7 engine oil pressure sender, 8 fuel level sender, Engine oil pressure sender – JLG 4017 Service Manual User Manual
Page 143: Fuel level sender
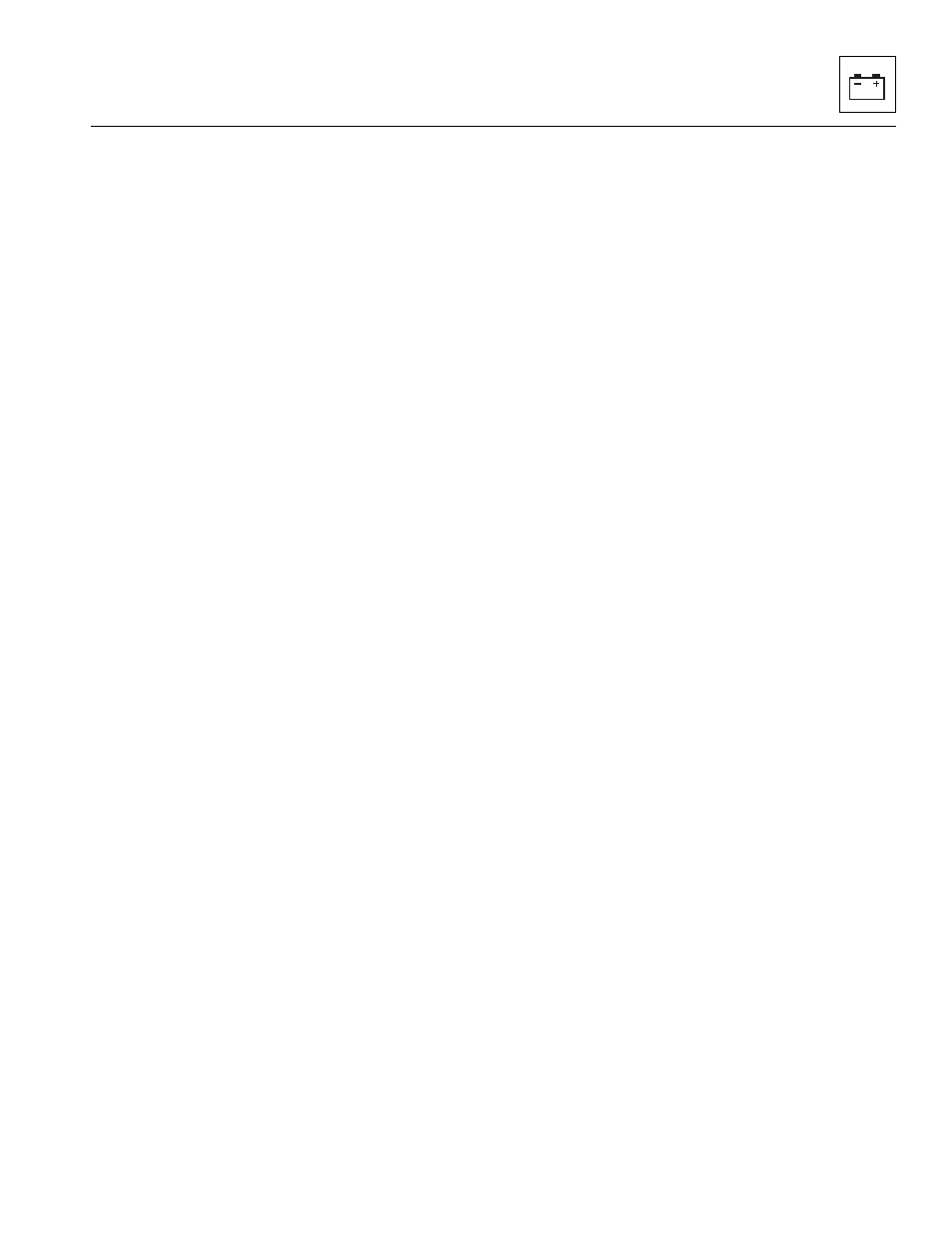
9.23
4017
Electrical System
4. Start the engine, allow it to reach operating
temperature and observe the operator’s instrument
cluster for warning indication. If the sender is not
defective, the problem could be elsewhere; possibly
in a shorted wire, improper-running engine, improper
or low coolant, obstructed or faulty radiator, coolant
pump, loose fan belt, defective instrument display,
etc.
5. Close and secure engine cover.
9.11.7
Engine Oil Pressure Sender
The engine oil pressure sender is located below the
injector pump.
a.
Engine Oil Pressure Sender Removal
1. Open engine cover. Allow engine to cool.
2. Disconnect the negative (-) battery cable at the
negative (-) battery terminal.
3. Unplug the engine oil pressure sender connector
from the wiring harness connector.
4. The sender is threaded into the engine block.
Remove the sender.
b. Engine Oil Pressure Sender Inspection and
Replacement
Inspect the sender and the wiring harness connector
terminals for continuity. Replace a defective or faulty
sender with a new sender.
c. Engine Oil Pressure Sender Installation and
Testing
1. Thread the engine oil pressure sender into the
engine block snugly, then connect the sender
connector to the wiring harness connector.
2. Connect the negative (-) battery cable to the negative
(-) battery terminal.
3. Check for proper oil level.
4. Start the engine, and observe the operator’s display
for warning indication. If the sender is not defective,
the problem could be elsewhere; possibly in a
shorted wire, improper-running engine, low oil,
obstructed or faulty oil pump, defective instrument
display.
5. Close and secure engine cover.
9.11.8
Fuel Level Sender
a. Fuel Level Indicator Testing
1. The fuel level sender wiring harness leads can be
accessed from the top of the fuel tank. Disconnect
the fuel level sender wiring harness leads. With the
help of an assistant, touch both harness leads
together.
2. From the operator’s cab, have the assistant turn the
ignition key switch to the RUN position. DO NOT
start the engine. Observe the fuel level indicator
needle on the operator’s instrument cluster. The
reading must be at the FULL mark.
3. Turn the ignition key switch to the OFF position. The
fuel level indicator needle should return to the
EMPTY position.
b. Fuel Level Circuit Tests
If the fuel level sender is suspected of giving a false
reading, perform the following checks:
1. If the fuel level indicator needle does not move,
check the fuel tank for fuel.
2. Check for loose or defective wiring, faulty ground
connections, and corrosion on the fuel tank sender
and wiring lead.
3. If the fuel level indicator needle does not move after
the ignition key switch is turned to the RUN position,
use a test lamp to determine whether current is
flowing from the ignition switch to the fuel level
sender.
4. If the fuel level indicator does not move and a faulty
or defective fuel level sender in the fuel tank has
been ruled out, and in addition, wiring and
connectors have been checked and ruled out, the
fuel level indicator is defective and must be replaced.
5. Check that the ignition terminal has current and that
the fuse in the fuse panel is not blown.
6. Check for broken, shorted, frayed, disconnected or
damaged wiring between the fuel level indicator
wiring at the cab, fuse and relay panel, ignition key
switch, and from the fuel level sender on the fuel
tank through the wiring in the cab.
7. Check the fuel level sender. A defective fuel level
sender in the fuel tank may also prevent the fuel
level indicator from moving. Refer to Section 9.5,
“Electrical System Schematics,” for further
information.