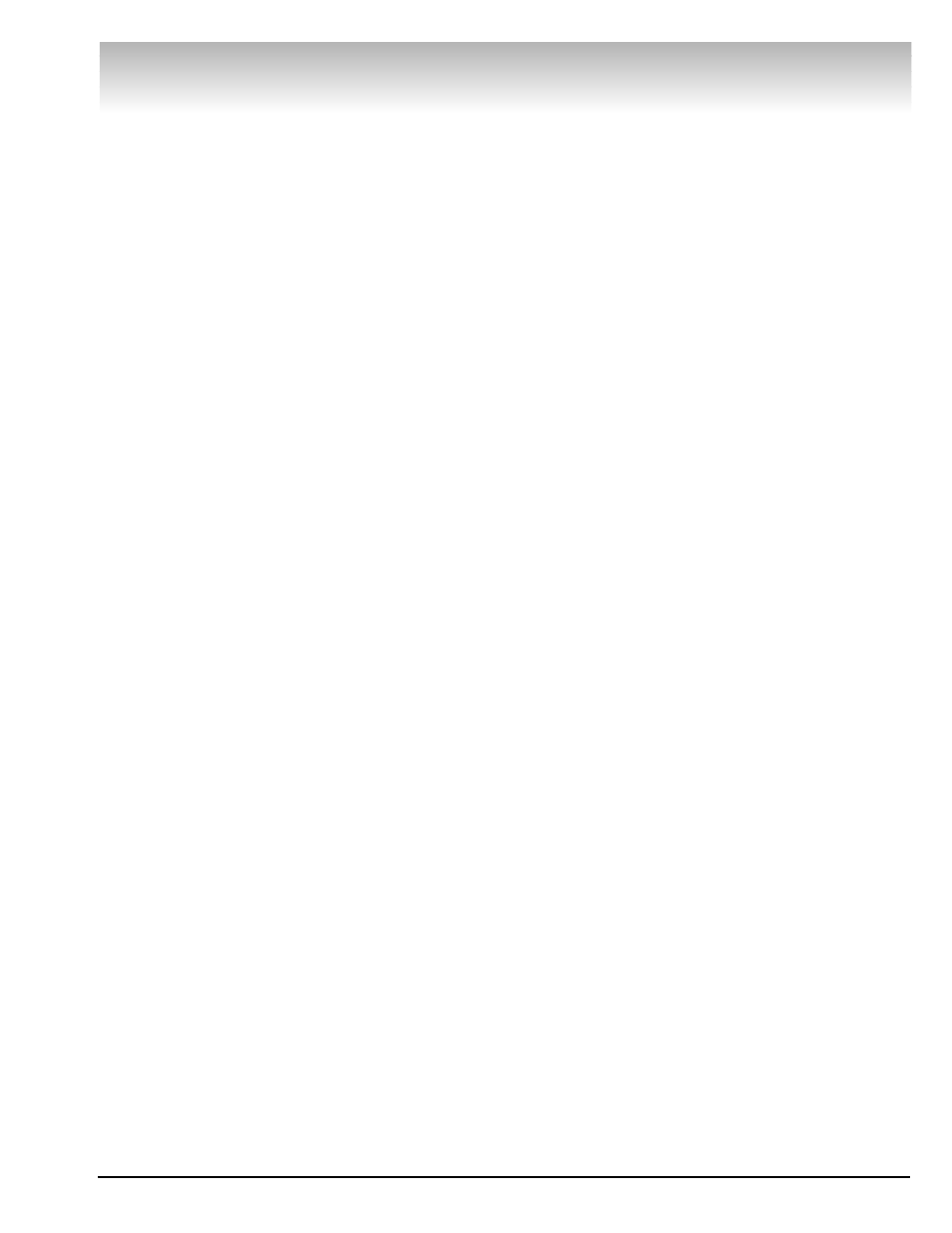
AMMCO 700/705/710 Brake Lathes • 3
Brake Lathe Operation
To completely understand rotor turning with this
lathe, you must have a knowledge of the lathe itself.
When the lathe is plugged into a power source the car-
riage feed motor is on. When the feed engagement
knob is loose, the carriage will move through its full
travel with a few turns of the handwheel. When the
feed engagement knob is tightened, the carriage will
travel in an outward direction until the knob is loos-
ened, or the carriage reaches the end of travel. The limit
switch will turn the feed motor off when maximum
travel is reached.
Note: The carriage handwheel cannot be hand
adjusted while the engagement knob is tight.
Both faces of the rotor will be reconditioned at the
same time, the depth-of-cut on each side is determined
by each side’s dial micrometer. The lathe assembly has
a pair of serf-centering mounting brackets. These can
be adjusted to fit the bolt pattern of the caliper mount-
ing bracket on the majority of today’s vehicles. This
insures that the cutting bits will be in the proper loca-
tion for reconditioning of the rotor.
The mounting hardware containing various bolts,
spacers, washers, and nut plates, will allow for the
mounting of the lathe to most vehicles without the
need to purchase extra hardware.
Reconditioning Disc Brake Rotors
Each brake rotor should be carefully inspected for
SCORING and RUST RIDGES (at the inner and outer
circumference of the rotor). Any excessive wear or
deformity should be noted and, if not within acceptable
limits, the rotor should be replaced.
Use a micrometer to check the thickness of the rotor
at no less than three points around the circumference
about 1" (2.54 cm) in from the outer diameter. If the
thickness is less than the minimum established by the
car manufacturer (or if it will be less after recondition-
ing), the rotor should be replaced.
Note: Most often the discard thickness dimension is
cast into the rotor, not the minimum “machine to”
thickness.
Depth-Of-Cut Micrometer Dials
The depth-of-cut micrometer dials are calibrated with
both inch and metric scales. The depth-of-cut dial indi-
cates the amount of material to be cut from its side of
the rotor.
Inch Scale - A cut of .002" (one micrometer division)
on each dial from a 1" thick rotor will result in a refin-
ished rotor of .996" thick.
Metric Scale - A cut of .05 mm (one micrometer divi-
sion) on each dial from a 25.4 mm thick rotor will result
in a refinished rotor of 25.3 mm thick.
Vehicle Preparation
1. Remove the caliper to provide a secure place of
attachment for the lathe. The caliper should be sup-
ported with a wire hook to prevent strain on the flexi-
ble brake hose. Position the hook as to place the caliper
in an out-of-the-way position to avoid damage.
Note: If the rotor to be machined is connected, by the
drive train, to the wheel on the opposite side of the
vehicle, both wheels must be removed.
2. If the constant-velocity-joint boot is missing or
damaged, replace before machining rotor.
3. Secure the rotor to the hub using the Rotor Driving
Unit lug adapter as described in the section MOUNT-
ING OF LUG ADAPTER.
4. If required, rotate the steering wheel to allow
clearance for the lathe between the steering knuckle
and fender well, Fig. 1.
Note: On some rear rotor applications the shock,
sway bar, and connecting arms may need to be discon-
nected in order to gain more room by allowing the axle
to drop down.
Brake Lathes