Operation – NOVUS N2020 Controller User Manual
Page 3
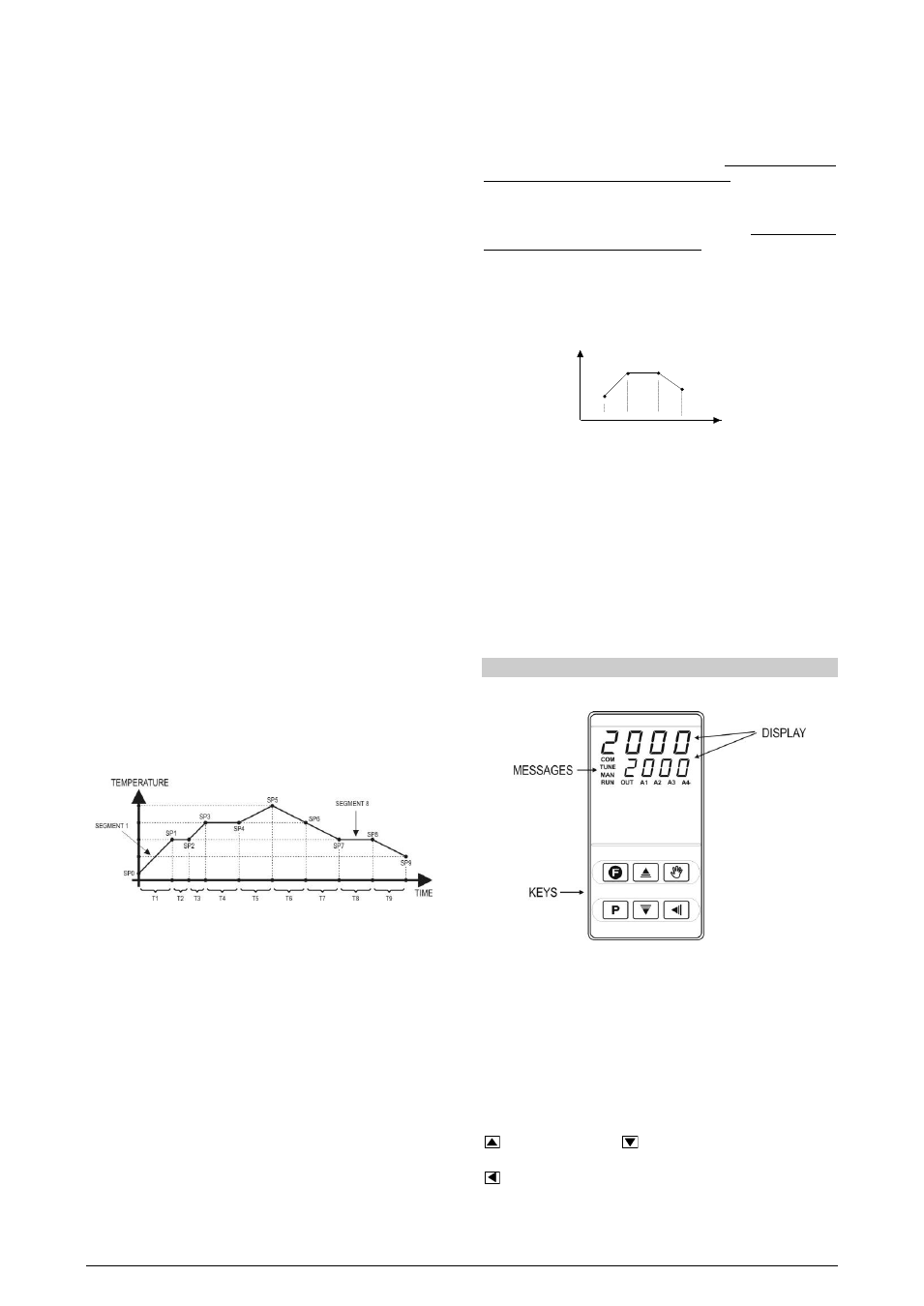
N2020 Controller
NOVUS AUTOMATION
3/7
LBD – LOOP BREAK DETECTION
The parameter defines a time interval, in minutes, within which the
PV is expect to react to a control output signal. If the PV does not
react properly within the time interval configured in lbd.t, the
controller interprets this as a control loop break and signals this
occurrence in the display.
A LBD event may be sent to any output channel. Simply configure
the LBD function to the desired output channel (OUT1 or OUT2): the
selected output will be activated when a LBD condition is detected.
When the Lbd.t parameter is programmed with 0 (zero), the LBD
function is disabled.
The LBD is useful in detecting system failures, such us defective
sensors or actuators, loads and power supply, among others.
SAFE OUTPUT VALUE WITH SENSOR FAILURE
This function defines an output value (user defined) to be assigned to
the control output in the event of a sensor failure.
When the input sensor is identified as broken, the controller switches
the control mode to MANUAL while forcing MV to assume the user
configured value in the 1E.ov parameter. This function requires that
one of the alarms be configured as 1Err and the 1E.ov parameter
(control output percentage) programmed with a value other then 0
(zero).
Once this function is triggered, the controller remains in SAFE mode
(MANUAL control output) even after the sensor failure appears to be
fixed. The operator intervention is required for switching back to
AUTO mode.
1E.ov values are only 0 and 100 % when in ON/OFF control mode.
For PID control mode any value in the range from 0 to 100 % is
accepted.
OFFSET
Allows fine adjustments to the PV reading for compensation of
sensor error.
PROGRAMS OF RAMP AND SOAK
The controller allows the creation of one ramps and temperature
soaks program. This program is created from the values definition of
SP and time intervals, defining up to nine (9) program segments.
The figure below shows a program model with 9 segments:
Fig. 04 - Example of ramps and soaks program
The program created is storage permanently on the controller’s ram.
It may be always changed, executed and repeated whenever
necessary.
For the program’s execution:
1- Turn off the outputs (rvn= NO);
2- Enable the parameter execution E.Pr= yes;
3- Start-up the outputs: (rvn= yes).
Once the program execution is started, the controller starts to create
automatically the SP values defined for each program segment. The
SP adjustment on the indication screen is blocked.
Program Toleration Function - PtoL
The program toleration function “PtoL” defines the maximum error
limit between PV and SP values during the program execution. If this
limit is exceeded, the time counting of the segment (Pt1...Pt9) is
stopped until the error is within the established tolerance. With a
value >0 the user indicates in its program that priority must be given
to PV in relation to the indeterminate value times.
If 0 is programmed in the tolerance (Ptol= 0), the controller
executes the program defined without considering eventual errors
between PV and SP. Thus, the user defines that the priority has to be
given for the execution time of the program.
Programs with few Segments
For the execution of programs with few segments, it is enough to
program 0 (zero) for the time interval of the segment, which
succeeds the last segment of the desired program.
SP
Time
T1
T2
T3
SP0
SP1
SP2
SP3
T4=0
Fig. 05 - Program example with three segments
Successive Repetitions of a Program
The program created may be repeated for several times, always
restarting immediately after the end of each execution.
The parameter rPt.p (rePeat Program) in the Programs cycle
configures the number of times the program must be REPEATED. It
determines the number of executions besides the first execution.
With 0, the program is executed once. It won’t repeat.
Important: After the last execution of the program, all controller
outputs will be turned off and the RUN parameter is OFF.
OPERATION
The controller’s front panel, with its parts, can be seen in the Fig. 06:
Fig. 06 - Identification of the parts referring to the front panel
Display: It shows the variable measured, configuration parameters
symbols and its respective values/conditions.
TUNE indicator: Stays ON while the controller is in tuning process.
OUT indicator: It shows the instantaneous state of the controller
output(s).
A1 and A2 indicator: signalize the occurrence of alarm situation.
P key: Key used to forward the successive parameters and
parameters cycles.
Increment key and
Decrement key: allow altering the
values / conditions of the parameters.
Back key: allow altering the values of the parameters.