2 cylinder pressure checking, Cylinder pressure checking – JLG 4017 Service Manual User Manual
Page 118
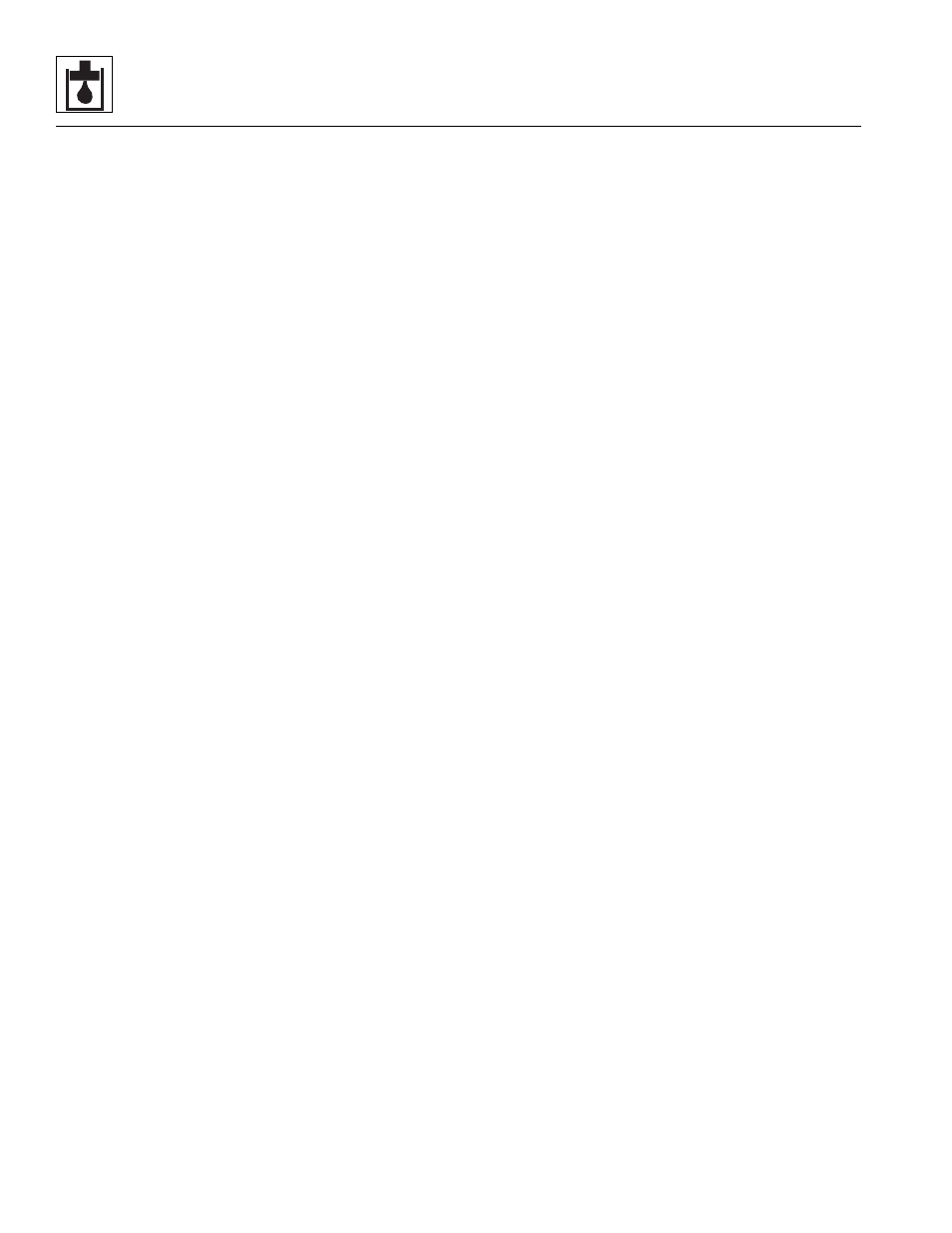
Hydraulic System
8.18
4017
b. Cylinder Cleaning Instructions
1. Discard all seals, back-up rings and o-rings. Replace
with new items from seal kit to ensure proper
cylinder function.
2. Clean all metal parts with an approved cleaning
solvent such as trichlorethylene. Carefully clean
cavities, grooves, threads, etc.
Note: If a white powdery residue is present on threads
or parts, it can be removed by using a soft brass wire
brush. Wipe clean with Loctite Cleaner prior to
reassembly.
c. Cylinder Inspection
1. Inspect internal surfaces and all parts for wear,
damage, etc. If the inner surface of the cylinder
barrel does not display a smooth finish, or is scored
or damaged in any way, replace the barrel.
2. Remove light scratches on the piston, head gland,
rod or inner surface of the cylinder barrel with a 400-
600 grit emery cloth. Use the emery cloth in a rotary
motion to polish out and blend the scratch(es) into
the surrounding surface.
3. Check the piston rod assembly for run-out. If the rod
is bent, it must be replaced.
d. General Cylinder Assembly Instructions
1. Use the proper tools for specific installation tasks.
Clean tools are required for installation.
2. Install new seals, back-up rings and o-rings on the
piston and new seals, back-up rings, o-rings and
bearing on the head gland.
Note: The extend/retract cylinder has a spacer that
MUST be installed over the rod
AFTER
the head gland
and BEFORE the piston head.
3. Fasten the rod eye in a soft-jawed vise, and place a
padded support under and near the threaded end of
the rod to prevent any damage to the rod.
IMPORTANT: Protect the finish on the cylinder rod at all
times. Damage to the surface of the rod can cause seal
failure.
4. Lubricate and slide the head gland over the cylinder
rod. Install the piston head on to the end of the
cylinder rod. Loctite and install the set screw in the
piston head. Refer to Section , “,” for torque
specifications for the piston head and the set screw.
IMPORTANT: Avoid using excess force when clamping
the cylinder barrel in a vise. Apply only enough force to
hold the cylinder barrel securely. Excessive force can
damage the cylinder barrel.
5. Place the cylinder barrel in a soft-jawed vise or other
acceptable holding devise.
IMPORTANT: When sliding the rod and piston assembly
into the cylinder barrel, prevent the threaded end of the
cylinder barrel from damaging the piston head. Keep the
cylinder rod centered within the barrel to prevent binding.
6. Carefully insert the cylinder rod assembly into the
cylinder barrel.
7. Screw the head gland into the cylinder barrel and
tighten with a spanner wrench. Refer to Section
8.8.4, “Cylinder Torque Specifications,” for torque
specifications for the head gland.
8. If applicable, install new counter balance valve into
block on the cylinder barrel.
e. General Cylinder Installation
1. Grease the bushings at the ends of the hydraulic
cylinder. Using an appropriate sling, lift the cylinder
into it’s mounting position.
2. Align cylinder bushing and install pin, lock bolt or
retaining clip.
3. Connect the hydraulic hoses in relation to the labels
or markings made during removal.
4. Before starting the machine, check fluid level of the
hydraulic fluid reservoir and if necessary fill to full
mark with Mobilfluid 424® ISO Grade 46.
5. Start the machine and run at low idle for about one
minute. Slowly activate hydraulic cylinder function in
both directions allowing cylinder to fill with hydraulic
oil.
6. Inspect for leaks and check level of hydraulic fluid in
reservoir. Add hydraulic fluid if needed. Shut the
engine OFF.
7. Wipe up any hydraulic fluid spillage in, on, near and
around the machine, work area and tools.
8.8.2
Cylinder Pressure Checking
Attach a 345 bar (5000 psi) gauge to the test port on the
main control valve to check the system pressure. Refer to
Section 8.4.1, “Hydraulic Pressures,” for the circuit
pressure setting.
Note: If a hydraulic cylinder pressure is greater than the
main control valve pressure, increase the main control
valve pressure by adjusting the main relief. Generally,
one half turn clockwise will be adequate to check an