Configuration parameters – NOVUS Controller N3000 User Manual
Page 5
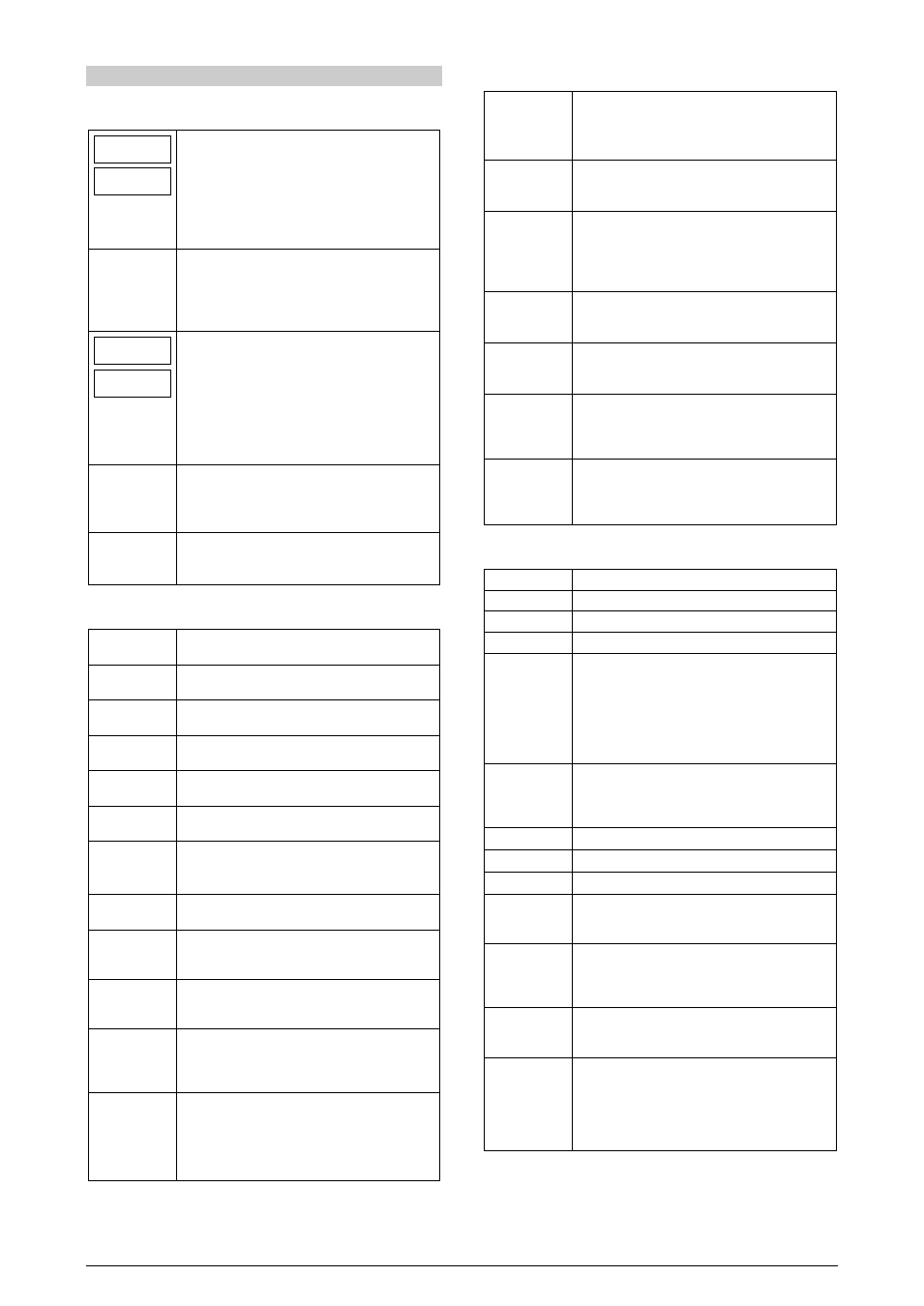
Controller N3000
NOVUS AUTOMATION
5/9
CONFIGURATION PARAMETERS
OPERATION CYCLE
PV Indication
(Red)
SV Indication
(Green)
PV AND SV INDICATION: The status display shows
the present value of PV (Process Variable). The
parameter display shows SV (Set Variable).
The status display shows “- - - -“ whenever PV exceeds
the maximum range or there is no signal at the input. In
case of hardware error the status display will show Ern,
where n is the error code.
avto
CONTROL MODE: YES indicates automatic control
mode (closed loop, PID or ON/OFF). NO indicates
manual control mode (open loop). Bumpless transfer
from auto ↔ to manual mode is available. If in doubt
program YES.
PV Indication
(Red)
MV Indication
(Green)
MANIPULATED VARIABLE VALUE (MV): The upper
display shows PV value and the lower display shows
the percentage of MV applied to the control output.
When in manual control the MV value can be manually
changed. When in auto mode the MV value can only be
viewed.
To distinguish the MV display from the SV display, the
MV is shown flashing intermittently.
Pr n
RAMP AND SOAK PROGRAM SELECTION: Selects
the ramp and soak program to be executed (7
programs possible). Refer to chapter 7 for R&S
description.
rvn
CONTROL ENABLE: YES means that the control
output and alarms are enabled and NO means they
are disabled.
AUTO TUNING CYCLE
atvn
AUTO-TUNE: YES enables the auto tuning of the PID
parameters and NO disables it.
Pb
PROPORTIONAL BAND: Percentage of maximum
input span. 0 to 500 %. Select zero for ON/OFF control.
xyst
CONTROL HYSTERESIS (in engIneering. units): This
parameter is only shown for ON/OFF control (Pb=0).
‘ ir‘
INTEGRAL RATE: Integral time constant in repetitions
per minute (Reset).
dt
DERIVATIVE TIME: Derivative time constant, in
seconds.
(t
CYCLE TIME: PWM period in seconds. Can only be
viewed if proportional band is other than zero.
act
CONTROL ACTION: For Auto Mode only.
•
rE Reverse Action usually used for heating.
•
dir Direct Action usually used for cooling.
bias
Offset for MV (manual reset). Range: -100 % to +100
%. Default value: 0.
ovll
OUTPUT LOW LIMIT: minimum percentage value for
MV (Manipulated Variable) when in automatic control
and PID. Default value: 0.0 %
ovxl
OUTPUT HIGH LIMIT: Maximum percentage value for
MV when in automatic control and PID. Default value:
100.0 %
sfst
SOFT START: Time in seconds during which the
controller limits the MV value progressively from 0 to
100%. It is enabled at power up or when the control
output is activated. If in doubt set zero.
Sp.a1
Sp.a2
Sp.a3
Sp.a4
ALARM PRESET: Tripping point for alarm 1, 2, 3
and 4.
RAMP AND SOAK PROFILE PROGRAMMING CYCLE
tbas
TIME BASE: Selects the time base for the ramp and
soak. Valid for all profile programs.
0
- PT1 to PT7 values are in seconds;
1 - PT1 to PT7 values are in minutes;
Pr n
PROGRAM TO BE VIEWED: Selects the ramp and
soak profile program to be edited/viewed in the
following cycle prompts (7 programs available).
ptol
RAMP AND SOAK TOLERANCE: maximum deviation
between PV and SV. Whenever this deviation is
exceeded the time counter is halted until deviation
lowers to within the tolerance. Set zero to disable this
function.
Psp0
Psp7
RAMP AND SOAK SET POINTS (0 to 7): Set of 8 SV
values which define the ramp and soak profile
segments. See also PT1 to 7 and PE1 to 7 below.
Pt1
Pt7
RAMP AND SOAK SEGMENTS TIME (1 to 7): Set of
7 time intervals in minutes or seconds (9999 max.) for
the 7 segments of the ramp and soak program.
Pe1
Pe7
RAMP AND SOAK EVENT (1 to 7): Set of 7 values
that define which alarms must be activated during a
ramp and soak program segment. Alarm function
depends on “rS” setting (Table 3).
lp
LINK TO PROGRAM: Number of the next profile
program to be linked to follow the current profile.
Profiles can be linked to make larger programs of up
to 49 segments.
ALARM CYCLE
Fva1
ALARM 1 FUNCTION: Select options from Table 3.
Fva2
ALARM 2 FUNCTION: Select options from Table 3.
Fva3
ALARM 3 FUNCTION: Select options from Table 3.
Fva4
ALARM 4 FUNCTION: Select options from Table 3.
bla1
bla2
bla3
bla4
ALARM BLOCK 1 TO 4: This function blocks the alarm
at power-up when the units is first energized.
YES enables and NO inhibits this blocking function.
When enabled the alarm will not be active at power-up
waiting for PV (Process Variable) to reach a non-alarm
situation. From this point on the alarm will be free to
actuate should a new alarm situation occur.
xya1
ALARM 1 HYSTERESIS: Defines the differential
range between the PV value at which the alarm is
turned on and the value at which it is turned off (in
engineering units).
xya2
ALARM 2 HYSTERESIS: Same as above.
xya3
ALARM 3 HYSTERESIS: Same as above.
xya4
ALARM 4 HYSTERESIS: Same as above.
A1t1
ALARM 1 TIME 1: Defines the time (6500 sec. max.)
during which the alarm 1 output will be ON when
alarm 1 is active. Program zero to disable this function.
A1t2
ALARM 1 TIME 2: Defines the OFF state time for the
alarm 1 output, after being ON during the time
selected on ALARM 1 TIME 1. Program zero to
disable this function.
A2t1
ALARM 2 TIME 1: Defines the time (6500 sec. max.)
during which the alarm 1 output will be ON when
alarm 1 is active. Program zero to disable this function
A2t2
ALARM 2 TIME 2: Defines the time during which the
alarm 2 output will be, after being ON during the time
selected on ALARM 2 TIME 1. Program zero to
disable this function. Table 4 shows the advanced
features that can be achieved with these time
functions.