Auxiliary digital input and key, Feeder, Manual operation mode – NOVUS N1500FT Indicator User Manual
Page 3: 24 vdc auxiliary power supply, Installation, Installation recommendations, Electrical connections, Power supply connection, Connections for input and output signals
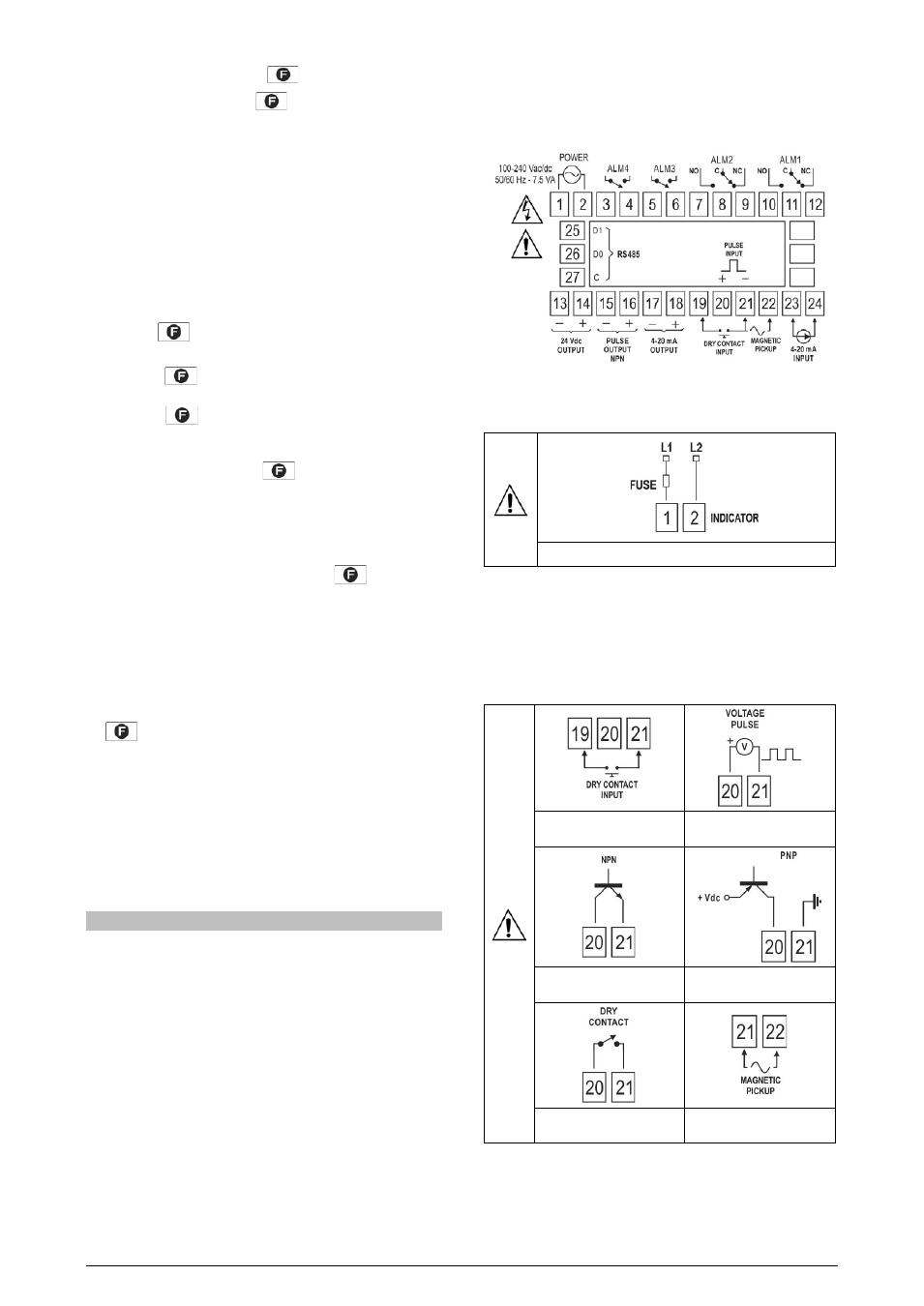
N1500FT Flow Indicator
NOVUS AUTOMATION
3/9
AUXILIARY DIGITAL INPUT AND
KEY
Similarly to a digital input, the
key can be set to zero the
totalizer, freeze the main screen, zero minimum and maximum
readings or control the feeder function.
FEEDER
The feeder function is used to control the volume of fluids based on
its flow rate. It is typically used for storage applications, where there
is a start signal that triggers a relay and the flow rate begins to be
measured. When reaching a given setpoint, this relay is deactivated
to stop flow.
Its use depends on correct configuration of the related alarm.
During the feeder process, it is not possible to change the alarm
setpoint. Process should be reset first to allow it.
Functions of
key and/or digital input, when assigned to the
feeder function:
• When the
key or digital input is activated, the feeder
process is started, activating all relays related to the feeder alarm;
• In case the
key or digital input is activated once again, the
process is frozen and all relays related to the feeder alarm are
deactivated;
• To restart the feeder process,
key or digital input must be
activated for 3 seconds, until the process is restarted, zeroing all
existing feeder indication. This can be done with the process
stopped or running;
• At the end of the feeder process, when alarm setpont is reached,
process values are frozen and all related relays are deactivated.
To restart a new process, just activate the
key or digital
input for all counters to be reset and process will start running;
•
In case of a power shortage, if the feeder batch reset parameter
(
Bat.rst
) is configured as
no
, whenever the equipment
powers up again the process will restore from where it stopped.
This means that, if it was in the middle of a feeder process, all
relays assigned to the feeder alarm will be activated. If the
process was stopped, all counters will keep their values and the
process will remain stopped until it is activated either by the
key or the digital input.
MANUAL OPERATION MODE
In the hardware cycle, outputs can be set manually. This can be
extremely useful for tests and simulations. After exiting the cycle,
outputs go back to their regular status.
24 VDC AUXILIARY POWER SUPPLY
DC power supply models provide a 24 Vdc output for field transmitters.
INSTALLATION
The indicator must be installed on a panel. To do so, remove the two
plastic clamps, introduce the device in the panel cutout and put the
clamps back from the rear side of the indicator.
INSTALLATION RECOMMENDATIONS
• Input signal conducers should be disposed in the system
separately from output conducers and power conducers,
preferably in grounded electrodes.
• Instruments should be powered through a dedicated network.
• For control and monitoring applications it is vital to consider what
might happen if any part of the system fails. The alarm internal
relay does not ensure total protection.
• It is recommended to use RC FILTERS (47 Ω and 100 nF, series)
in contactor coils, solenoid coils, etc.
ELECTRICAL CONNECTIONS
All the inside can be removed without the need to undo the electrical
connections. Disposition of signals in the rear panel of the indicator is
shown in Fig. 1.
Fig. 1 – Rear panel connections
POWER SUPPLY CONNECTION
Fig. 2 – Power supply terninals
CONNECTIONS FOR INPUT AND OUTPUT SIGNALS
It is important that these connections are well made, with signal or
sensor wires securely attached to rear panel terminals. Check the
“Specifications” section for the range of the input signals.
The images below show connections for different input types:
Fig. 3 – Auxiliary digital input
connection
Fig. 4 - Flow pulse input –
Voltage signals
Fig. 5 -
Flow pulse input –
NPN signals
Fig. 6 - Flow pulse input –
PNP signals
Fig. 7 - Flow pulse input – Dry
contact signals
Fig. 8 – Coil Signal connection
(magnetic pickup)