Sure the “o – Gradall LOED 534A Service Manual User Manual
Page 42
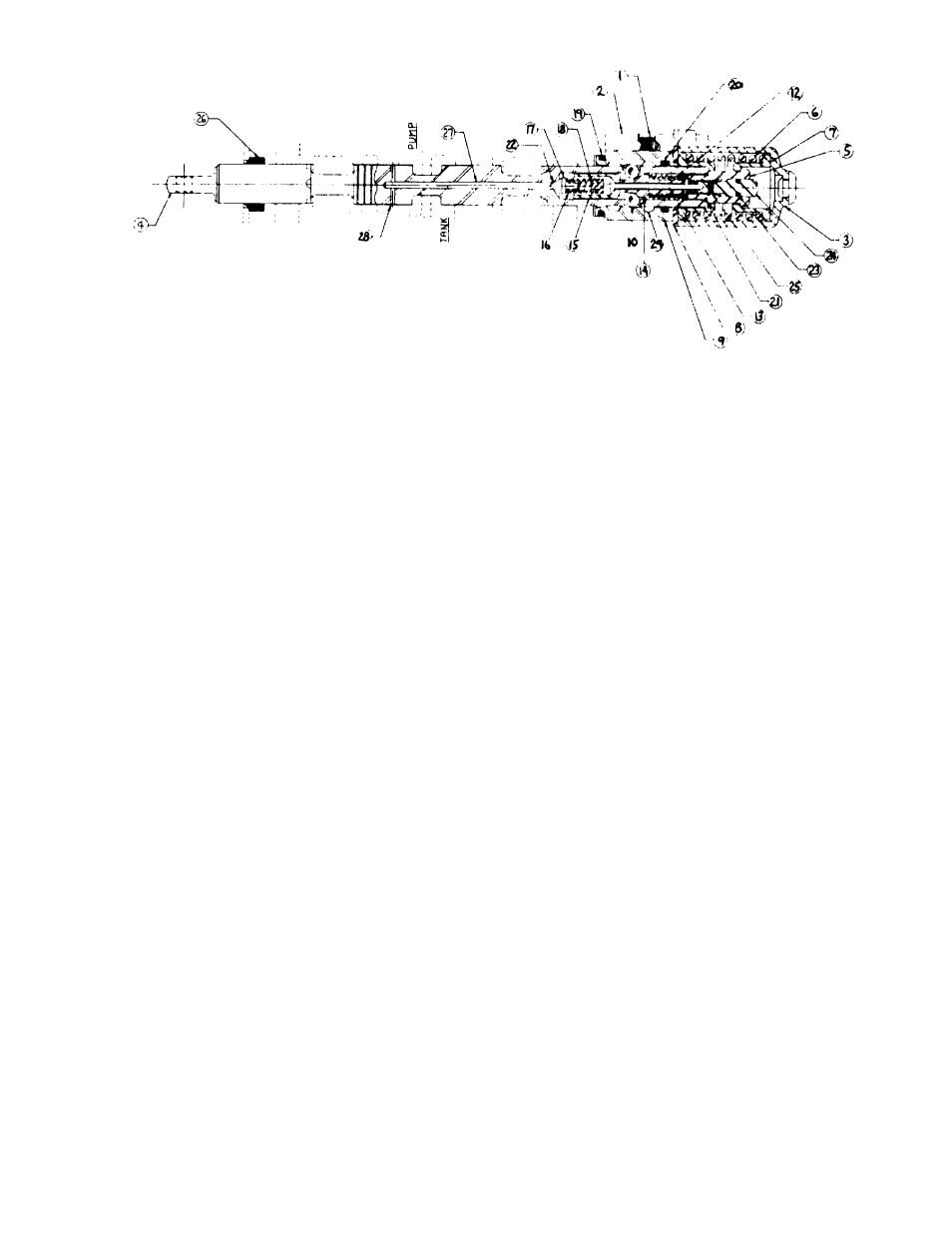
Remove socket head cup screws (No. 1), spacers
(No. 2), and plunger cap (No. 3).
Insert rod through all holes in tang end of plungers
(No. 4) This will prevent the plunger from turning.
Use a special spanner wrench to remove the special
cap screw (No. 5) that holds the plunger spring
(No. 6) to spring seats (No. 7) and seal plate
(No. 8). Remove these parts slowly to prevent them
from being lost.
Take a firm hold on the detent sleeve (No. 9)
slowly rotate while gently pulling the detent sleeve
backwards.
As the detent sleeve (No. 9) is being pulled back-
wards, place the other hand under and around
the plunger (No. 4) so that when the balls (No. 10)
are exposed, your hand will catch them.
Remove rod from the hole in the tang ends of the
plunger (No. 4).
Remove any balls (No. 10) thut are left in the
plunger (No. 4) by slowly rotating the plunger and
catching the balls as they drop out.
Take a firm hold of the plunger (No. 4) and pull it
out of the housing (No. 11). Be careful of any
accumulation of oil that may be in the plunger bore
of the valve housing.
While holding the plunger (No. 4) in your hand, tip
the plunger up and catch the spring (No. 12). ad-
just rod (No. 13). cam (No. 14), sleeve (No. 15),
spring (No. 16), poppet (No. 17), and spring guide
(No. 18) that is inside of the plunger.
The seal (No. 26) at the tang end of the plunger
(No. 4) is serviced in the same manner as for the
spring-centered plunger previously discussed
on page B-7.
To replace the “O” ring (No. 19) on the outside of
the detent sleeve (No. 9), insert a small screw
driver or similar instrument under the “O” ring and
gently left if from its seat. Wash the “O” ring
groove and replace the worn or damaged “O” ring
with a new one being careful not to damage it.
To remove the “O” ring (No. 20) from the detent
sleeve (No. 9), use a thin sharp instrument to get
behind the “O” ring to extract it from the groove.
If you are unable to get an instrument behind the
“O” ring, insert the instnument into the “O” ring
and remove it from the groove. Before inserting
a new “O” ring into the groove be
sure the “O”
MAINTENANCE PROCEDURES - FORWARD - REVERSE VALVE
(Disassembly)
Step 1:
Step 2:
Step 3:
Step 4:
Step 5:
Step 6:
Step 7:
Step 8:
Step 9:
Step 10:
Step 11:
Step 12:
Continued
Step 13:
Step 14:
Step 15:
Step 16:
Step 17:
Step 18:
Step 19:
42
ring groove is clean and has not been damaged
in any way. Insert plunger (No. 4) through the
detent sleeve until the rear of the plunger is even
with the bottom edge of the inner “O” ring groove.
Lubricate the “O” ring with oil and gently insert
it into the “O” ring groove. Use a thin round edge
tool for this operation. Always proceed with caution
so as not to damage the “O” ring in any way.
Remove the “O” ring (No. 21) on the special cap
screw in same manner as described in Step 12. To
replace the “O” ring, first put the “O” ring partly
over the edge of the threaded end and hold it with
your thumb. Now, insert a small diameter round
edge tool under “O” ring and while using a
circular motion, stretch the “O” ring down and
over the threads to the “O” ring seat. NEVER roll
the “O” ring over the threads to the seat.
Inspect adjust rod (No. 13.) If this rod is bent,
r e p l a c e i t w i t h a n e w o n e .
Check the face of the small poppet (No. 17) and
the poppet seat (No. 22) inside of the plunger
(No. 4). If poppet face (No. 17) or poppet seat in
the plunger is worn or marred, use a fine lapping
compound on the poppet and gently lap these parts
until seat and poppet face are free of any irregu-
larities. Be sure to cleanse both the poppet and
the inside of the plunger of any lapping compound.
If “O” ring (No. 23) on adjust screw (No. 24)
needs to be replaced, back out adjust screw from
special cap screw (No. 5); remove the “O” ring
and replace it with a new one.
To replace nylon insert (No. 25), first remove it
from the adjust screw (No. 24) using a rod or drill
with an O.D. a little smaller than the I.D. of the
hole. Install a new insert making sure the insert
fits snug in the hole and does not protrude past the
crest of the threads on the adjust screw.
NOTE: If adjust screw (No. 24) has been turned
in the special cap screw (No. 5) or removed.
this will change the setting of the kickout pressure
and must be reset (Step 19).
To reset the kickout pressure setting, first install
a pressure gage in the cylinder port line, which is
in communication with the cylinder port for this
plunger. Move the plunger into an operating position
and apply pressure at high idle. Adjust in this
manner until desired kickout pressure is reached.
Never set the plunger kickout pressure higher than
the main relief valve pressure setting.
FIGURE 41