Gradall LOED 534A Service Manual User Manual
Page 39
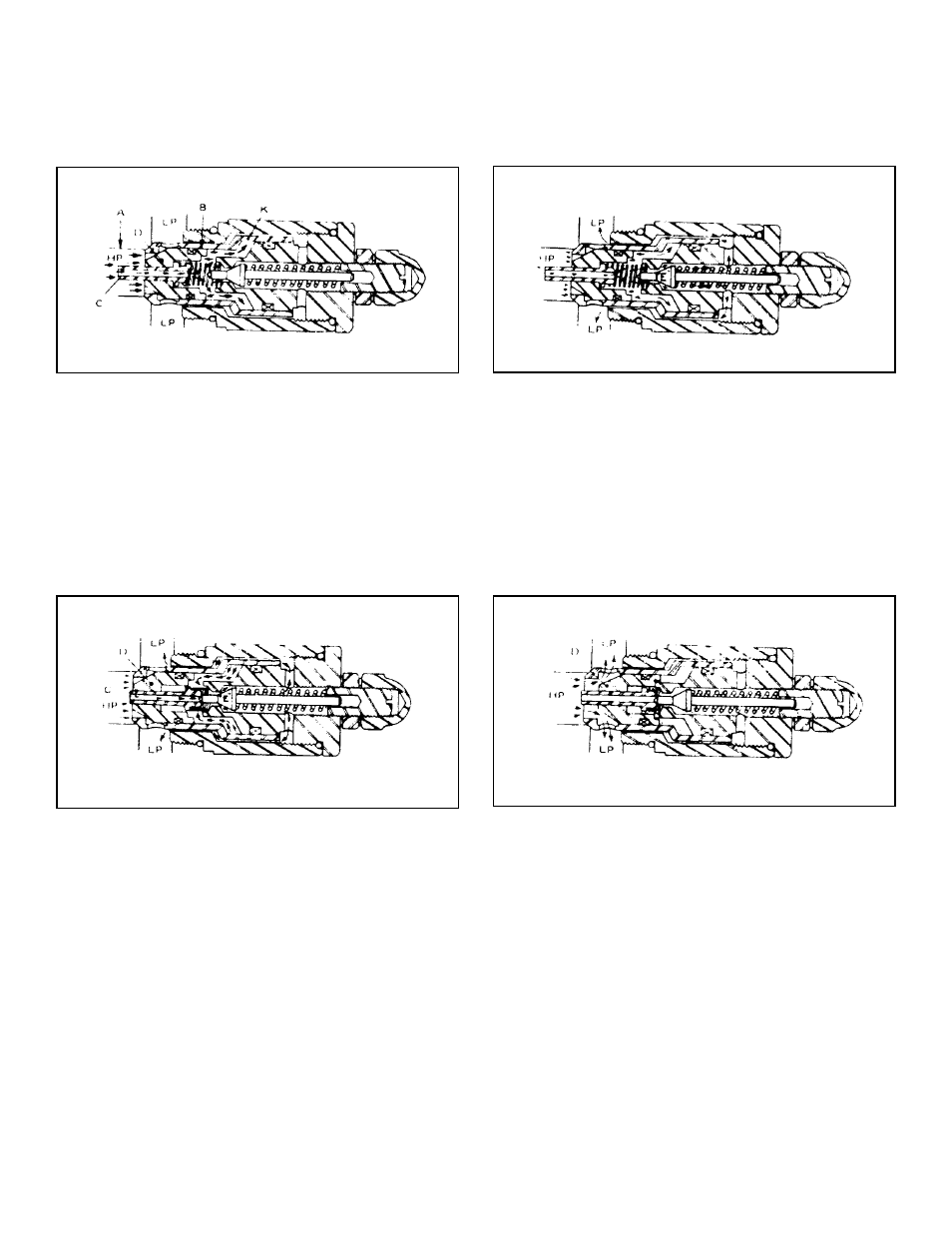
MAINTENANCE PROCEDURES - RELIEF VALVES
A combination cylinder relief valve and anti-void unit is illustrated in Figure 5 8. The service port
relief valve is designed to control the maximum pressure obtained in the circuit. By discharging oil to the
low pressure return passage, the service port relief valve provides maximum structural protection of circuit
c o m p o n e n t s . I t w i l l f u n c t i o n w h e t h e r t h e p l u n g e r i s i n t h e n e u t r a l o r o p e r a t e p o s i t i o n .
Step 1
The normal operating sequence for the cylinder
port relief is as follows - the relief is in
communication between the cylinder port “HP”
and low pressure “LP”. Oil is admitted through
the hole in piston “C” and because of the differ-
ential area between diameters “A” and “B” main
poppet “D” and check valve poppet “K” are
tightly seated. (See Fig. 35)
Step 3
The loss of oil behind piston “C” effected by the
opening of pilot poppet “E”, causes piston “C”
to move back and seat against pilot poppet “E”.
This shuts off the oil flow to the area behind main
poppet “D”, and causes a low pressure area in-
ternally. (See Fig. 37)
Step 2
The oil pressure in the cylinder port “HP” has
reached the setting of the pilot poppet spring force
and unseats the pilot poppet “E” and oil flows
around the poppet - through the cross drilled holes
a n d t o t h e l o w p r e s s u r e a r e a “ L P ” . ( S e e F i g 36 )
Step 4
The imbalance of pressure on the inside as com-
pared to that of the cylinder port “HP”, forces
the main poppet “D” to open and relieve the oil
directly to the low pressure chamber “LP” in the
valves. (See Fig. 38)
39
FIGURE 35
FIGURE 36
FIGURE 37
FIGURE 38