Special recommendations, Calibration, Input calibration – NOVUS N1500FT Indicator User Manual
Page 8: Output calibration, Serial communication, Features, Electrical connections: rs485 interface, Configuration of serial communication parameters
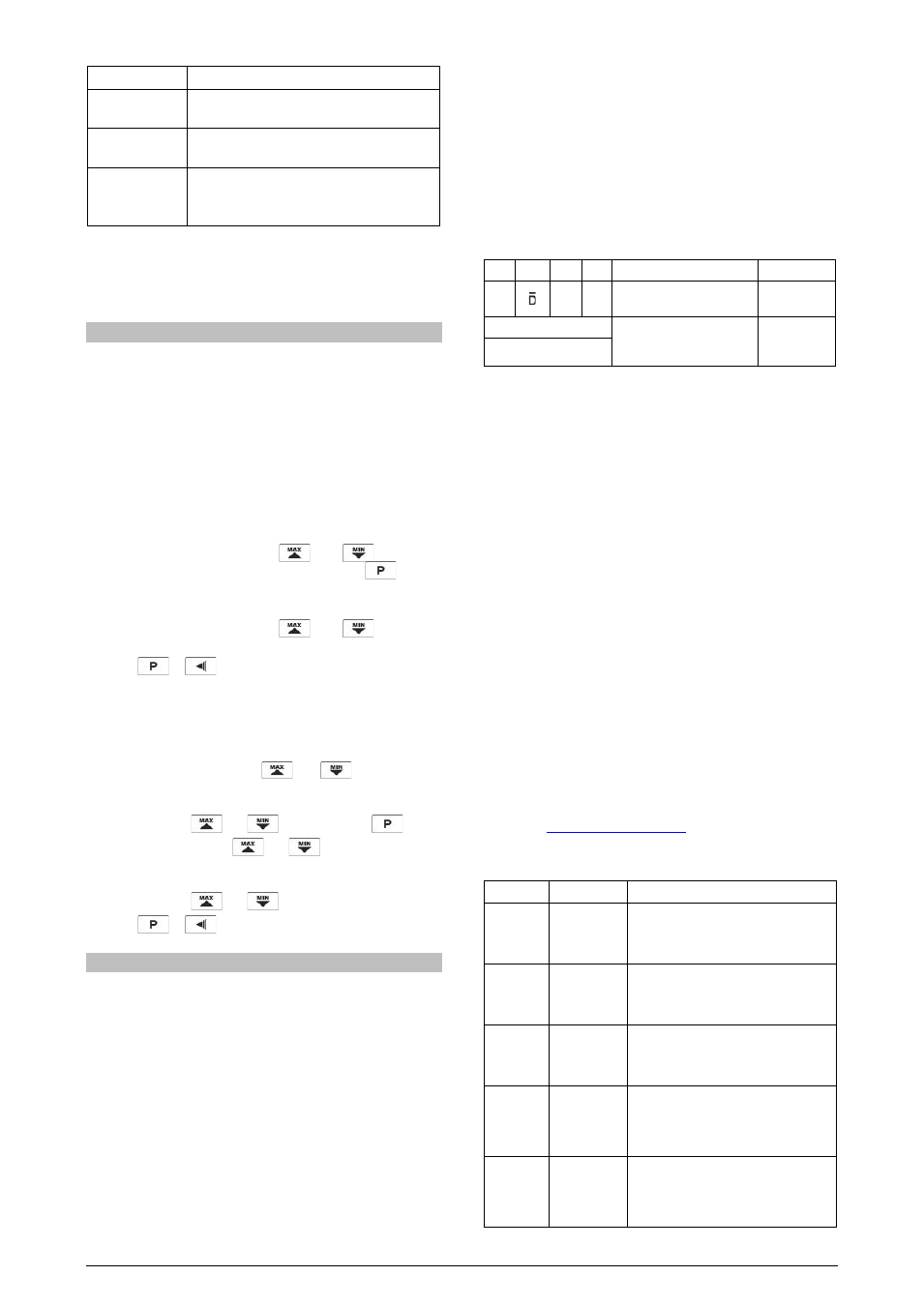
N1500FT Flow Indicator
NOVUS AUTOMATION
8/9
MESSAGE
PROBLEM DESCRIPTION
VVVVV
Value reading is above limits allowed for this
sensor or signal.
nnnnn
Value reading is below limits allowed for this
sensor or signal.
------
Open input. No sensor or signal.
Also displayed in the “feeder” screens in case
no alarm is configured as “feeder”.
SPECIAL RECOMMENDATIONS
Should your indicator be repaired, special care must be taken with
handling. The device must be removed from the case and immediately
placed in an antistatic wrap, protected from extreme heat and humidity.
CALIBRATION
Both analog input and output are factory calibrated, and recalibration
should not be performed by inexperienced operators. If recalibration
of a given range is necessary, proceed as follows.
INPUT CALIBRATION
1. Set input type to be calibrated to 4-20 mA;
2. Program inll (lower limit) and inkl (higher limit) indication
parameters to maximum and minimum values of input type;
3. Apply to entry a signal corresponding to a known indication and
close to its lower limit;
4. Enter calibration cycle with correct password;
5. Access inl( parameter. With
and
keys, have
parameter display show applied value. Then Press
;
6. Apply to entry a signal corresponding to a known indication and
close to its higher limit;
7. Access ink( parameter. With
and
keys, have
parameter display show applied value;
8. Press
or
to exit screen and activate calibration.
OUTPUT CALIBRATION
1. Mount a milliammeter in the analog control output;
2. Enter calibration cycle with correct password;
3. Select oUL( parameter. Use
and
keys so that the
device recognizes the process of calibration of current output.
4. Read current in the milliammeter and enter it in the oUL(
parameter using
and
keys. Then press
;
5. In parameter oUx(, use
and
keys so that the device
recognizes the process of calibration of current output;
6. Read current in the milliammeter and enter it in the oUx(
parameter using
and
keys;
7. Press
or
to exit screen and activate calibration.
SERIAL COMMUNICATION
The indicator may be optionally supplied with a RS485 asynchronous
serial communication interface for communicating with a supervisor
computer (master). The indicator always operates as slave.
Communication is always initiated by the master, which sends a
request to the slave address with which it wants to communicate. The
addressed slave takes control and sends a response to the master.
The indicator takes broadcast type commands (addresses to all
network instruments). For this type of command, the indicator does
not send any reply or acknowledgement.
FEATURES
Signals compatible with RS485 standard. MODBUS (RTU) Protocol.
2-wire connection between 1 master and up to 31 indicators (it is
possible to address up to 247 units) in bus topology.
Communication signals are electrically isolated from the rest of the
indicator.
• Maximum connection distance: 1000 meters.
• Selectable speed; 8 bits of data; 1 stop bit; selectable parity (no
parity, even or odd).
• Start time of response transmission: 100 ms maximum after
receiving the command.
ELECTRICAL CONNECTIONS: RS485 INTERFACE
RS485 signals are:
D1
D
D+
B
Bi-directional data line
Terminal 25
D0
D-
A
Reverse bi-directional data
line
Terminal 26
C
Optional connection that
improves communication
performance.
Terminal 27
GND
CONFIGURATION OF SERIAL COMMUNICATION PARAMETERS
Two parameters must be configured for serial use:
Baud
: Communication speed.
Prty
: Communication parity.
Addr
: Communication address of indicator.
REDUCED REGISTERS TABLE FOR
SERIAL COMMUNICATION
Communication Protocol
Slave MODBUS RTU protocol supported. All configurable
parameters of the indicator may be read and/or written through serial
communication. Writing on registers in broadcast mode using the
address 0 is also allowed.
The following Modbus commands are available:
03 - Read Holding Register
06 - Preset Single Register
05 - Force Single Coil
16 - Preset Multiple Register
Holding Registers Table
The following are the most commonly used registers. For further
information, refer to the Table of Registers for Serial
Communication available for download on the flow indicator
webpag
The registers below are read-only. The ones that are available in a
floating point format require two registers for being 32-bit values.
Address Parameter
Register Description
0000
and
0001
Instantaneous
flow rate
Instantaneous flow value in floating
point (IEEE-754).
0002
and
0003
Totalized Flow Flow totalization value in floating
point (IEEE-754).
0004
and
0005
Non-resettable
Totalized Flow
Grand total flow value in floating point
(IEEE-754).
0013
to
0016
Totalized Flow
Flow totalization value in integer
format (with signal) of 64 bits. The
most significant part is in the first
register.
0017
to
0020
Non-resettable
Totalized Flow
Grand total flow value in integer
format (with signal) of 64 bits. The
most significant part is in the first
register.